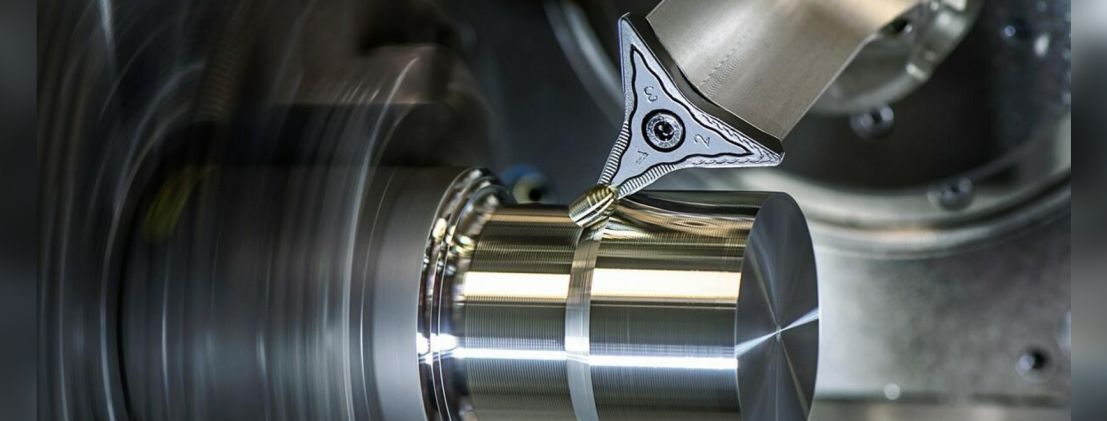
Tool manufacturer is revolutionizing in-house production with CERATIZIT FreeTurn
Only those who rely on advanced and future-oriented tool solutions these days will remain competitive in the long term. For this reason, those responsible at the Ceratizit production site in Besigheim have decided to use the new turning technology High Dynamic Turning (HDT) and the FreeTurn tools to manufacture their high-quality tools - and have not been disappointed.
Since its first presentation at AMB 2018, the High Dynamic Turning (HDT) turning process, which has won numerous innovation awards, has been making waves all over the world of machining. By using the milling spindle in turn-mill centers, the cutting angle of the dynamic FreeTurn tool from Ceratizit can adjust 360° for optimal use in every position of the workpiece. This creates several very interesting opportunities. First, flexible machining of almost any workpiece contour is possible. Also, chip breaking can be optimally influenced. It is even possible to achieve higher feed rates and tool life with maximum stability as additional positive effects of the dynamic turning method.
High Dynamic Turning with FreeTurn
Placing the tool on the workpiece using a milling spindle - what first sounded like science fiction to conventional turning is now a reality. The new process and the dynamic FreeTurn tools are taking over more and more manufacturing companies. The production manager for special tools, Dr. Thomas Ledermann at the CERATIZIT tool manufacturing location in Besigheim has long had an eye on the revolutionary turning process. "Here in Besigheim we produce tools of the highest quality and use highly optimized processes for this. The possibilities offered by High Dynamic Turning and FreeTurn really appealed to us. Therefore, we decided to implement the turning process with us to test whether it really does what it claims.” explains Thomas Ledermann.
The machining expert found the possibility of tool reduction particularly exciting because, according to the manufacturer Ceratizit, a single FreeTurn indexable insert can be used for various turning applications. For Mr. Ledermann, this fact alone is a good argument for switching to HDT, as it saves considerable tool costs.
Tool Savings
Paul Höckberg, Product Manager for Turning at CERATIZIT, accompanied the system changeover in Besigheim and agrees with Thomas Ledermann: “The most obvious advantage of HDT and FreeTurn are the tool cost savings. Where we conventionally needed several tools for roughing, finishing, contour, face, and longitudinal turning, we now only need one dynamic FreeTurn tool,” says Höckberg. “However, when using FreeTurn in Besigheim, we quickly realized that this is not the only advantage. In terms of process speed and energy efficiency, too, the dynamic turning process was ahead of conventional machining.” reveals Thomas Ledermann.
The DMG Mori CTX beta 1250 TC was selected as the machine, which fulfills all the requirements for turning in a highly dynamic manner. “This machining center is widespread on the market and HDT ready. This confirms that many manufacturing companies are able to use our FreeTurn technology,” emphasizes Höckberg. The component, a base body of an indexable insert drill, was then optimized and implemented using the Siemens Sinumerik 840d controller and a 5-axis simultaneous cycle from Open Mind - with an astonishing result.
Amazing Cutting Speeds
“As expected, we were able to reduce the number of tools required. Instead of the previously three different tools, we now only manufactured the component with one FreeTurn tool,” says Ledermann. But saving two tools was not everything. What really astonished the production manager was the cutting data that was used. “We processed the component with a cutting speed of VC 220 m / min, a feed rate of f 0.48 mm / rev and an infeed depth of ap 4 mm. A cutting speed of 400 m / min was possible when finishing”. FreeTurn is therefore a far superior alternative to our conventional tools,” summarizes Thomas Ledermann.
Product manager Höckberg is also amazed by this result: “We knew our FreeTurn was good. However, we would never have thought it possible to drive such enormous cutting speeds in mild steel (X40CrMoV51)”. Another comparison to the previous conventional processing clearly shows that the switch to HDT and FreeTurn has paid off. "We were able to save 2.25 minutes of production time, € 3.53 production costs and 0.42 kW / h of energy per component".
Securing a Competitive Advantage
Due to this positive result, High Dynamic Turning and FreeTurn will certainly find its way into everyday production at Besigheim. Programming is carried out using the CAD / CAM software Siemens NX, which is also ideal for HDT. "We are already looking forward to gradually converting our production to High Dynamic Turning and FreeTurn," says Thomas Ledermann. "This way we can secure a significant competitive advantage."
How FreeTurn Works
In High Dynamic Turning, instead of the classic, static adjustment with a clamp holder, the milling spindle is used to position the FreeTurn tool on the workpiece to be machined. Since the milling spindle rotates around its own axis with a clearance angle of 360 °, a completely flexible adjustment to the workpiece is possible - the machining can be controlled in almost all directions. The advantage: Different operations can be carried out with just one insert, and there is no time-consuming tool change. The cutting edges of the indexable inserts can also be designed for various processes. This means that all known turning operations such as roughing, finishing, contour turning, face turning, and longitudinal turning can be carried out with just one tool. Therefore, it is understandable that manufacturing companies all over the world want to use this added value for their own production.