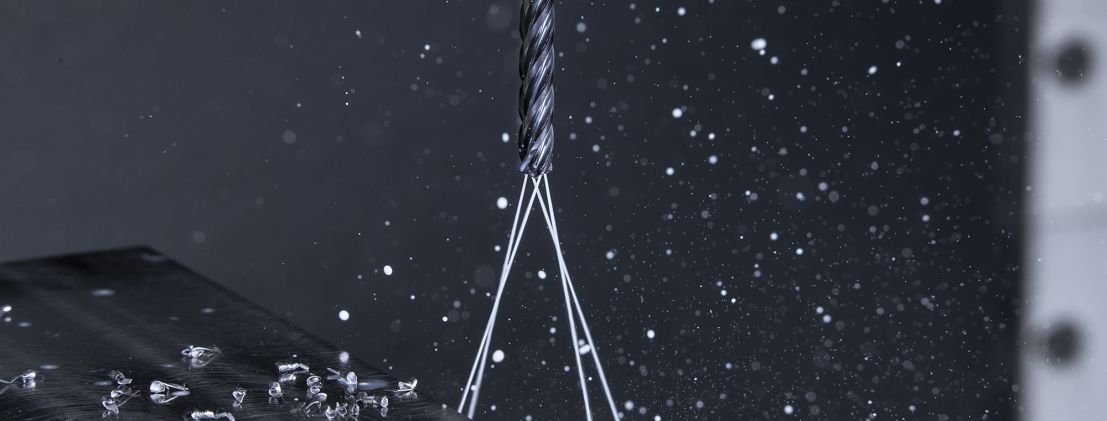
Ceratizit releases high-feed drill with four cutting edges
Many innovations, firsts or revolutions often turn out to be nothing more than facelifts or updates once you look under the bonnet. The same cannot be said for the WTX HFDS from Ceratizit – which is the first four-edged high-feed drill from de tool supplier. Impressive cutting data and tool life in steel and cast iron materials clearly demonstrate the fourth cutting edge is not there just for show.
The superlatives that preceded the launch of the new drill have pushed expectations among potential users a notch higher: innovative, unprecedented results, a new benchmark in the drill segment. These are the criteria by which the world's first high-feed drill with four effective cutting edges, the WTX HFDS from Ceratizit, will be judged.
Speed and endurance
"No matter what we put it up against, the WTX HFDS is faster every time! It reduces machining times by up to 66% in comparison with standard two-edged and three-edged high-speed and high-feed drills!" says a delighted Felix Meggle, Product Manager Drilling Tools at Ceratizit. Designed and engineered as a specialist tool for steel and cast iron, the drill cuts through these materials like a knife through butter, "at high speed and with the ultimate in precision. If we replicated that performance on the road, we'd be getting a knock on the door from the police!" adds Meggle. And for those of you thinking that this just means you'll be changing the tyres sooner, think again: this four-edged marvel is not just as quick as lightning, it will run rings round any competitor in an endurance race too."
Mass and class
"The WTX HFDS is far more than just a speed and productivity merchant. It also delivers high quality in terms of positioning accuracy, tolerance and the roundness/cylindricity of the holes produced," explains Meggle. Field trials showed an average positioning accuracy of 0.03 mm for the entire hole depth; an astonishing result in light of the cutting data. "With a WTX HFDS Ø6.80 mm, 5xD we can cut into 1.7331 / 16MnCr5 at a cutting speed of Vc= 120 m/min and a feed per revolution of F= 0.50 mm/U to produce holes with an H7 tolerance," adds Meggle by way of example. All this is made possible by the special pyramid-shaped drill tip, which is completely unlike a conventional chisel edge and allows for exceptional centering of the drill. Four continuous spiral coolant holes ensure optimal cooling of every cutting edge, while the tool core still remains extremely stable. In addition, the WTX HFDS produces only a slight burr when entering and exiting the hole.
Dragonskin protection
A global first like the WTX HFDS leaves nothing to chance, as demonstrated by the legendary Dragonskin DPX14S coating from Ceratizit. The TiAlN nanolayer is resistant to application temperatures of 1000°C, clearing the last potential obstacle in the way of the new four-edged solid carbide drill delivering its epic levels of performance.