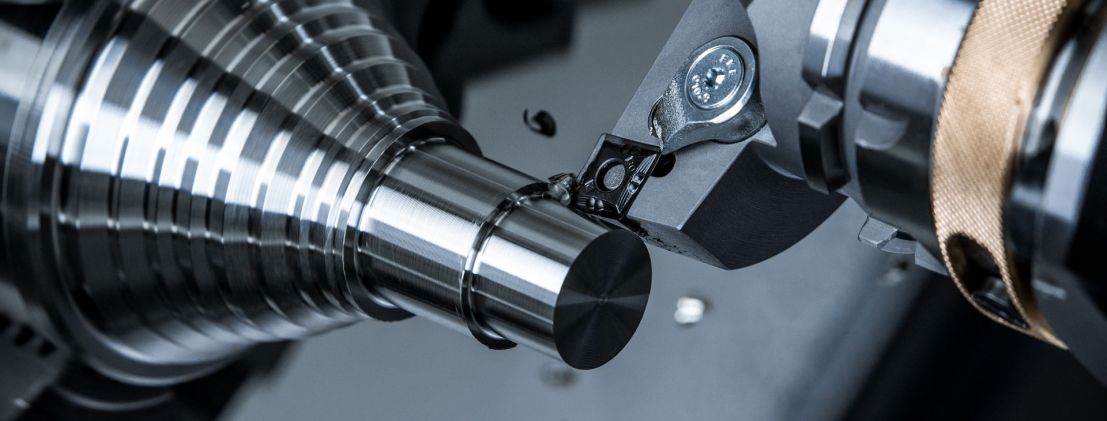
Ceratizit carbide grades boost turning performance with stainless steels
For turning stainless steels – regardless of whether they be cast iron blanks, forged parts or semi-finished parts – Ceratizit is sure to have the optimum cutting insert in its range. In addition to the established CTPM125 carbide grade, two new cutting materials now round off our product range: the more wear-resistant CTCM120 and the tougher CTCM130. Thanks to the latest Dragonskin coating, both grades are high performers and process-secure.
Ceratizit launched two new carbide grades which are recommended for turning austenitic, stainless steels and supplement the existing all-rounder cutting material. Development focused on the most frequently used stainless steels V2A (e.g. 1.4301) and V4A (1.4545). The aim was to provide the user with a wider selection of cutting inserts, which perfectly and seamlessly cover every application – from roughing to fine machining.
The universal PVD-coated carbide grade CTPM125 has proved its worth over many years. It is characterised by a well-balanced ratio between toughness and elevated-temperature hardness and promises to deliver high reliability when machining all stainless steels.
New grades
The new addition to the range is the CVD-coated, highly wear-resistant cutting material grade CTCM120, which allows high cutting speeds with austenitic steels and boasts a smooth cut. It also impresses with its long tool life which in some cases was double that of the competition in benchmark tests.
The particularly tough CTCM130 carbide grade, which Ceratizit recommends for interrupted cuts, for example, is also new. If cutting speeds need to be kept low and conditions are unstable, it helps to increase process security.
The complete range for austenitic, stainless steels is characterised not just by the precise coordination of the three grades, but also by the free selection of different chip breakers. Depending on their application, customers can choose from three geometries for negative