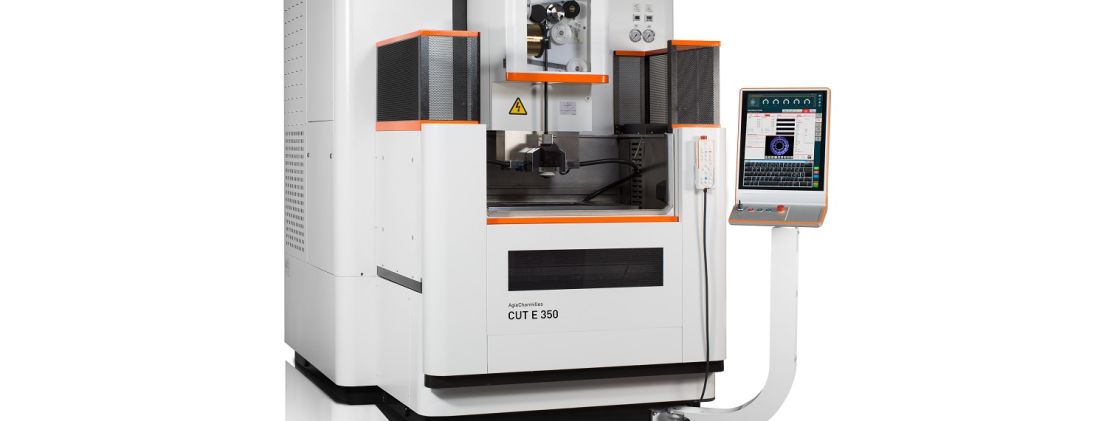
New CUT E wire-cutting machines from GF Machining Solutions boost productivity
Solutions to advance customers’ performance and productivity, secure their processes and accelerate their time to market are engineered into GF Machining Solutions’ new AgieCharmilles CUT E 350/600 wire-cutting EDM machines. The machines ensure accurate cutting of complex shapes and effective cutting on short runs.
Driving the machines’ accuracy and efficiency are onboard collision protection, new built-in machining strategies and flexible job management, within a new, easy-to-use human-machine interface (HMI). The machines’ ergonomics and improved design minimize their workshop space requirements, and their high rigidity allows the accurate cutting of large and heavy parts. Their compact, space-saving layout ensures efficient workshop integration, and the drop door system allows easy, convenient access to the working zone. The CUT E 350/600 machines boast a reliable wire circuit system for perfect unrolling that does not disrupt the EDM process during machining. The filters, positioned side by side, make maintenance fast and easy, and ease of use is also a factor in the remote control, designed for one-handed use—a real help in fine-tuning workpiece preparation.
Integrated glass scales preserve long-term, repeatable accuracy, require no recalibration, and eliminate classical screw system errors related to backlash and wear. A large, 25 kg spool is available to extend running hours and allow continuous production.
The machines’ AC CUT human-machine interface features powerful job management: Information about geometries, machining processes and command programs are processed in one file, so jobs can be transferred between CUT E series machines and all modifications are managed automatically. More than 10 automated measurement cycles are available to ease workpiece preparation, and with standard, onboard AC CAM Easy, the operator can prepare an ISO file and post-process it into a job during machining.
Intelligent Power Generator (IPG)
Efficient production is at the heart of the modern Intelligent Power Generator (IPG). Its integrated technologies boost cutting speed, precision and surface quality. The CUT E machines can use dedicated wire for decreased part costs and increased turnover, and the POWER-EXPERT module decides the optimal power to send in the wire—especially efficient for stepped parts. The corner strategy module automatically adjusts parameters during change of direction to produce sharp angles and small radii. Integrated speed-dedicated processes can reduce cutting time up to 18 percent compared to standard machines, and the CUT E series demonstrates its versatility by offering cone-cutting capability up to 30 degrees over 45 mm.
The Intelligent Collision Protection (ICP) on the X, Y and Z axes eliminates costly collision-related downtime and protects your machine and workpieces, so your machine operators can work with confidence. Unique on the market and arising from GF Machining Solutions legacy of more than 60 years of EDM expertise, ICP detects even the slightest abnormal forces and halts X, Y or Z axis movement in order o avoid collisions and the costs and damages that can follow a collision. At the same time, the machines’ ThermoCut module provides for successful, efficient threading by preparing the wire properly before threading.