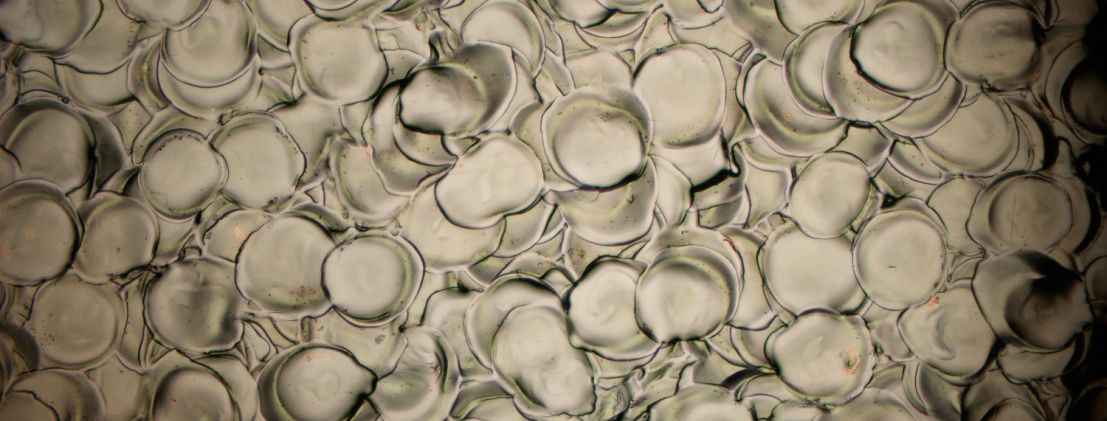
3DS technology delivers perfect surfaces while increasing productivity and end product quality
A revolutionary new technology from GF Machining Solutions takes surface texturing to a new level while increasing mold makers’ productivity, process repeatability and the quality of their customers’ end products. The three-dimensional structure (3DS) surface texturing technology ensures easy ejection of molded parts, significantly reduces mold maintenance time, and ramps up mold service life. And it does all of that while guaran-teeing perfectly homogenous surface texture, the exact degree of desired glossiness, and greater scratch resistance on end products.
Now available as an option for all AgieCharmilles FORM X000 and X00 series die-sinking machines (EDM), 3DS makes it possible — for the first time — for mold makers to go beyond roughness average (Ra) to achieve a new standard and qualify surfaces in three dimensions. Ra, the most universally recognized and widely used international parameter of roughness, describes profile amplitude parameters and focuses largely on visual or tactile examination
of the molded surface.
As smooth and uniform as the surface of cherry blossom
3DS represents the mean width between the roughness profile elements measured within the sampling length. With 3DS, the shapes of and spaces between craters left by the EDM process are perfectly controlled; which allows mold makers to modulate the surface structure and create a special texture as smooth and uniform as the surface of cherry blossom — so fine that it cannot be seen by the human eye. Made possible by the perfect spark control of GF Machining Solutions’ Intelligent Speed Power Generator (ISPG), 3DS surfaces open the door to a host of potential functionalities and benefits. The technology allows mold makers to monitor dedicated parameters and achieve different surface structures, while retaining the Ra required by customers. The FORM machines’ human-machine interface (HMI) allows the user to choose between standard and 3DS texturing.
3DS represents a solution to mold-making challenges that negatively impact productivity, reduce mold life and compromise end product quality. The technology simplifies the mold-making process by allowing mold designers to execute their visions while minimizing design compromises; reducing sticky effects to increase demolding speed, and minimizing the accumulation of residue on molds so users’ maintenance costs are reduced.
Higher flexibility and end product quality
Real-world testing under demanding workshop conditions confirms the revolutionary difference 3DS brings to die-sinking EDM. That rigorous process demonstrates that the technology provides a flexible tool for easily surpassing customers’ expectations, and refines the scale of dedicated parameters in order to achieve the desired surface texture.
Results from tests conducted by GF Machining Solutions with customers in Switzerland and Germany show that 3DS users across a wide variety of market segments — including automotive, information and communications technology, electronic components and home appliances — experience higher flexibility and end product quality, greater process repeatability and homogeneity of granularity.
At the same time, 3DS technology helps mold makers add value for their customers because it delivers greater robustness of final parts. For example, the technology imparts greater resistance to scratches and other forms of wear — an especially desirable quality when it comes to creating molds for smartphone cases and home appliances. One home appliance manufacturer used 3DS technology to enhance the robustness of covers it produced for small electrical boxes.