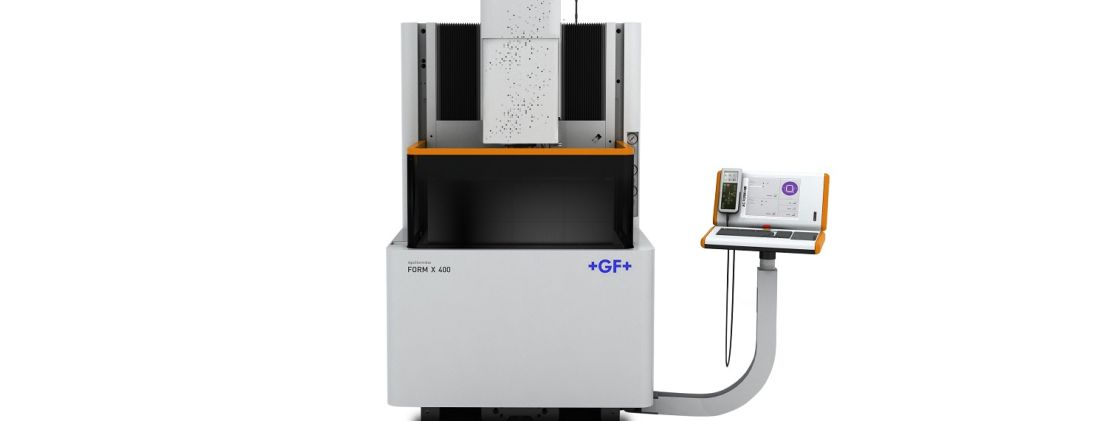
GF Machining Solutions’ new FORM X series machines yield highest precision
GF Machining Solutions’ new AgieCharmilles FORM X 400 and AgieCharmilles FORM X 600 machines form customers’ extreme success by mastering temperature fluctuations to guarantee very high precision in die-sinking electrical discharge machining (EDM). The result is superbly precise machining of complex applications where there is no room for error.
In engineering the AgieCharmilles FORM X 400 and AgieCharmilles FORM X 600 machines, GF Machining Solutions Research and Development took into account the effects of temperature fluctuation on precision and mastered those variations, which can be related to the machining environment or the machine itself. The new machines’ thermo control system guarantees unmatched precision under even less-than-ideal workshop conditions.
The sophisticated and unique thermo control system compensates for temperature variations by using a temperature-stable dielectric to cool the X, Y and Z glass scales, as well as the Z-axis ball screw. In assembly, the machine body is thermally isolated from the high-speed Z axis, which is cooled with dielectric fluid. Their moving part are fully dissociated from the loading and machining area to ensure that they are not affected by variations in temperature in the erosion area, nor by the extreme range in weights of the workpieces that can be accommodated by the AgieCharmilles FORM X series.
Moreover, the AgieCharmilles FORM X series' structure has been specially designed with a frame of polymeric material that ensures constant positioning accuracy: The machine’s extreme robustness means that all the mechanical forces are absorbed so that an accurate gap between the part and the electrode is maintained. The spheroidal cast iron X, Y, and Z axes, located in the upper part of the machine, are based on highly accurate calculations in order to reduce their mass and at the same time meet requirements in terms of rigidity, precision and dynamic conditions.
Whether the user is machining a single cavity, a multi-cavity or microcavity mold for serial production of small parts, like lens holding pieces for electronic components, the AgieCharmilles FORM X 400 and AgieCharmilles FORM X 600 represent maximum positioning accuracy. In addition to offering optimal global thermostabilization, the machines themselves are assembled with highest accuracy and under strict manufacturing conditions and aligned with a laser interferometer during the final steps of production to ensure perfect 3D positioning.
ISPG updates advance micromachining
Like all GF Machining Solutions die-sinking EDM machines, this range of solutions features the Intelligent Speed Power Generator (ISPG), the world’s most powerful generators for die-sinking EDM. The plus of this machine's generator is that it has been updated to overcome historic process challenges. With the machine's new discharge circuit for spark erosion power modulation and the flexibility to maximize material removal, the user can achieve an unprecedented level of quality and efficiency. This means, for example, that the customer's micromachining processes are optimized so fewer electrodes are consumed and a new level in sharp internal corners is achievable.
Optimal machining strategies
Moreover, the AgieCharmilles FORM X 400 and AgieCharmilles FORM X 600 feature the latest-generation and ergonomic GF Machining Solutions AC FORM human-machine interface (HMI) for an advanced level of logic, speed and safety. Developed on the basis of a study with numerous customers to streamline the mold-making process, the AC FORM HMI is organized on one menu level where all icons are arranged logically and in chronological order of use, and dynamic contextual help is always just a click away.
With integrated quality-enhancing and cost-saving intelligence, TECFORM ensures that the EDM process is continuously optimized with each pulse to significantly reduce electrode wear and make it possible to reach the finest finishes. The embedded TECFORM module allows the AgieCharmilles FORM X 400 and AgieCharmilles FORM X 600 to quickly and safely achieve the best performance and produce the desired results. Segment-dedicated technology eliminates the need for the operator to adjust the generator’s parameters.
The machines’ software manages job preparation and setup and offers a range of machining strategies to ensure highest precision and performance. Process control takes a fraction of a second and produces an extremely homogeneous surface finish. In combination, these features yield greater reliability, improved machining efficiency and significantly less unproductive time.
Increase autonomy without manual intervention
With just one machine control position, the AgieCharmilles FORM X solutions meet—in an exemplary way—the market demand for easy-to-control, automated production. Each level of Automation is easily accommodated due to the machines’ modular, space-saving design, so it’s simple to add tool changers with 20 to 140 standard electrodes.
Users of the AgieCharmilles FORM X 400 and AgieCharmilles FORM X 600 can further ramp up their autonomy by adding System 3R’s WPT1+ compact part and electrode-changing robot. Thanks to the FORM X series machines’ symmetrical design, the System 3R WPT1+ can be added to the left or to the right sides to add autonomy and increase customers’ productivity per square meter. Available in a variety of modular models to meet a broad range of user needs, this Automation solution can serve one or two machines in a production cell, and its one-, two-, or three-magazine capability provides exceptionally flexible capacity. Pneumatic control of gripping devices and table chucks is integrated into the System 3R WPT1+, which requires only minimal floor space. Together, these characteristics help manufacturers achieve greater return on their investment.
The series’ new Autoscan allows for the automatic identification of electrodes and workpieces to ensure an entirely safe, flexible automated machining process. With their clearly defined communication interfaces, the new AgieCharmilles FORM X series machines are designed for highest flexibility; they are ready to link to various media, like external handling devices or a master computer for networking several machine tools, and a measuring machine can easily be connected.