A high degree of precision to achieve extreme accuracies on machine positioning and pitch is possible with GF Machining Solutions’ hallmark AgieCharmilles CUT 1000 X, CUT 1000 X OilTech, CUT 2000 X, CUT 2000 X OilTech and CUT 3000 X machines. To support their extraordinary precision, adapted mechanical structures for high accuracy, high standard thermal stability and dedicated machine calibration and testing are mandatory.
The increased pressure on manufacturers across a variety of segments to produce more complex and accurate components in large volumes makes the choice of machine absolutely critical in terms of precision and reliability. In the context of just-in-time production flows, rejected parts can have devastating effects on timing, costs and the manufacturer’s image. As those manufacturing demands become more extreme, GF Machining Solutions’ AgieCharmilles X series takes highly accurate wire-cutting EDM to an extreme level by eliminating pitch and positioning errors.
GF Machining Solutions’ specific and uncompromising calibration testing on the machines’ production site is similar to the demands manufacturers face daily. The CUT 1000 X and CUT 1000 X OilTech deliver pitch accuracy of ±1.0 µm over 200 mm by 140 mm, and M-shape form accuracy of ±1.0 µm. The CUT 2000 X, CUT 2000 X OilTech, and CUT 3000 X deliver pitch accuracy of ±1.5 µm over 340 mm by 240 mm and form accuracy of ±1.5 µm.
Best tolerances for positioning and geometrical controls
Expert geometrical and erosion inspections ensure the results that manufacturers’ customers expect. Prior to installation, GF Machining Solutions’ experts machine a large number of holes in a plate, then use a high-precision coordinate measuring machine (CMM) to measure the position of each hole’s center. The CMM results are then reloaded into the computer numerical control (CNC) of the X series machine. That correction of the CNC guarantees perfect pitch and positioning accuracy from the very first die or mold that the customer machines.
Thanks to that expertise in testing and calibration, manufacturers can confidently produce stamping tools and multi-cavity molds for electronics, information and communications technology, as well as the tiniest components for MedTech and watchmaking. Optimal machining conditions for extremely demanding micro applications are ensured by the X series machines’ high precision axes, short measurement loops, dual measurement system on all axes, consistent separation of the EDM area from heat sources, and the submerged working area.
Quality and accuracy are guaranteed during assembly of an X series machine, due to GF Machining Solutions’ thorough measurement and high process control standards for all assembled mechanical components.
Highest productivity
In addition, the X series machines offer manufacturers a wide range of productivity- and quality-enhancing features:
- Exclusive Automatic Wire Changer (AWC) two-wire spool allows the use of larger diameter wire or premium wires for the main cut and then automatically switch to smaller wire for the finishing cut resulting in huge increases in cutting speeds. Productivity is boosted by fast and reliable wire threading and simple and dependable wire disposal with the integrated wire chopper.
- Highest flexibility to insert urgent machining jobs, thanks to the onboard Job Management System.
- Perfect wire threading, even under the most difficult conditions, with the THREADING-EXPERT, a retractable device driving the wire from the upper guide to the start hole.
- Absolute quality results, thanks to the Integrated Vision Unit (IVU Advance). With an embedded charge-coupled device (CCD) camera linked to a backlight installed on the lower arm of the machine, IVU Advance allows pre-setting, in-process local measurements, and scanning of the contour machined.
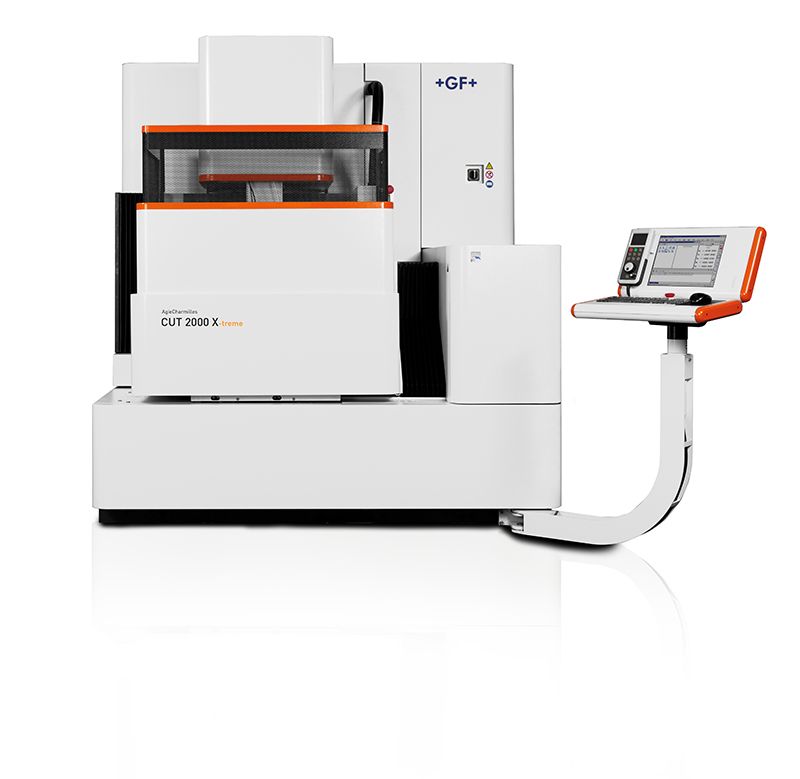