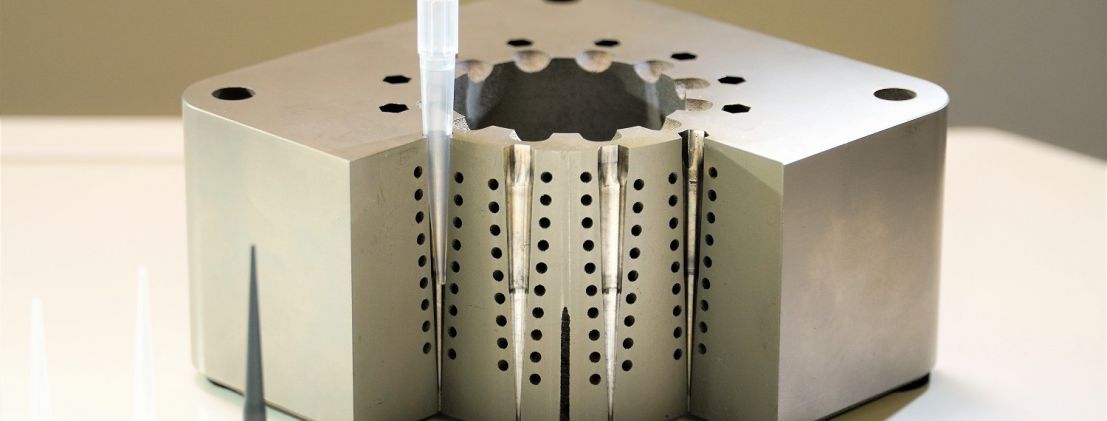
GF Machining Solutions is focusing on medical technology
GF Machining Solutions has opened a new Medical Solutions Center at its German headquarters in Schorndorf. With this step, the machine builder is focusing on medical technology. The Medical Solutions Center houses all the machines (laser machines, 3D metal printers, machining centres and wire and sinker EDMs) required for the production of medical devices, as well as the appropriate software and a team of specialists. The Medical Solutions Center gives both customers and experts within GF Machining Solutions the opportunity to optimize production processes and to develop and test new applications.
The Medical Solutions Center's opening reflects GF Machining Solutions's strategic focus on the medical industry. With a 1,200 m2 demo room, packed with machine tools, software, digitization solutions and technical know-how, GF Machining Solutions has the key technologies needed to produce medical devices and implants. During the corona pandemic, sales from the medical industry increased by 20%. At the same time, sales in other sectors fell by 20%. Although GF Machining Solutions is optimistic about the future - for example, the machine builder expects the aviation industry to be back to its old strength by 2023 - the company sees a large growth market in the medical industry. This is where the company will focus most of its attention over the next five years.
Blueprint for the future
Not only has GF Machining Solutions invested in a demo room, but also in a complete team of medical experts who, together with the customer, can come up with solutions to challenging issues. In addition, cooperation has started with KSF from Tuttlingen (D) to develop new production technologies for the medical industry. According to Ivan Filisetti, President of GF Machining Solutions, the Medical Solutions Center in Schorndorf is just the beginning: "With this center, we are laying the foundation for our medical technology. The goal is to develop as much knowledge and medical production technology as possible in a short period of time, which can then be shared from Schorndorf with all our other locations worldwide."
All technologies available
Everything comes together in the medical industry: high surface quality, small dimensional tolerances, materials that are difficult to machine, reproducibility, traceability and productivity. The production of medical devices is therefore often costly and qualitatively challenging. Typically, multiple machining technologies are required to produce a part, such as machining, edm, surface finishing and engraving. This requires many intermediate manual operations that increase the risk of errors. GF Machining Solutions' comprehensive technology portfolio of machine tools, automation and software solutions reduces the amount of human intervention and is perfectly aligned with the requirements of the medical industry.
Five-axis milling
The Mikron Mill S 600 U is a five-axis machining center ideally suited to machining workpieces with complex contours. Its stable and highly dynamic design combined with high thermal stability, linear drives and a powerful Step-Tec spindle, allows for efficient and precise machining of injection moulds, implants, surgical instruments and dental parts made from tough, hard materials. Using pallet automation, as presented in the Medical Solutions Center, lead times are reduced.
Productive wire cutting
Wire cutting is a widely used production technique for medical applications. Wire cutting is an ideal technique, particularly for parts that must comply with high dimensional and surface accuracy. In the medical center, GF Machining Solutions has set up a Cut P 550 wire EDM, among other things. "Wire EDM is always regarded as a slow production technique. By producing several products simultaneously, the output can be increased," says Sendler. He cites the production of medical pliers as an example. With just two cuts, the team managed to produce sixteen parts. By turning the material a quarter after the first machining step and then performing the second cut, the pliers came out of the EDM almost ready to use. This way, wire EDM can be used very productively. "Thanks to the Medical Center, we can develop these kinds of smart solutions together with customers in the future. That gives a lot of added value." GF Machining Solutions has further developed the wire EDM process over the years with all kinds of new and smart features. Intelligent Spark Protection (ISPS) System is one such feature that improves process reliability and productivity. ISPS determines in real time where the spark discharge is taking place. This is especially useful in case of interrupted cuts. Since the spark prefers to travel where the electrical resistance is lowest, such as at gaps in the workpiece, wire breakage can occur. ISPS monitors this and can automatically adjust parameters so that the spark always occurs at the right point. This ensures higher productivity and process reliability.
Laser texturing of functional surfaces
A technology that is increasingly used in the production of medical components is laser texturing. With the help of a laser, it is possible to apply textures, engravings and markings very precisely. With the Laser P 400 U, GF Machining Solutions has integrated the laser into a five-axis machine, allowing not only 2D, but also complex 3D surfaces to be machined. For example, the technique can be used to apply texture to prostheses for better adhesion to human bone or to provide surgical instruments with a micro- and sub-micro texture to obtain functional properties. The latter can include hydrophobic surfaces that do not stick to blood, so that the surgeon has a better view of the operation. Laser texturing can also be used to create antibacterial, easy-to-clean or anti-reflex surfaces. If, for example, there is no reflection, the surgeon can view the image better during endoscopy. So there are all kinds of applications where laser processing is useful.
The Laser P 400 U is part of the Medical Solutions Centre. Remarkably, the machine is equipped with an all-in-one laser head that houses both a nanosecond laser and a femtosecond laser. The laser head makes it possible to switch from one source to the other automatically and within one second. In this way, production time can be reduced by combining two laser operations on the same machine.
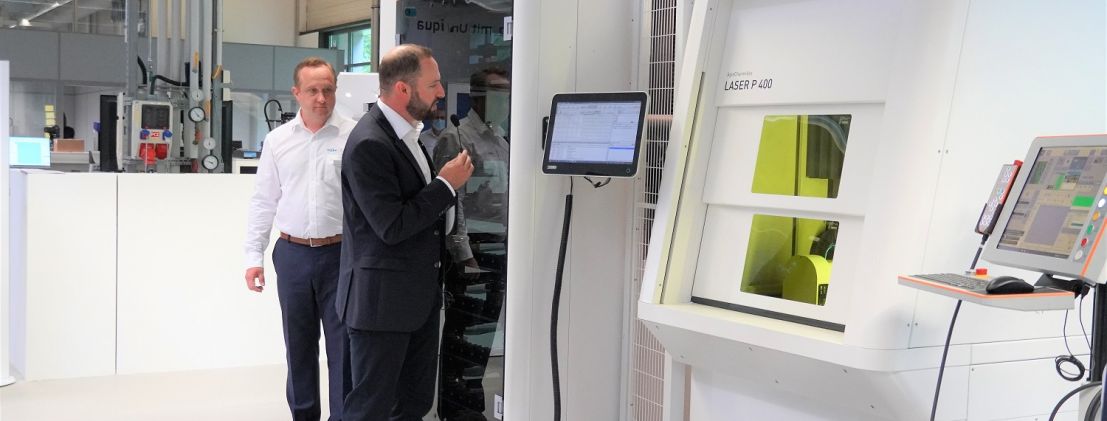
Automation and traceability
As in every sector, cost prices and delivery times are under pressure. Add to that the shortage of technical staff and, as a manufacturing company, you can no longer avoid automation. GF Machining Solutions has a broad in-house automation portfolio, with which all processing steps can be linked. In addition to machine tools optimized for automation with pallet and zero-pressure systems, the machine builder also offers robot cells, WorkshopManager Software and the integration of measurement and control technology. The entire package enables unmanned production from single pieces to bigger series production
The medical industry not only places high demands on the quality of components, but also on traceability. In order to comply with medical regulations, production data must be recorded for each component. GF Machining Solutions can demonstrate how data management works live in the Medical Solutions Center. Every machine in the center is connected to GF Machining Solutions' WorkshopManager software. With this, the manufacturer demonstrates the benefits of automated data management. "Compliance with documentation and data tracking regulations is a fundamental part of the production of medical components. GF Machining Solutions has an extensive portfolio of hardware and software solutions to make this happen. The rConnect Platform, which enables wireless access to all machine tools, combined with real-time process monitoring and data logging, provides a complete overview of the production process," said Sendler during the tour of the medical center.
Additive Manufacturing
A production technology that lends itself extremely well to the medical industry is Additive Manufacturing (AM). Implants and prosthetics are often unique single pieces that can be produced economically by AM. In addition, AM offers the possibility to produce special geometries, such as sponge-like structures for better adhesion to the human body. Together with 3D Systems, GF Machining Solutions develops applications for 3D printing. This cooperation goes so far that the powder bed machines are built at the machine builder's site in Losone (CH). A zero-point clamping system is used for 3D printing. This means that printed products retain their position after printing for efficient post-processing. It is also possible to automate the 3D-metal printer thanks to the zero-point clamping system. The cooperation between GF Machining Solutions and 3D Systems has also led to the development of the CUT AM 500. This metal printer is set up in the new medical center and combines 3D printing with wire EDM. After printing, the CUT AM 500 can rotate the base plate by 180 degrees and then use the wire to cut the products loose from the base plate. Sendler: "Our AM solutions are designed for high productivity and user-friendliness. This makes them extremely well suited for the medical industry."