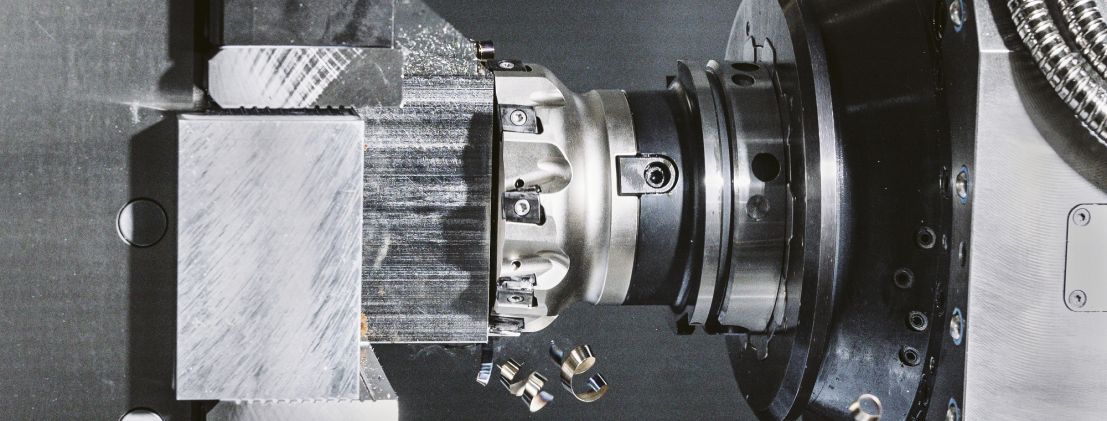
Maximill - Tangent From Ceratizit Picks Up The Pace With Turbo Feed Rates
When machinists face the challenge of monitoring processes amidst a maze of interfering contours, the usual solutions often fall short. Face milling cutters can't be used, and long overhang lengths make stable, low-vibration machining seem unattainable. While this scenario might seem daunting, the solution lies in utilizing the right tool. Introducing the MaxiMill - Tangent from CERATIZIT, a groundbreaking tangential indexable insert milling cutter. With its exceptional durability, this tool transforms the impossible into reality, particularly when machining steel and cast iron components.
The MaxiMill - Tangent simultaneously enables stable and soft-cutting machining. Developers at CERATIZIT have long prioritized a uniform chamfer profile across the entire cutting edge length of the precision-ground indexable inserts. With a wide range of carriers and inserts with four usable cutting edges in sizes -09 and -13, the tool manufacturer offers a versatile selection for different applications.
Ground inserts with stable cutting edges
The MaxiMill - Tangent has indexable inserts optimized for machining ISO P and ISO K materials. Moreover, it features a maximum infeed depth of 8 mm for the -09 insert, while the larger model goes even further to 12 mm. MaxiMill – Tangent also has universal -M50 and -F50 chip grooves are available, while delivering increased cutting-edge stability thanks to a smaller radial clearance angle. Furthermore, there is an integrated face-cutting edge, which offers numerous advantages, including uniform material removal that results in a smoother component surface. In addition, the cutting forces are distributed more evenly, which reduces the load on both the tool and the machine.
The MaxiMill - Tangent is available on the market in three carrier variants, a shell-type milling cutter, screw-in milling cutter and with a straight shank, and range from 25mm to 125mm. The large and stable contact surfaces in the integrated carrier inserts carrier provide additional stability and reliability. But the advantages of tangential clamping don’t stop there. Compared to radial systems, tangential clamping provides extra space for significantly more indexable inserts on the milling cutter body, thus guaranteeing maximum cutting-edge density and efficiency. And to prevent any drop-offs in efficiency during tool changes, inserts can be rotated, turned and replaced quickly and easily. “Thanks to the MaxiMill – Tangent’s exceptionally stable design, its high-performance four-edged indexable inserts and tangential clamping, even components with interfering contours can now be machined easily and cost-efficiently —including a built-in feed turbo,” says Product Manager Robert Frei from CERATIZIT.
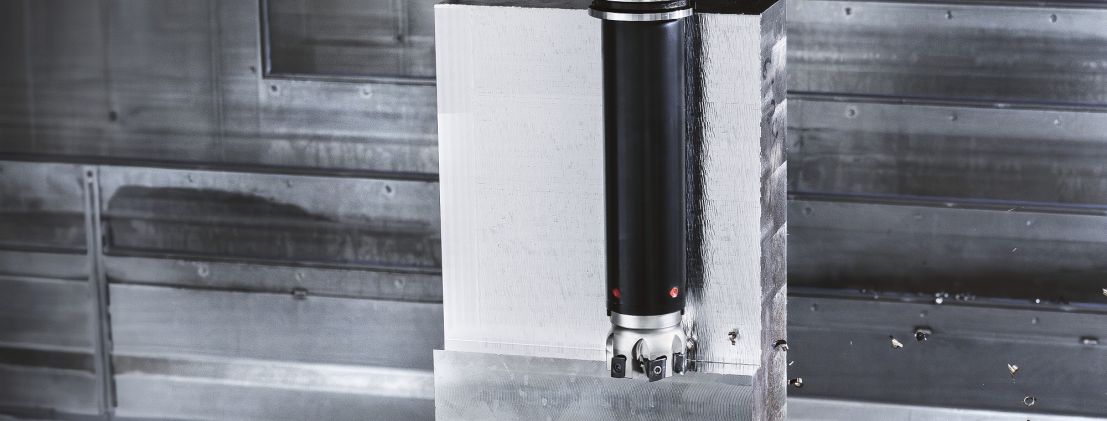
Tangential to the feed turbo
So, how does the MaxiMill - Tangent compare to a conventional corner and face milling system? When preforming GGG-50 machining, it shows off just what it can do. With a 63mm beam diameter, six cutting edges in simultaneous use, a 2 mm infeed depth and an insert width of 35mm, it showed the competition that it was a cut above — or 15. While the competition managed to complete 12 components, the MaxiMill - Tangent produced a whopping 27.
Internal cooling channels prevent chip jamming
One key to the MaxiMill – Tangent’s success lies in its optimum chip control on shoulder, corner and face milling —something attributed its design and cooling channels. This prevents devastating chip jams, improves the surface quality of the component and significantly extends the service life of the tools.