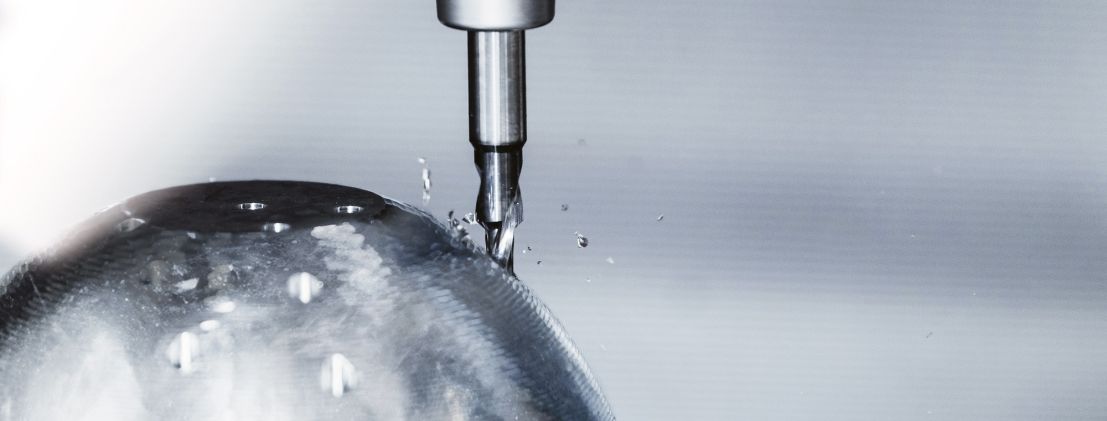
CERATIZIT WTX Micropilot Drills Even on Inclined or Curved Surfaces
In the past, you could only drill on inclined or curved surfaces with pre-chamfering using a milling cutter. Thankfully those days are in the past, and now only one tool is required: the newly developed WTX - Micropilot from CERATIZIT. It can even pull off 90° countersinks at the bore entry in a single operation —saving tool changes, time and costs.
Micromachining has rules and practices all its own. Simply put, what works well with standard tool dimensions does not necessarily hold true with small diameters. “To this end, we have revised our micro-drilling program and developed a genuine time saver. The WTX - Micropilot is small in stature, but big in performance. Perfectly matched to our WTX - Micro micro drill from 8xD - 30xD, the pilot drill is used at drilling depths of up to 2.5xD,” says Manuel Keller, Product Manager at CERATIZIT.
Say goodbye to crooked drill holes
When faults occur in complex, micro-sized components, they quickly end up dumped in the recycling can. Truth, be told, there are a number of things that can go wrong: drills run off, drill holes get crooked or tools break—including damage to the workpiece itself. “Efficient machining of small components presents its own set of challenges,” says Manuel Keller. “Our customers want process reliability, the shortest possible machining times and demand extremely high-quality standards. Fortunately, our WTX - Micro series is up to the task.” Thanks to its ingenious face geometry with a 160°-point angle, the tool ensures the follow-up drill can plunge in cleanly and without running. And with the special Dragonskin coating, clean chip removal and longer tool life are guaranteed.
The WTX - Micropilot is state-of-the-art through and through—from the substrate to the geometry to the coating. It is also perfectly designed to work together with its “best buddy” WTX–Micro. This drill duo can handle the most common as well as the most demanding tasks. “One special feature of the WTX – WTX-Micropilot is that it circumvents the usual mirroring required if drilling inclined and curved surfaces with an inclination of up to 50. This eliminates one processing step, saving time and tool changes. When piloting on straight surfaces, a 90° countersink at the bore entry is also possible,” reveals Manuel Keller.
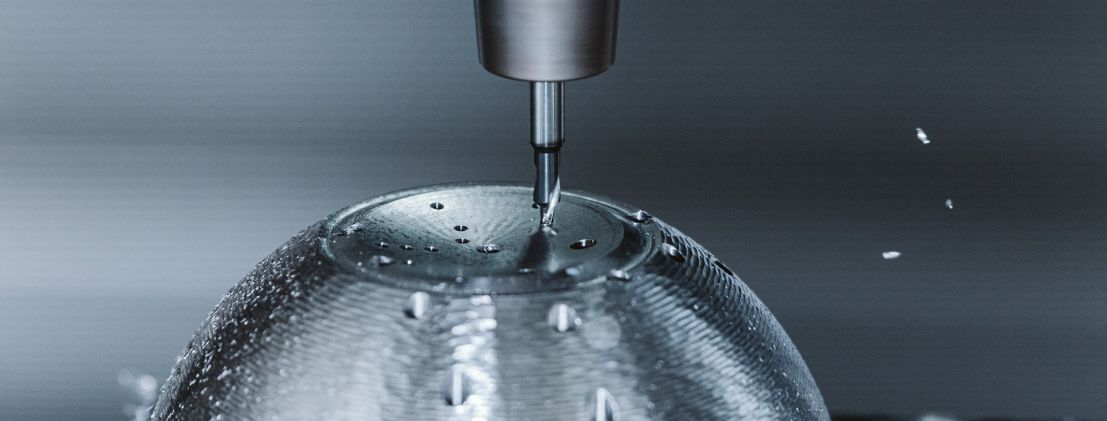
Smooth moves for maximum chip removal
What all WTX micro drills have in common is their special pointing, which maximizes positioning accuracy and excellent centering properties. Their lapped surfaces and the patented chip space grinding also guarantee safe and fast chip removal. Additionally, the spiral internal cooling channels of the WTX Micro drill have been optimized to ensure maximum flow of cooling lubricant, which, in turn, secures improved surface quality of the holes. Among other things, this is thanks to a power chamber, which is fitted to the micro drills from 5xD over the entire shank length, which increases the amount of coolant at the tip while maintaining uniform pressure—thus improving tool life.
Made for maximum precision
With its micro-tool portfolio, CERATIZIT covers the majority of micro-machining applications with high-quality solutions. “This also applies to the WTX - Micro product range, including the new WTX - Micropilot, which makes the impossible possible. On both inclined or curved surfaces with an inclination of up to 50°, there is no need for prior mirroring. And if 90° countersinks are required at the bore entry point on straight surfaces, WTX - Micropilot can easily handle the task in a single operation, saving tool changes, time and costs—without sacrificing quality,” says Manuel Keller.
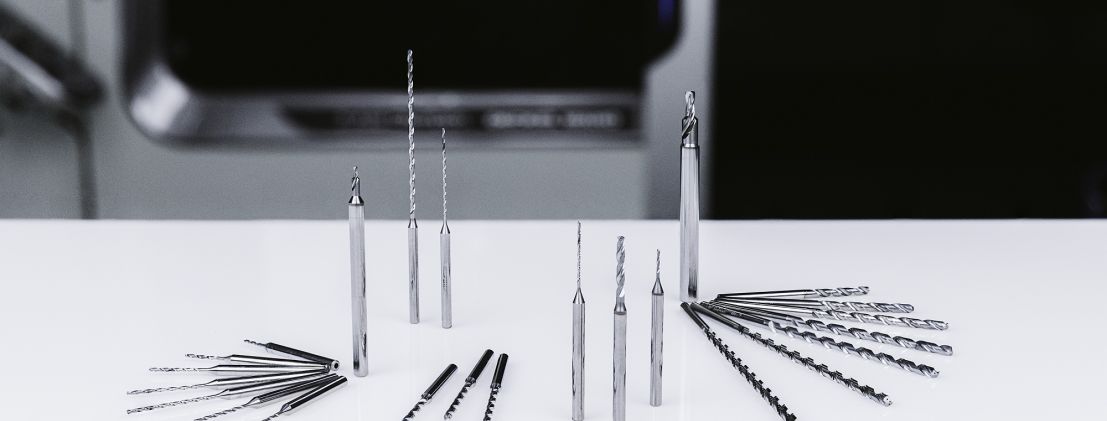