The medical industry has been flourishing for years, and the future outlook continues to be remarkably positive. The industry is characterized by small production batches, along with stringent requirements for precision, surface quality, and cleanliness of medical components. GF Machining Solutions is primed to meet these demands with its specialized machinery and expertise.
For the past four decades, the medical manufacturing sector has seen significant growth. According to Statista, a global data and business intelligence platform, the medical device market's expected revenue in 2023 is nearly $500 billion. This revenue is anticipated to grow at an annual rate of 5.26%, resulting in a market volume of over $600 billion by 2028. With the global population increasing, people living longer, more regions having access to quality healthcare, and rapid advancements in medical technology to keep people vital in their later years, it's only logical that the medical industry has been on an upward trajectory. GF Machining Solutions is well-equipped to benefit from this growth by introducing modern machines capable of high-precision machining of complex contours. The company also offers automation and process optimization solutions.
Optimizing Processes Together
To support customers on their journey to efficient production of medical components, GF Machining Solutions (GFMS) has honed its expertise in this area. Beyond machining centers, wire and die-sinking EDM machines, microlaser machines, and automation solutions specializing in medical component machining, GFMS also engages in collaborative projects with clients.
For a medical sector client, GFMS, along with Blaser Swisslube, Rego-fix, and Fraisa, optimized the production of a so-called guide rail from stainless steel 1.4542, enabling reliable production in an unmanned setting. The client faced issues with long chips leading to tool breakage, causing an unstable process with significant downtime. "Due to a shortage of skilled workers and the need to increase capacity from existing machinery, manufacturing companies are increasingly turning to automation. However, many don't realize the extensive groundwork required to achieve reliable unmanned production. My advice is to first achieve a stable process and then look towards automation. Along with our partners, we support clients in achieving a stable process," says Thomas Wengi, Managing Director at GF Machining Solutions. By redefining the clamping, tooling, machining strategies, and type of coolant used, the partners were able to establish a stable and automated machining process, resulting in a 25% higher material removal rate and a 40% reduction in production time.
An Innovative Approach to Knee Implant Production Without Grinding
GFMS also showcased an optimized production process of a medical component, in partnership with others. The client sought to reduce the production costs of a knee implant by 25% due to the annual 2% decrease in market price for an artificial knee, putting production under pressure. Along with OPEN MIND and Seco Tools, GFMS found a solution to optimize the production process, particularly focusing on the machining of the 'femoral' component, one of the three critical components of an artificial knee.
The 'femoral' component is the most complex part to produce due to its curved surfaces and the challenge of merging all tool paths fluidly. In cooperation with OPEN MIND and Seco Tools, GFMS made the grinding process redundant. By opting to machine the curved surfaces with barrel and ball end mills for perfect transitions, this method proved to be 15% faster than the tools previously used by the client. Additionally, hyperMill Best Fit was employed to calculate the best tool paths for perfect smooth transitions. Combined with the five-axis Mikron MILL X400 U G, equipped with linear motors and a stable frame made from vibration-damping polymer concrete, a surface quality was achieved straight from milling that eliminated the need for any grinding process. Ultimately, the partners managed to reduce machining costs by nearly 50%.
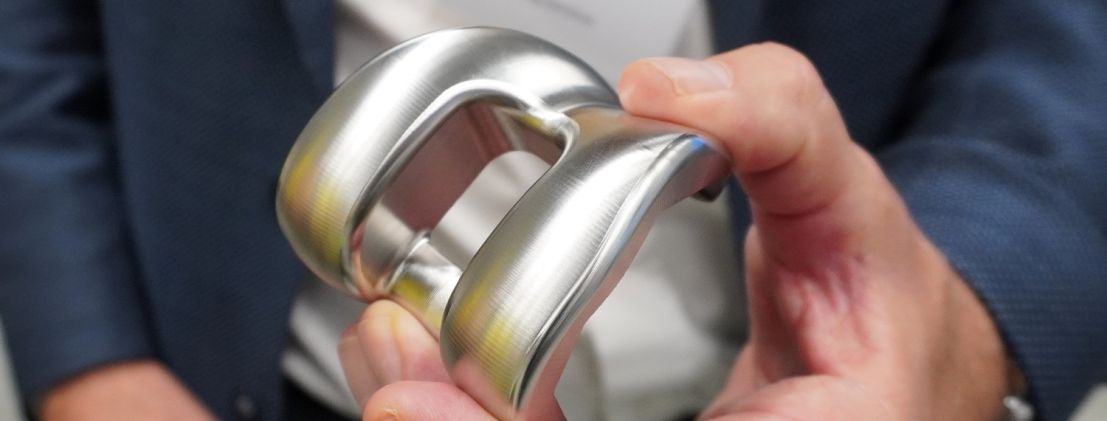
Supercritical CO2 Cooling
A notable topic discussed during the Solutions Days was supercritical CO2 cooling. The use of supercritical CO2 as a coolant during milling has garnered significant interest in recent years for its efficiency gains, especially in medical equipment manufacturing. GFMS has conducted extensive trials with this innovative cooling technology and concluded that productivity, tool life, and workpiece quality are substantially better with CO2 cooling.
A milling test with titanium showed that CO2 cooling results in significantly less wear on the tool's cutting edge compared to traditional coolant. The researchers managed to machine 233% more volume per tool with CO2 than with coolant. Interestingly, the chips were much smaller due to the low temperatures making them brittle and thus more prone to breaking. The test also revealed a 16% improvement in surface roughness and an 85% increase in cutting speed. "With CO2 cooling, we could mill 900 meters in the same time it took to mill 500 meters with coolant emulsion," said one of the researchers. GFMS has also conducted similar tests with other materials commonly used in the medical sector, including stainless steel and UHMWPE, showing comparable improvements.
The system for supercritical CO2 cooling can be integrated with Mikron MILL machines. It can deliver CO2 at pressures up to 110 bar and is equipped with an MQL (minimum quantity lubrication) delivery system. This represents a significant advantage of CO2 cooling over cryogenic cooling. Tiny oil droplets can be perfectly and homogeneously mixed with the CO2 cooling and directed through the spindle to the cutting edges of the tool. By using medical-grade cutting oil that evaporates at room temperature without leaving residues on the machined surface, CO2 cooling is exceptionally suited for producing medical components, such as orthopedic implants and casings for implanted devices like pacemakers.
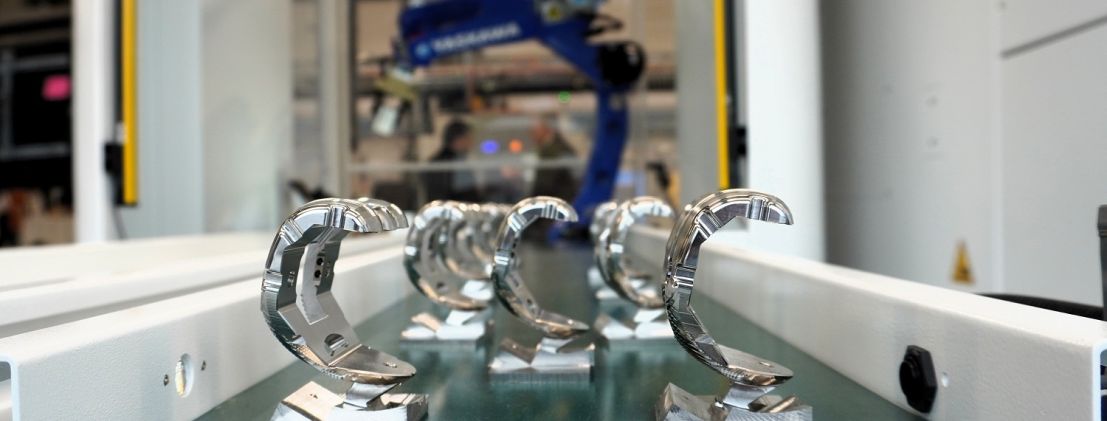