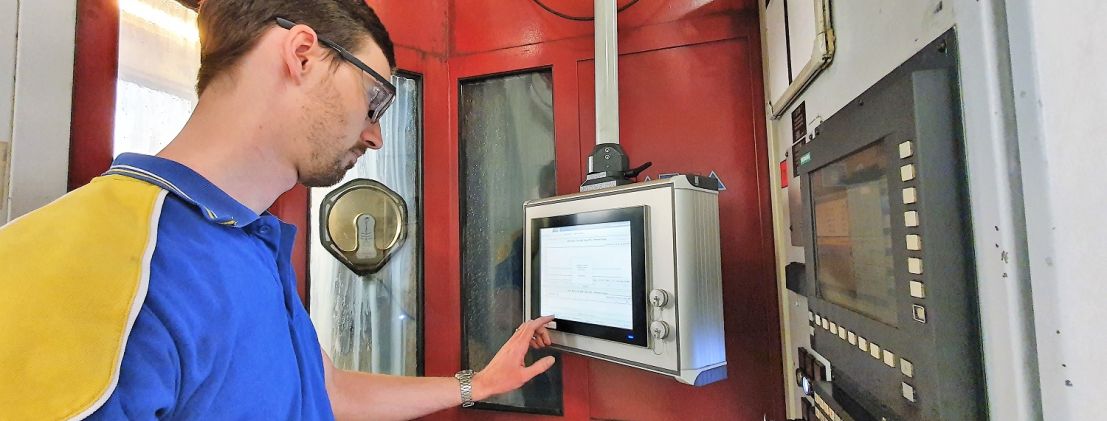
CNH Industrial Belgium optimizes twenty-year-old machine with ToolScope
CNH Industrial in Antwerp, manufacturer of tractor components (mainly rear axles and drive systems), has modernized a twenty-year-old machine tool using ToolScope. Thanks to this monitoring and control system from CERATIZIT, CNH Industrial gains a better understanding of the machining process and can use machine data to reduce cycle times, increase tool life and achieve a reliable production process.
The manufacturer of parts for New Holland, Case IH and Steyr tractors was looking for a solution to achieve more efficiency with the existing machine park to meet the growing demand. According to Baptiste Muller, process engineer at CNH Industrial Belgium, the age of the machinery was the biggest challenge in the optimization process. "To reduce cycle times, you can broadly do two things. Either invest in new machines or optimize existing processes. We chose the last option, because despite the fact that some machines are twenty years old, they are still of very good quality. But optimizing these machines with outdated controls and limited computing capacity is not so easy, and certainly not with a limited budget," says Muller.
After a search, Muller finally settled on ToolScope from Ceratizit: "Our factory in India has already been using ToolScope for some time and has achieved promising results in reducing tool breakage and increasing tool life. Of course, we also looked at other solutions, but they were all incompatible with our older machines. To test ToolScope in our factory, we started by optimizing one machine."
Industry 4.0 easily installed
The ToolScope monitoring and assistance system continuously records machine signals generated during the production process. This data is visualized and used to monitor and regulate machine control. The status of the tool and machine is visualized based on a patented process for statistical process control. "With ToolScope, it is possible to integrate Industry 4.0 into an existing machine shop. As we show at CNH Industrial, this even works with a 20-year-old PLC," says Stefaan Grimonprez, technical consultant at Ceratizit.
Although ToolScope 'runs' on external hardware, the system does communicate with the machine control 100 times per second. The question was whether the two-decade-old controller could cope with this communication. "The computing power of the machine software is already 80% loaded in normal operation, so to avoid overloading it is necessary to capture and process the process data externally. That's the advantage of ToolScope: it works independently of the machine controller, so the system can work very well together with older machines." An additional advantage of the external hardware is the new interface, which enables CNH Industrial to export data more easily.
Process optimization with insightful data
ToolScope is made up of a multitude of apps with unique capabilities. This allows users to set up ToolScope completely according to their own wishes, and possibly expand it with new functionalities over time. CNH uses three apps, namely Process Monitoring, Wear Monitoring for Tools and Adaptive Feed Control.
With Process Monitoring, CNH Industrial gains full insight into the production process. "We produce gearboxes and housings on this machine 24/7. With ToolScope we can visualize all process data in a graph, after which we can see very precisely where the process deviates from an optimal process. For example, if there is a peak in the spindle's torque at a certain point, then you know you can optimize the program at that point. In this way we are able to optimize the process continuously," says Muller. CNH is machining castings from 300 kg to 450 kg on the ToolScope-equipped machine, of which about 10% is chipped. So with small improvements, the company can achieve big results over time.
In addition to insight into the process data, Process Monitoring also responds automatically to any deviations in machining. For example, the system identifies tool breakage, missing workpieces or tools and other faulty processes and stops the machine immediately in such a case. This creates reliable unmanned production that avoids the risk of damage to tools, workpieces and machines.
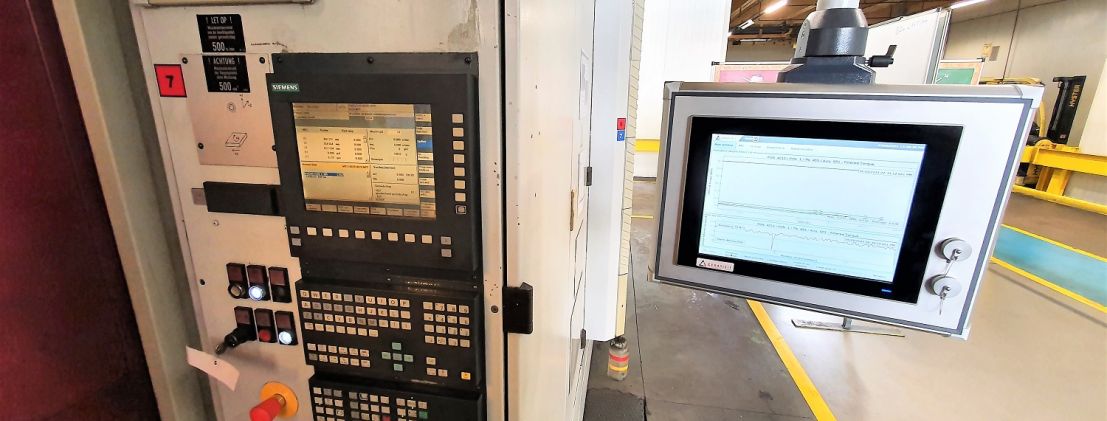
Making the most of tool life
With Wear Monitoring for Tools, CNH Industrial has found a solution to get the most out of its tools. The function determines when a tool reaches the end of its life based on the process force to which the tool is exposed, rather than using fixed tool life times. A fixed tool life does not take into account variations in machining conditions, such as fluctuating material quality or potted sand that castings are known for. This means that the available tool life can be much better utilized. The result is lower tooling costs and an increase in machine availability.
Automatic feeding
For Muller, the app Adaptive Feed Control is the most interesting feature. "We machine castings and they have many variations. For example, castings are much harder in winter than in summer, which reduces the tool life of some tools by 25% with the same process parameters. In addition, castings are not dimensionally stable, which means that more material needs to be machined in some cases than in others. With Adaptive Feed Control, we can achieve shorter cycle times despite these challenges." Adaptive Feed Control measures the process forces and automatically adjusts the feed accordingly. This leads to a faster and more stable production process while protecting the tool from critical process forces.
3% cycle time reduction
CNH Industrial has been using ToolScope for six months now and has achieved a cycle time reduction of 3%. The goal is to get to 4%. Muller: "ToolScope is a fantastic tool for a process engineer. It is a complex system with a lot of possibilities. Of course the system works the moment you install it and it is easy for an operator to use. But if you want to get the most out of it, you have to fine-tune a lot of parameters and that is a time-consuming and continuous process. Companies considering digitalization must be prepared to spend time analyzing data and playing with parameters. Digitizing and optimizing is more than just plugging in a system. It's an ongoing learning process.
Muller used ToolScope to optimize the machining process of the twenty most important and frequently used tools. For some milling tools, this has reduced machining time by 10% to 15%. For drilling, machining time has been reduced by 8%. A considerable improvement. The fact that the total cycle time reduction currently stands at 3% is due to the fact that as many as 100 to 130 tools are used for machining large gearboxes and housings. In addition, CNH is going for "safe," because production must not come to a halt. "It's a challenging task to get those last few percent out, but at the end of the day it's worth it. And what's really handy is that you can copy the parameters you collect with the first tryout to other machines. Then the ROI suddenly becomes very interesting," says Muller. Because of the good first results, CNH Industrial Belgium expects to equip more machines with ToolScope in the future.