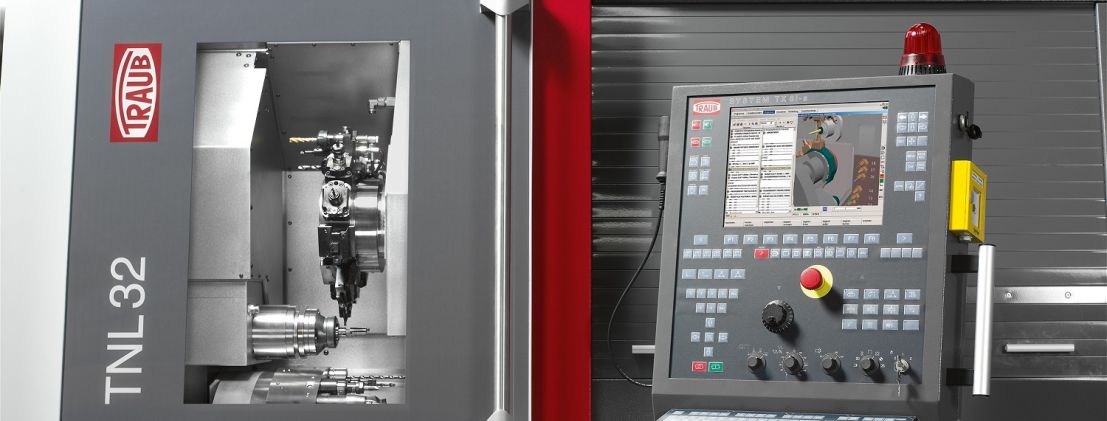
TRAUB TNL32-11 sliding/fixed headstock automatic lathe cuts machining time
The TRAUB TNL32-11 is the latest addition to the successful TRAUB TNL32 sliding/fixed headstock automatic lathe series. Its signature feature is a front working attachment mounted on a cross-slide which raises the number of linear axes on the machine to eleven. This means that the powerful TRAUB TNL32-11 can perform simultaneous machining with three fully independent tools. This saves machining time – especially for components with a high proportion of drilling.
The TRAUB TNL32 series has rapidly become a success on the market. Three different models – the TNL32-7B, the TNL32-9 and the TNL32-9P cover diverse market needs. All of them have explanatory product names: the 32 refers to the bar capacity, the numbers 7 and 9 indicate the number of linear axes, the B stands for an additional B-axis and the P for a machine with the TX8i-p control. So it is obvious that the fourth member of this lathe family, the TNL32-11, has two additional linear axes (see the overview in the box).
Like the TNL32-9, the TNL32-11 has a headstock moving in the Z-axis, an upper and identical lower turret with X, Y, and Z-axes, and a counter spindle movable in the X and Z directions. A new feature is the front working attachment, which sits on an additional cross-slide moving in the X and Z-axes. It provides the user with further, freely positionable tools and enables the use of up to three tools, simultaneously and independently of each other.
High flexibility due to interpolating Y-axis
In addition to the two linear X and Z axes, the front working attachment features a CNC circular axis. By the interpolation of the rotary axis with the X-axis and the C-axis of the main spindle, the front working attachment can also be used in the Y direction using an interpolated Y-axis. The particular benefit: when a drilling tool needs to be corrected to exact center, the necessary corrections can be simply performed via the CNC controller. That can be help with small parts which react with great sensitivity to even minimal offset errors.
The large clearance circle of the tool mountings of the front working attachment was chosen deliberately: its generous size allows simultaneous and collision-free machining together with the two tool turrets on the main spindle.
Eight additional tools
The front working attachment makes eight additional tool stations available. Four of them are used to mount fixed tools, the other four are for live tools. There is also a station for a workpiece gripper which can unload a machined workpiece from the counter spindle. A time-saving advantage: while the finished workpiece is discharged from the counter spindle, the next part can already be machined with two tools at the main spindle.
With an output of up to 3.4 kW and a maximum speed of 12,000 revolutions, the tool drive in the front working attachment is extremely productive and designed for high power. The tool holders are highly robust and stiff with a mounting shank diameter of 36 mm. Individually controllable coolant pressure of up to 80 bar is available at every station. One live station can be used as a deep-hole drilling station with a coolant supply up to 120 bar. The front working attachment can also be used as a tailstock when producing long components.
Large, user-friendly work area
Alongside the advantages of the front working attachment, the TRAUB TNL32-11 sliding/fixed headstock automatic lathe offers the many other benefits of the entire series. The work area is easily accessible to the operator due to its high and wide sliding door, simplifying setup and changeovers. A large inspection window allows the operator to keep a close eye on the machining process. The long Z travel of the headstock means the machine can easily be used for sliding or fixed headstock turning without compromises. The conversion effort is less than 15 minutes.
Two drives in one turret
The tool turret technology is particularly impressive. Indexing is performed using an NC rotary axis that controls movement via an internally meshing planetary gear. This allows the turret to be indexed to any preferred position without a mechanical locking mechanism being necessary. The free positioning of the turret makes multiple-tool assignment possible on each station.
Another highlight is the “Dual Drive”, consisting of two drive trains integrated within one turret. This patented drive solution reduces non-machining time and thus also machining times per piece. An idea with is both simple and ingenious: while one tool is in use, the tool intended for the next work step can be accelerated up to the desired speed during main time and is immediately available at full speed after the turret indexing operation. Jerky accelerations and delays that were previously unavoidable when reducing auxiliary processing times are now a thing of the past. In addition, the user benefits specifically from the fact that tool holder wear is reduced due to the lower acceleration values. Even with live tools, chip-to-chip times are around just 0.3 seconds.
Improved tool mountings
The TRAUB compact shank system is used in the turrets, enabling extremely precise mounting of tool holders. They are seated deeper in the turret than in other commercial systems, which results in less leverage effect and thus greater stiffness. For live tool holders, the large 45 mm shank diameter allows for the installation of spindle bearings with large diameters. A quick-change system enables high-precision, smooth exchange of tools without removing the tool holder. The compact shank system verifiably increases the tool life and also contributes to improved surface quality.
The right TNL32 for every application
The TRAUB TNL32 series now consists of four models. The TNL32-9P is the base version of these machines. It has nine linear axes. The two tool carriers have large travel ranges in the X/Y/Z-axes. The counter spindle is mounted on a separate cross-slide with X- and Y-axes. Rear-end machining is carried out by one of the two X/Y/Z turrets. The two tool carriers can perform cutting operations on both the main spindle and counter spindle. This extends the scope of machining to cover workpieces over 250 mm long. With simultaneous internal machining, the additional X-axis of the counter spindle ensures excellent clearance.
The TNL32-9 is based on the same mechanical design as the TNL32-9P, but is equipped with the TRAUB TX8i-s control.
The latest variant of the TRAUB sliding/fixed headstock automatic lathe series TNL32 is the TNL32-11 presented in this article. In addition to the axes of the TNL32-9, it features a front working attachment mounted on a cross-slide which increases the number of linear axes to eleven. This means that it can perform simultaneous machining with three fully independent tools.
The TNL32-7B has seven linear axes. Here also, the two tool carriers feature large travel ranges in the X/Y/Z-axes. Again, the lower tool carrier is integrated in the counter spindle. The upper tool carrier is equipped with an additional B-axis swiveling 100°. It can be used to machine geometrically complex parts and demanding contour elements which require additional operations such as milling, drilling, cross-drilling or transversal threading with any number of angular positions.