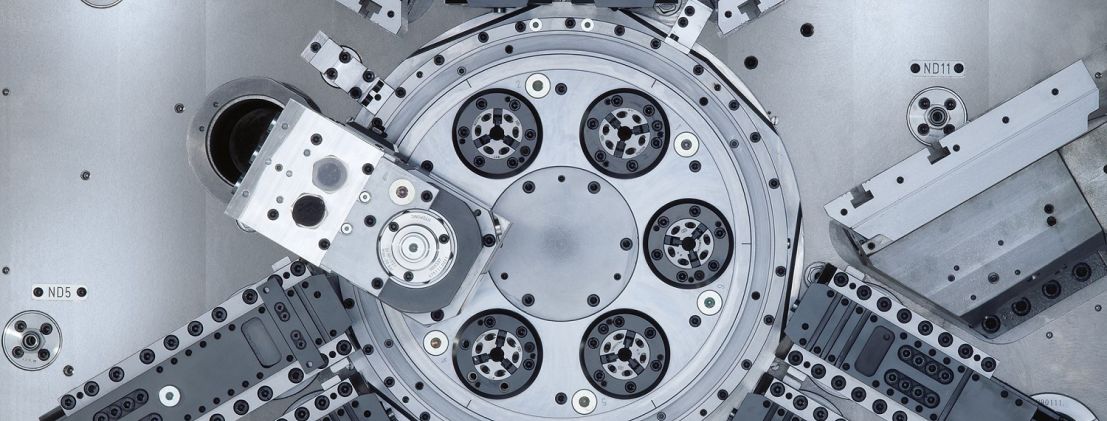
INDEX MS16 Plus multi-spindle lathe features six spindles
With the new extended version INDEX MS16 Plus of the MultiLine series, the Esslingen multi-spindle specialists present a CNC multi-spindle lathe featuring six spindles for up to 22 mm diameter parts. The six-spindle machine, built from a multi-spindle modular component system, is intended to replace the widely used but costly to set-up fast cam-controlled multi-spindle lathes that still dominate the market when it comes to machining workpieces of simple to moderate complexity.
The INDEX MS16 Plus scores not only because it combines the speed of a cam-controlled machine with the flexibility of CNC technology, but also because its extremely compact dimensions (1,300 mm width) require no more space than current cam-controlled multi-spindle machines. In addition, the MS16 Plus offers exceptionally high ease of setup and more versatile machining options compared to cam-controlled machines. To keep up with the speed and efficiency of cam-controlled multi-spindle lathes for small parts up to 22 mm diameter, the INDEX engineers have come up with a number of good ideas.
In the full expansion of the MS16 Plus, each spindle position can optionally be associated with a highly stable grooving or boring slide with 1 NC axis and a cross-slide with 2 NC axes (X- and Z-axes) that are arranged around each work spindle in a V-shape, allowing easy use of several tools simultaneously on each work spindle. The NC-controlled synchronous spindle for gripping the workpiece and an NC cutoff and back-boring slide provide optimal conditions for efficient production of turned parts with simple to medium complexity and up to approx. 70 mm length. Optionally, machining on the cutoff side can be divided between a cutoff slide and a separate rear machining unit to reduce cycle time.
As usual with INDEX multi-spindle machines, all technologies that are available on turning centers and automatic lathes can also be used on this new six-spindle MS16 Plus, such as: turning, drilling, milling, tapping, deep hole drilling or slotting.
Live tools and auxiliary equipment that can be mounted on all slides as well as the C-axes of the work spindles open up additional production options, such as: off-center drilling and tapping without compensating chuck, oblique and cross drilling, contour milling, hobbing and polygon turning.
Infinitely variable speed control
The familiar advantages of the INDEX CNC multi-spindle machines, such as the use of maintenance-free and powerful hollow-shaft motor technology in all work spindles and the optimum selection of cutting data via the CNC program, are of course implemented on the MS16 Plus as well. The six high-torque work spindles with a drive power of 8.7 kW per spindle, which are cooled on demand by the fluid-cooling system proven in the MultiLine series, run in a globally unique, fluid-cooled spindle drum that is precisely locked through a three-part Hirth coupling after each indexing operation. Thermal growth of the spindle carrier is minimized and the spindle bearing temperature is kept at a low level, which benefits the service life and leads to optimum thermal stability.
The speed of each of the six spindles can be controlled separately. During machining, it is always possible to program the optimum speed, which can still be varied during cutting, for each spindle position and each cutting edge of the tool. Speed changes and positioning of the spindles are possible even during drum indexing, thus avoiding any additional secondary processing times. Further advantages that result from this are optimum chipping, maximum surface quality, short production times per piece, and extended tool life. The MS16 Plus can therefore be used to machine even difficult-to-cut materials accurately and efficiently.
NC grooving slide
To achieve short cycle times comparable to those of cam-controlled multi-spindle automatic lathes, extremely stiff and highly dynamic NC grooving slides with excellent damping properties are used. As usual with a cam-controlled multi-spindle machine, the grooving slides can be equipped either with a form cutting tool for cutting a workpiece contour or with accessories for live tools. For quick and easy tooling, the NC grooving slides are equipped as standard with INDEX W-serration – another first for multi-spindle automatic lathes. Optionally, an NC boring slide can be set up with a slide travel of 70 mm instead of an NC grooving slide.
NC cross-slides for maximum flexibility
In addition, each work spindle can be fitted with an NC cross-slide. The low-mass and compact cross-slides with integrated NC drive are appealing due to their low moment of inertia and the resulting high dynamics, which facilitates outstanding acceleration in practical application. The advantage of a hydrostatic sliding guide in the feed axis (Z) is its outstanding damping characteristic that prevents the transfer of the machining vibrations to the adjacent slide via the headstock. This helps to mitigate vibration and rattling while workpieces are being machined – even when the most diverse machining processes are being performed concurrently by the six spindles. For example, one spindle can be used for heavy-duty roughing while high-precision finishing takes place on another spindle without sacrificing surface quality. In addition, the hydrostatic bearing is wear-free – there is neither friction nor a stick-slip effect. The 5 NC cross-slides are designed for a slide travel of 45 mm in X and 70 mm in Z.
Simultaneous machining
The grooving or boring slides and cross-slides are arranged in a V-shape around each work spindle, thus allowing trouble-free use of several tools at the same time. The machining type is determined by the tool holder. All operations (external – external, internal – external, stationary – live, and live – live) can be freely defined in almost any spindle position. Valuable time can be gained, for example, by performing the internal operations while grooving the external contour of the workpiece with the cross-slide. Each cross-slide can be equipped with several tools – internal and external, stationary or live – that can be engaged in succession thanks to CNC technology. This often makes it possible to reduce the number of required slides in the machine configuration or to increase the possible number of machining operations.
Easy to retrofit
Since the MC16 Plus, due to its compact design, makes it possible to omit any slides as complete units or to retrofit additional slides easily in the field, simple configurations can be put together that can be upgraded later when necessary. To match a cam-controlled machine of current design, which has only a grooving slide and a Z slide per spindle position, for example, the NC cross-slide of the MC16 Plus can be equipped with a fixed housing instead of the X-axis, on which only one tool is mounted that only moves in Z. Or you can leave out all the grooving slides, for example, and use only the cross-slides, which allow the use of different tools on all six spindles simultaneously thanks to NC technology. In specific cases, one will choose a reasonable number of NC grooving/boring slides and NC cross-slides tailored to the range of parts to be machined.
Extremely fast spindle stop and cutting off
For rear-end machining, the MS16 Plus is equipped with a synchronous spindle driven by a hollow-shaft motor allowing speeds up to 10,000 rpm and which can move 140 mm in Z at 30 m/min to engage several rear-end machining tools on the NC cutoff slide with the X- and Z-axis in succession more quickly. To achieve the shortest cycle times possible, the synchronous spindle accelerates to max. 10,000 rpm in less than 0.7 s thanks to its high power output of 9 kW, also allowing for an extremely fast spindle stop when ejecting the finished parts. The ejector in the synchronous spindle is actuated hydraulically. Besides a cutoff tool, the NC cutoff slide can optionally hold two stationary or two live tools and another stationary tool for rear-end machining. Thanks to its increased stroke of 94 mm, the NC cutoff slide requires no stroke extender, and it can travel at a rapid traverse rate of 30 m/min.
27 NC axes
The total of 27 NC axes of the MS16 Plus at full expansion (5 NC grooving or boring slides, 5 NC cross-slides, 1 NC cutoff and/or back-boring slide, 6 work spindles, 1 NC synchronous spindle, drum indexing) plus an additional 5 free NC axes of possible CNC-controlled auxiliary equipment are controlled by an INDEX C200-4D (based on the latest generation of the Sinumerik 840D Solutionline control) featuring the new INDEXoperate user interface for multi-spindle automatic lathes. All necessary setup data are stored with the part program, which allows unbeatable fast job changes. Numerous functions such as part production time evaluation or block time measuring help achieve optimized part programs. Of course, all of the programming tools familiar from the INDEX MultiLine series can be used for the MS16 Plus as well. For example, INDEX offers virtual machine setup on a PC workstation also for the MS16 Plus. This reduces the setup time and avoids collision errors.
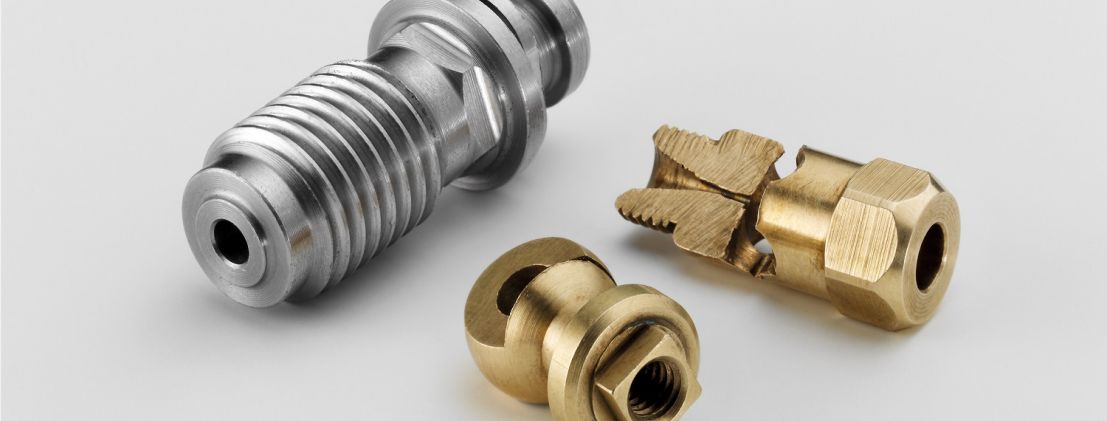
Optimal easy setup
The front-open design known from the INDEX MultiLine series in conjunction with the intelligent arrangement of the tool carriers on the MS16 Plus not only provides optimal accessibility, but also makes a longitudinal slide block superfluous. This ensures unhindered chip flow, resulting in high process safety. Especially during changeover, the unobstructed accessibility allows for tremendous cost saving. And even at full tooling there is still enough room for the free flow of chips into the machine's built-in chip conveyor, which is installed in the longitudinal axis of the machine, requiring minimal space.
To save space, the control cabinet for the MS16 Plus was simply “put on the machine”. This approach has been applied to INDEX multi-spindle machines for nearly 20 years. Along with its compact size, the machine also comes with a high power density.
Inherent energy efficiency
For years, all INDEX machines have met the demand for reduced energy consumption. The INDEX MS16 Plus is no exception and requires at full expansion less than 50 kW, scoring with the following benefits: weight-optimized components for reducing energy consumption and for increasing the dynamic response; energy recovery by means of regenerative drives; energy shutdown of units that consume large amounts of energy after a user-defined time (standby mode); minimized friction based on optimally paired materials and low-friction bearings (hydrostatic circular guide); intelligent cooling principles, for targeted cooling of the machine, economical use of waste heat.
Space-saving peripherals
For the MS16 Plus available are an INDEX bar guide (spring tubes) and an automatic loading magazine as rack and bundle loader, as well as a space-saving cleaning system with integrated vacuum rotation filter and chip conveyor included in the machine design.