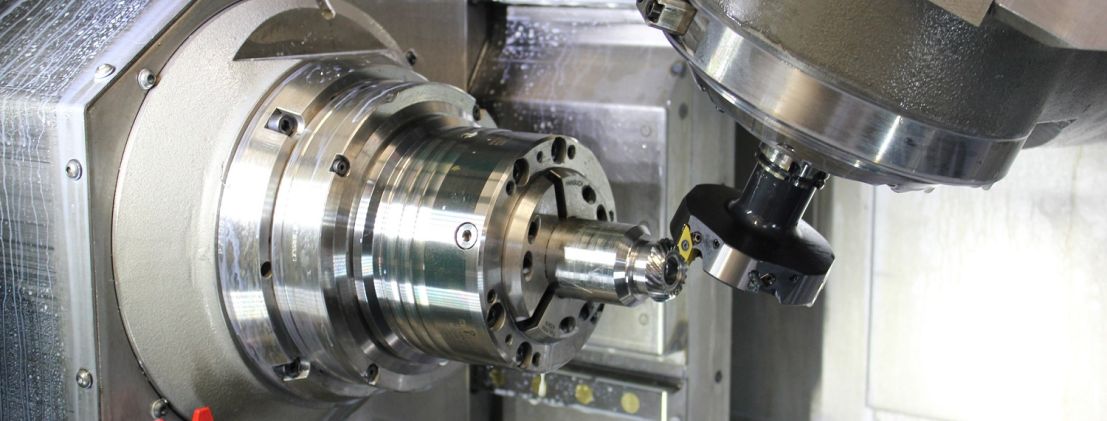
Bevel gear cutting using INDEX turn-mill centers
INDEX has developed a “bevel gear hobbing” package, which consists of a specially designed control cycle and four INDEX cutter heads with module-dependent inserts. Equipped with these features, the turn-mill centers INDEX R200 and INDEX R300 become gear-cutting machines on which spiral bevel gears (module from 0.6 to 4 mm) can be produced – from bar stock, with front and rear end machining, complete in one setup or alternatively as a pure two-spindle gear cutting machine. Compared to the conventional process chain with classic gear-cutting machines, users can achieve shorter cycle times and better geometry and position tolerances. And it is much more flexible.
To denote INDEX-Werke as a pure lathe manufacturer would not tell all about the innovative Esslingen company. That it's because many other technologies for metalworking are incorporated in the INDEX machines: For a long time there have been turn-mill centers that master the two chipping techniques almost equally well. Also the grinding technology is fully integrated on various INDEX machines. Now the machine tool manufacturer offers a technology package that makes the turn-mill centers INDEX R200/R300 also full-fledged gear-cutting machines. By hobbing using a continuous indexing method – which corresponds to the Klingelnberg Cyclo-Palloid method 1) – spiral bevel gears can be produced with constant tooth height in a module range of 0.6 to 4 mm.
The starting point of the development initiated by INDEX lies in its own manufacturing governed by the principle: quality-determining components are made in-house. When the tool holder production was reorganized several years ago, the decision was made to produce the required bevel gears themselves. After all, their quality is largely responsible for smooth running, the transmissible torque, and wear. Since no sufficiently productive, modern gear-cutting machine was found on the market for these parts, the management decided to technologically upgrade its own turn-mill center accordingly.
To sum it up: The technology integration was so successful that INDEX meanwhile covers its in-house need for bevel gears by an INDEX R200 and is now offering the technology to the broad market. Dr. Volker Sellmeier, Head of Technology Development, explains: “My team is committed to offering the customer a significant added value through the integration of machining processes such as gear cutting. We have achieved this with the new INDEX method for bevel gear hobbing, which enables complete machining on one machine, because you can achieve significant advantages in terms of cycle time, process and quality.”
INDEX R-series for bevel gear cutting
Bevel gear cutting requires a machine with high rigidity and a B-axis as the basis. Due to their excellent static, dynamic and thermal properties, the innovative turn-mill centers of the INDEX R-series offer themselves, provided they are equipped with the “bevel gear hobbing” technology package. Their axis configuration and equipment with two milling spindles on Y-B-axes running in hydrostatic bearings make it possible to machine on the main and counter spindle simultaneously in five axes.
However, according to Dr. Volker Sellmeier, one is not fixed entirely on the R machines: “In principle, it is possible to transfer this technology to other machines, such as the INDEX G220. For mass production, it is also possible to port the technology package to a multi-spindle machine.”
Of particular importance are the tools that are developed and distributed by INDEX. Two cutter heads are required per bevel gear, which differ slightly in their cutting circle radius to produce the longitudinal crowning. INDEX offers the cutter heads in four different sizes that can be fitted with up to six carbide inserts and feature internal cooling. In contrast to the classical Cyclo-Palloid method with an interlocking cutter head, the INDEX method uses two separate cutter heads per bevel gear. Dr. Sellmeier explains: “The two cutter heads provide a larger number of cutting edges. This allows us to achieve a higher cutting performance. We also have more freedom for flank modifications and correction of the contact pattern.”
A control cycle developed by INDEX is another essential part of the technology package. The user enters there the same parameters as on a conventional gear-cutting machine. These include, for example, machine distance, eccentricity and auxiliary angle. The cycle translates these values into the movements of each axis so that at the end the same relative movements are effected as on a conventional gear-cutting machine.
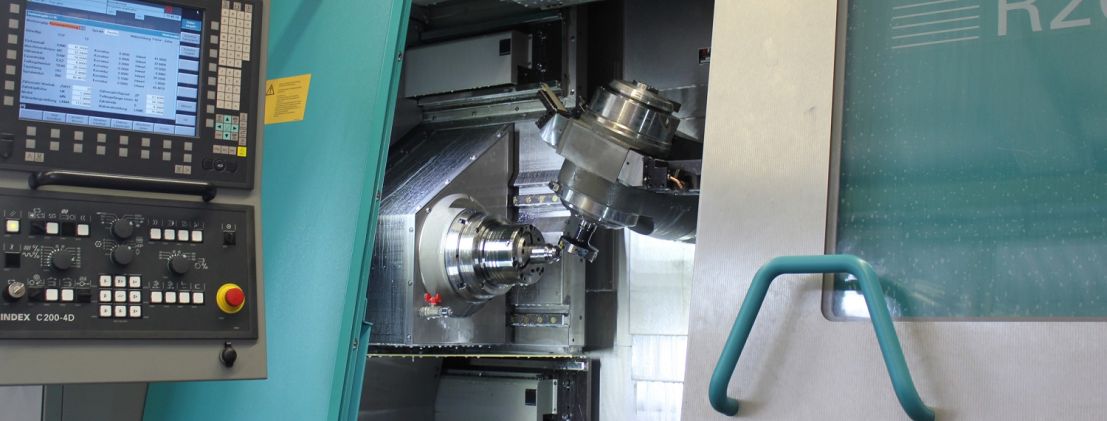
Complete machining on a single machine
While the workpiece has to be set up on several individual machines for turning, drilling, milling, gear cutting and deburring in the classical gearing process chain, INDEX's approach is to run all operations on the turn-mill center. The bevel gears are turned, drilled, milled and finally cut on a single machine. Even brushes for deburring can be set up. The soft machining process is thus completely autonomous, according to INDEX with a process-reliable gear quality of IT5. This is then followed by hardening. A final finishing process is usually required only for the mounting distance and the polygonal shaft/hub connection.
The benefits already start with material usage. As the INDEX R-series can handle bar stock, automated operation is possible even without a workpiece handling system. An integrated gantry-type removal system is available for automatic parts removal. Front and rear-end complete machining with different cutting methods result in shorter cycle times and distinctive benefits in terms of cost per piece. Dr. Volker Sellmeier provides figures: “When we machine the typical bevel gears with module 1.15 mm and approximately 25 teeth for our tool holders completely from bar stock, we are now reaching a cycle time of less than 3 min. The share of gear cutting amounts to about 30 seconds.”
While conventional gear-cutting machines do not have a tool change magazine, the INDEX R200/R300 allows the stocking of sibling tools, among others, for setup when needed, thereby allowing autonomous production over several hours. Complete machining also brings quality benefits. Because the gearing and the (INDEX-typical) polygonal shaft/hub connection are created in one setup, re-clamping errors are avoided and tight geometry and position tolerances are maintained.
Small and large series
INDEX addresses with its gear technology both contract manufacturers, which need to produce small lot sizes with high flexibility, and mass producers, which want to produce bevel gears in large quantities at minimal cost. The investment is relatively low compared with specialized machines. Also the consumption costs are kept within manageable limits, since the cutter heads are equipped with interchangeable inserts. Therefore, flexibility is high: In addition to bar stock machining, which is best primarily for small quantities, it is recommended for series production to use the R machine as a pure gear cutting machine and working on the main and counter spindles simultaneously. Dr. Volker Sellmeier explains: “This requires the use of an automated workpiece-loading and unloading system that loads the blanks and removes the finished parts gently. We offer a quadruple gripper with two stations on the main and counter spindle that picks up the finished parts, rotates and then loads new blanks. This way we use the machine as a kind of double-spindle machine, cutting the time per piece in half.“ And ultimately the INDEX “gear cutting machine” remains of course a versatile turn-mill center.
Experience and additional software
INDEX is happy to pass their know-how gained in its technology development and its own manufacturing on to its customers, providing various training courses for handling the turn-mill centers and the “bevel gear hobbing” technology package. Supporting software is provided in cooperation with GWJ Technology, an engineering firm from Braunschweig. The company has developed a software program called eAssistant, which allows the design of bevel gears.
Also helpful is GWJ's separate module GearEngineer, which allows calculating the target data of the edge topology. The data is loaded on a 3D coordinate measuring machine for target/actual comparison. The measured deviations can easily be entered in the INDEX control cycle, which automatically calculates the corrections for the machine setting data.