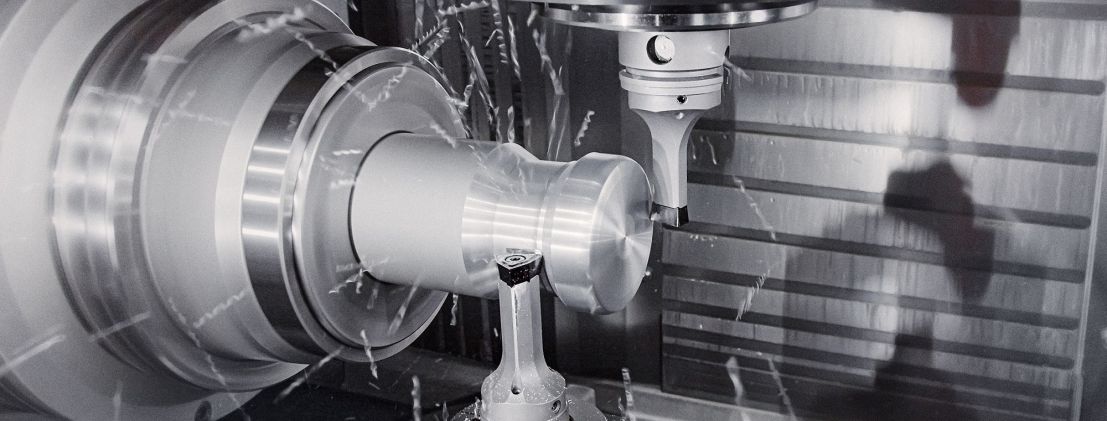
High Dynamic Turning on INDEX Turning Machines
At the INDEX Open House 2025, High Dynamic Turning (HDT) emerged as a central focus, demonstrated across three machine platforms. Visitors witnessed the established HDT setup on the INDEX G320 turn-mill center, where the HDT tool operates via the milling spindle. Debuting alongside this was a newly developed geared tool holder from INDEX, allowing HDT tools to be utilized in the turret. This innovation made it possible to perform simultaneous HDT operations on a single workpiece using two tools on the TRAUB TNX220. Additionally, INDEX presented how HDT enhances productivity on the MS40-6 multi-spindle turning machine.
High Dynamic Turning is a machining strategy designed to reduce cycle times significantly. It achieves this through a dynamically adjustable tool inclination angle, controlled via the CNC system. This flexibility enables efficient machining of complex contours without requiring multiple tool changes. HDT also offers improved chip control, higher feed rates, and extended tool life. Unlike traditional turning processes, HDT requires a high-precision, backlash-free rotational axis to orient the tool at various angles relative to the workpiece. While this is usually provided by the milling spindle in a turn-mill center, HDT employs it differently—using the Y-axis for positioning, while the spindle's rotational axis defines the cutting edge angle. This allows a single tool to perform face turning, OD turning, shoulder machining, and more, always maintaining the ideal cutting angle.
Tooling concept from Ceratizit
The tooling concept was introduced to the market in 2019 by Ceratizit with the FreeTurn system. This tooling system includes specially designed holders and indexable inserts with three cutting edges of varying geometries. By simply rotating the tool, users can switch between roughing, finishing, and directional cutting edges. This eliminates the need for multiple tools, reduces changeover time, and saves tool magazine space. At the Open House, INDEX and Ceratizit jointly demonstrated HDT with FreeTurn tools on the G320, comparing static (fixed-angle) and dynamic (adjustable-angle) HDT operations. According to Ceratizit, machining times can be reduced by up to 25% with HDT compared to conventional turning methods.
New Possibilities with Turret-Based HDT
A major advancement showcased was the introduction of HDT on turret-based machines. Traditionally, HDT’s application in such machines was limited due to the precision required to orient the cutting edge accurately. INDEX addressed this by developing a new tool holder featuring an internal wave gearbox with a 1:100 gear ratio. This results in extremely fine control—each full rotation of the drive motor translates into just 3.6 degrees of tool rotation. The gearbox is also self-locking, ensuring a completely backlash-free setup.
This innovation enables HDT tools to be used in any turret-equipped machine, such as the TRAUB TNX220. In a dual-HDT configuration, both the turret-mounted tool holder and the milling spindle were outfitted with FreeTurn tools, demonstrating synchronized turning operations on a single workpiece.
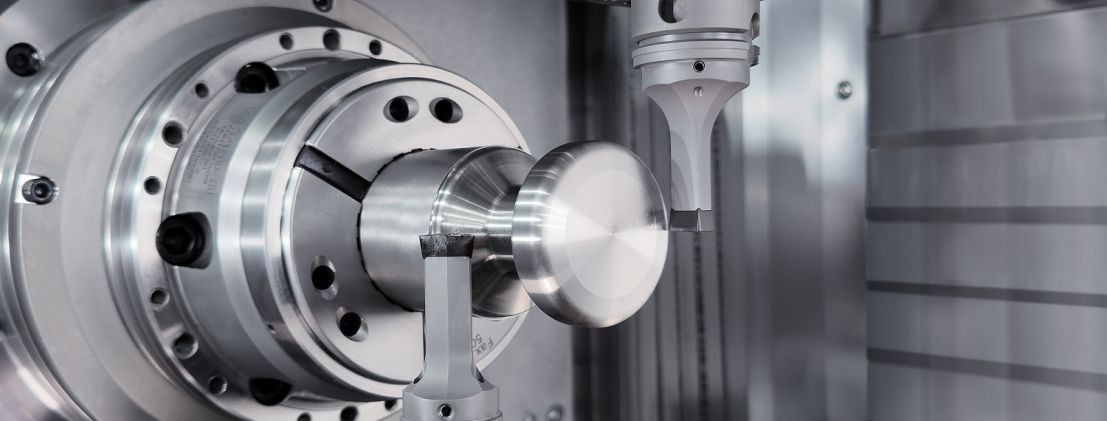
HDT in Multi-Spindle Machining
INDEX also integrated HDT into its MS40-6 multi-spindle turning center. This implementation required rotational control of the tool and Y-axis feed motion. The tool carrier’s swivel axis, combined with the workpiece’s C-axis rotation, effectively simulates a Y-axis movement. A direct-drive spindle, originally developed by INDEX for milling and gear cutting, drives the rotational motion. With no mechanical backlash, it’s ideal for HDT. To support this, INDEX collaborated with tooling specialist Schwanog to develop a modular combination tool mounted via a PSC interface. This tool combines an HDT insert, a form grooving insert, and a profiling insert in a single station, allowing diverse machining tasks without tool changes.
In live demonstrations, a single HDT insert machined both a semi-circular groove and a shoulder, covering tasks that would typically require three separate tools and stations. This approach frees up slides and increases efficiency on multi-spindle machines.
Expanding Potential Through Software and Modular Tooling
Looking ahead, INDEX sees further potential in compact tooling configurations. The company is exploring mini-turret solutions that integrate multiple tools into one holder, significantly increasing the number of available cutting edges on machines like the INDEX C100 and C200. On the software side, programming HDT operations is becoming more streamlined. For TRAUB machines, a dedicated interface already supports simplified HDT programming. For INDEX production turning machines, the necessary axis macros are available, and an intuitive user interface is currently under development.
With its combination of mechanical innovation, software integration, and strategic tooling partnerships, INDEX is advancing HDT as a versatile, high-efficiency process for a broad range of turning applications.