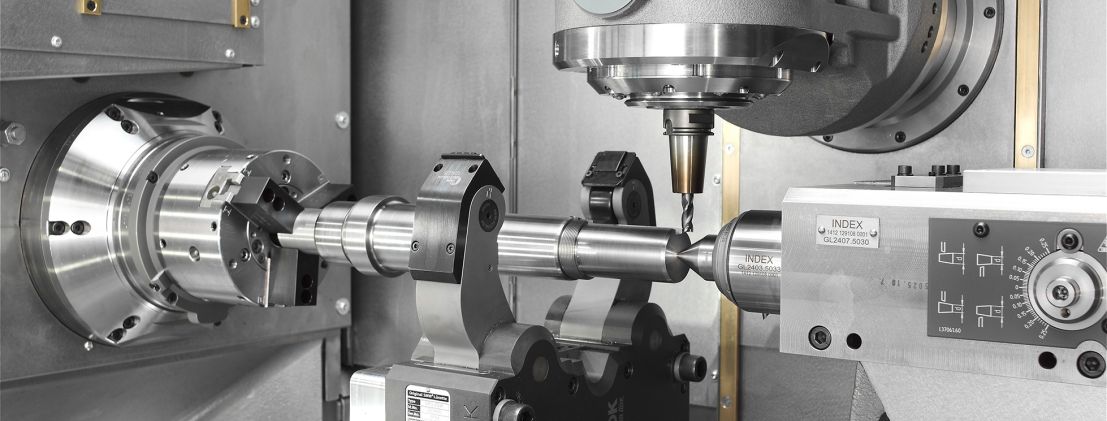
INDEX prepares G220 turn-mill center for the future of machining
With the turn-mill center G220 INDEX continues the tradition of the successful compact G-series of turn-mill centers – but with a complete redesign, responding to market requirements such as the increasing complexity of components and decreasing batch sizes. Thanks to a motorized milling spindle capable of five-axis milling and a tool turret with Y-axis, the G220 operates with great flexibility and can execute virtually any turning or milling machining process.
With increasing numbers of functions being integrated in many workpieces, the future demands great flexibility and performance density of machine tools. In addition, the components are generally becoming smaller, while the number of variants is rising. Complete machining is one key to overcoming this challenge, at the same time meeting growing quality requirements and remaining competitive in terms of cost.
In view of this, the development department at lathe manufacturer INDEX, a company with a history going back 100 years, contributed its entire expertise to the new design of the G220 turn-mill center. The result is a compact machine that allows turning and milling operations (even with five axes) with the usual high quality on an approximately 10 m2 footprint.
It is based on a heavily ribbed cast iron machine bed which, together with the generously sized linear guides in the X and Z-axes, ensures excellent stability and damping properties. The vertical panels enclosing the work area are formed of a one-piece cover sheet in place of high-maintenance telescopic plates. The Z-axis slides with the motorized milling spindle and the Y/B-axis with hydrostatic bearing support are symmetrically arranged as a gantry. All key machine components have been optimized with the help of calculation and simulation models to ensure both light and stable construction, consequently improving the high dynamic response as well as the outstanding cutting performance of the machine.
Ergonomic design
Ergonomic considerations were also at the forefront of the new design. The turquoise “ergonomic belt” running around the machine enclosure marks out an area ideally accessible to the machine operator. All actions required to set up and operate the machine can be carried out under optimum ergonomic conditions in this area, because all relevant components, i.e. main and counter spindles, turrets, motorized spindle and tool magazine or tailstock and steady slide, as well as the control panel of the machine are located within this ergonomic area.
Generous space for efficient turning and milling
The work spindles (main and counter spindles) are fluid cooled and have a bar capacity of 65 mm, optionally 90 mm (chuck up to 210 mm diameter). The distance between the spindles is 1280 mm; the maximum turning length is 1000 mm. The motorized spindles of the main and counter spindles allow productive turning operations through their high dynamics, power and torque.
The spindle center is located 1350 mm above the ground. The tool turret is located in the lower area, giving the customer the choice between VDI 25 or VDI 30 tool mountings. Accordingly, the tool turret has 18 or 12 stations, all of which can be equipped with individually driven tools (max. 6 kW, 18 Nm and up to 7200 rpm).
The tool turret can move not only in the X and Z direction (index-through space in Y 140/160 mm and in Z 150 mm), it also has a linear Y-axis with a traversing range of +/-50 mm. Thanks to the large work area and the distance between the main and counter spindles, simultaneous machining is possible with the motorized milling spindle and tool turret at the main and counter spindles – even on the face side – with no risk of collision.
The fluid-cooled motorized milling spindle is arranged above the rotation axis. Its powerful drive (max. 11 kW, 30 Nm and 18,000 rpm) and B-axis, directly driven by a torque motor and running in hydrostatic bearings, makes it possible to perform almost any drilling and milling operations due to high damping and stiffness.
With a Y stroke of +/-80 mm, a swivel range of the B-axis of -50 / +230 degrees, as well as a large X travel, which even reaches 30 mm below the center of rotation, allows the operator to produce any geometry easily and productively with up to five-axis machining. The use of long projecting tools, particularly useful for multi-axis machining, also presents no problems.
Double-row tool magazine
The motorized spindle operates with a single or optional double-row tool chain magazine, which provides space for 70 or 140 tools (HSK-T40). The stations feature a tilting basket design which protects the tools against contamination from oil and chips. Tools with dimensions of up to 50 mm diameter and 200 mm length can be used as standard. Alternatively, if adjacent spaces are free, tools of up to 120 mm diameter and 300 mm length can also be used. A further benefit of the tool magazine in the G220 is the integrated drill breakage monitoring unit. Before a tool is returned to the tool magazine following use, an automatic check to determine if it is still fully available is performed using a light barrier. The unit can optionally be combined with a tool breakage and wear monitoring system which evaluates the axis drives’ motor current consumption.
Tailstock and steady slide
For effective complete machining of long or wavy workpieces, in addition to a CNC-controlled tailstock (pressing force max. 8,000 N, quill with mounting DIN 2079 / SK30), a steady slide (steady head with clamping range 12-152 mm in diameter) is available replacing the lower tool turret.
INDEX has installed a CNC-controlled and CNC-programmable gantry-type removal unit for the gentle removal of machined workpieces. It is capable of unloading both remnants from the main spindle and finished parts from the counter spindle (max 7.5 kg weight). They are then placed on an integrated conveyor belt and discharged from the work area to the right of the machine.
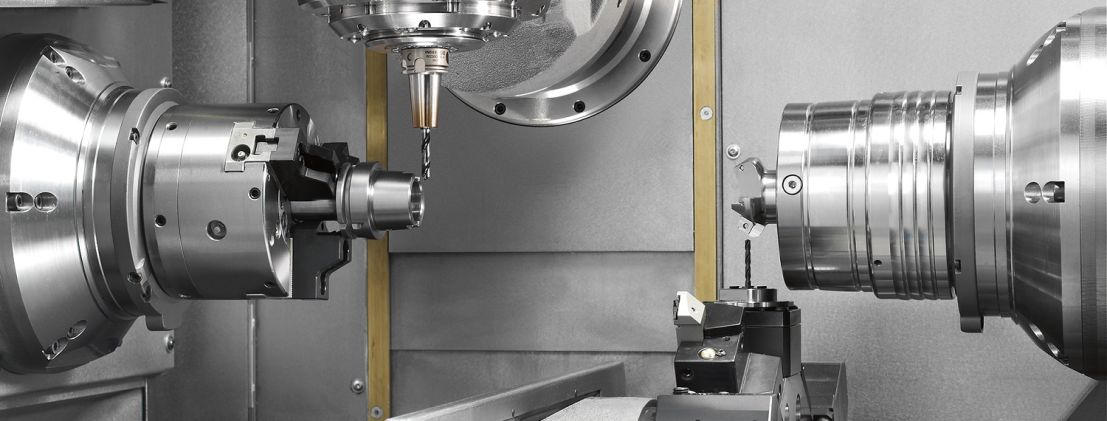
Temperature stability
A robust machine design is not the only thing required to ensure constant high-precision machining: the machine’s temperature stability also has a considerable role to play. In order to dissipate the heat produced in the fluid-cooled spindles and the control cabinet, INDEX has integrated a hydraulic circuit with an interface enabling connection to a local cooling unit or a central cooling system. By implementing cooling functions away from the production area and eliminating the traditional fans, noise and heat emissions in the machine environment are reduced to a minimum.
INDEX Xpanel
INDEX now supplies all machines – single and multi-spindle machines as well as turn-mill centers – with the newly developed XPanel operating system. With a 43.5 cm large screen with a fully touch-sensitive surface (multitouch), XPanel allows the user very easy setup and control of INDEX machines. A touch of the finger now suffices to use softkeys directly on the screen to open files, folders and menu trees or to move entire pages on the screen. Even switching the operating areas or enabling/disabling of block skip levels is now done simply by "finger pointing" on the screen.
In addition, even in its standard version, XPanel offers extensive added user assistance through complete integration into network structures. Drawings, setup sheets, user manuals, circuit and hydraulic diagrams, etc. are available directly on the machine without additional hardware.
XPanel unfolds its full strength with an additional industrial PC installed in the control cabinet. This allows the user to run 3D simulations coupled with the machine in real-time or even create complex programs directly on the machine using a CAM system. There are (almost) no limits to data communication as well.
The industrial PC, called VPC Box, allows the operator to run Virtual Machine (VM) developed by INDEX directly on the machine control panel. This “VM on Board” has advanced capabilities and can be used, for example, coupled with the real machine via the virtual NC core. This allows 3D simulation and collision monitoring in a completely new dimension, because INDEX offers various operating modes for “VM on board”. “CrashStop” allows the advance simulation of workpiece programs on the machine. If it detects a collision, the function triggers a prompt machine stop before an actual collision occurs. Using “RealTime”, the machine program can be simulated on the operating panel simultaneously, thereby enabling real-time analysis of the machining sequence in difficult-to-access work area situations. In addition, “VM on Board” can be used to create and test new NC programs directly on the machine during production.
XPanel offers also useful assistance for machine programming via INDEX's proprietary VPro ProgrammingStudio that can be used not only as part of “VM on Board”, but also directly on the machine control. The VPC Box even allows the use of the NX-CAM system with an INDEX postprocessor directly on the machine under the “CAM on Board” button. Of course, other CAM systems and customer-specific applications can be used as well. INDEX allows the user's IT department direct access to the VPC Box industrial PC in the control cabinet for this purpose.