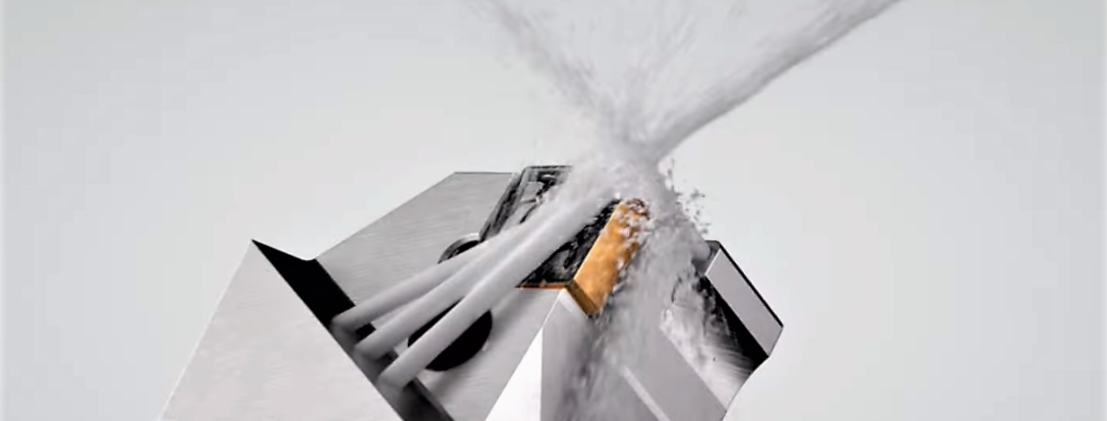
MaxiLock N-DC completes the DirectCooling range from CERATIZIT
A targeted coolant supply is not simply an option for the majority of demanding machining operations: it's also an undisputed efficiency booster. One more reason for CERATIZIT to complement its DirectCooling product range with the MaxiLock-N turning tool holders. Two coolant holes now aim coolant directly at the cutting edge, preventing wear and ensuring stable processes.
When it comes to cooling lubrication, the efficient use of resources and sustainability make simple flood lubrication a thing of the past. The DirectCooling (DC) system from CERATIZIT offers accurate and targeted cooling rather than flood lubrication of the general area - and in doing so delivers the ultimate in precision.
Right on the cutting edge
It's a familiar story: a hose in the turning machine generously distributes the coolant to the machining area. But there is another way to achieve the maximum in cooling performance. The new MaxiLock-N-DC turning tool holders complement the Direct Cooling (DC) system from CERATIZIT and - with their two internal holes - ensure that coolant is directed precisely at the cutting edge. To this end, three nozzles are aimed at the clamping flat from above, while another is directed at the flank from below and as such specifically at the cutting edges. "It is precisely this flank cooling that makes the difference. It extends tool life by 60% compared to cooling that is exclusively aimed at the clamping flat," explains Stefan Karl, Product Manager Cutting Tools at CERATIZIT.
This targeted cooling system is suitable for all materials, although it delivers enormous advantages with ISO-P, ISO-M and ISO-S in particular due to the rapid heat development in the cutting process. "That's where the indexable inserts used show their gratitude above all - with significantly less wear and a longer tool life because less heat remains in the process, not to mention effective chip transportation," adds Stefan Karl. This is ensured by the minimum pressure of 10 bar provided for DirectCooling and the coolant transfer via the turret of the turning all employees or turning-milling centre. The higher the pressure, the better the chips can be directed and removed.
Tailored DC system
A high coolant flow rate has a massive impact on tool life. "But it's not everything," says Stefan Karl knowingly. "Our DirectCooling system achieves flow rates that are almost as high as simple flood cooling. However, it stands apart when it comes to the tool service life, which is more than double the life achieved with uncontrolled cooling - depending on the respective material and machining application!"
Interference contours are a common problem during machining, but not for the holders from the DirectCooling series. Their lengths have all been ideally matched to one another and also offer optimal stability and unlimited flexibility. This is further ensured by the HSK-T universal standard interface for turning tools, which ensures straightforward connection to multifunction machines such as turning/milling centres and milling/turning centres.