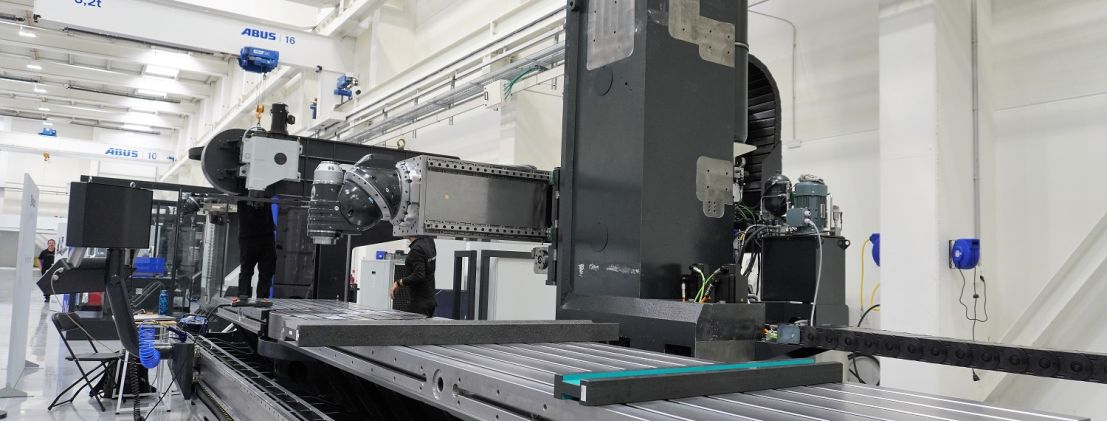
Take a peek into Soraluce's production sites in Bergara, Spain
In mid-June, Soraluce held its highly anticipated Soraluce Summit 2023 event at its production sites in Bergara, Spain. The event provided an exclusive opportunity for customers to gain insight into Soraluce's impeccable machine building process. Alongside the debut of the new Performance Line machine series, attendees were treated to a firsthand view of the brand new assembly plant and were dazzled by an array of impressive projects and demos.
"In recent years, demand for our milling, turning, boring and multitasking machines has increased significantly. There are now about 3,600 machines installed globally and the customer base is growing steadily," says Thilo Borbonus, managing director of Bimatec Soraluce. He says this has everything to do with the increasing need for large workpieces with high accuracy. The aerospace, energy, mould-making and general mechanical engineering industries, among others, are seeing larger and larger parts and constructions, with increasing accuracy requirements. Soraluce's machine tools are developed to meet exactly these needs. Borbonus: "Twenty years ago, we were of the opinion that machines would not get any larger than 20 metres. Today, we are not surprised by an X axis of 64 metres a Y axis of 8 m and customers wanting to machine workpieces with a mass of 700 tonnes. To meet the demand for this kind of machinery, the factory obviously has to grow with it."
To meet the increasing demand for large machine tools, Soraluce has invested in expanding its production capacity. A completely new assembly plant was recently opened in Bergara. The new assembly hall has a floor area of over 2,500 m2, bringing the total floor area of the various factories to 30,000 m2. Needless to say, the new factory was designed based on sustainable criteria. Thus, the new factory is also equipped with solar panels. In total, Soraluce generates about 30% of its energy needs itself.
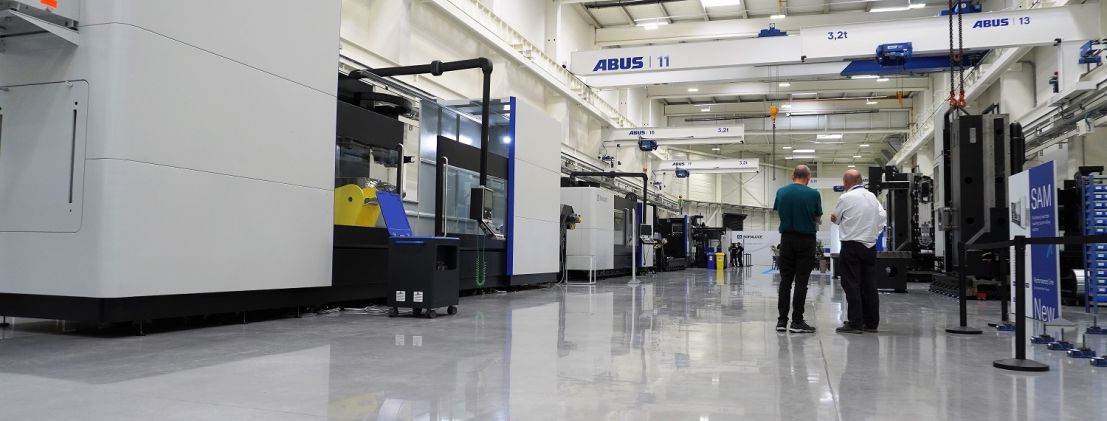
"We manufacture machinetools with our own machines"
Apart from castings, Soraluce produces almost everything in-house. "During the Covid crisis, it became painfully clear that there are risks involved in international supply chains. At that time, Soraluce was already set up to produce as much as possible in-house, and we have only expanded that since then," Borbonus says. Production starts half an hour's drive from Bergara, at Goimek's factory in Itziar. Goimek, like Soraluce, is part of the Danobatgroup and specialises in machining large parts. For instance, structural castings such as machine beds, columns and tables are machined here 24/7 for Soraluce's machines, among others. Remarkably, mainly large processing machines from the Danobat Group are used here, including portal and turning-milling centres from Soraluce, as well as large Danobat grinding machines. Iñigo Kortabarria, Sales Director at Soraluce, says: "The Goimek plant is at the heart of the 100 to 130 machines Soraluce produces per year. By using our own machinery, we can be sure of high quality. In addition, we can test new technology directly in practice and provide feedback to the R&D department. This allows us to develop and market new technology quickly and reliably."
Ideko: the source of innovation
All the new developments being tested at Goimek, among others, come from Ideko, based in Elgoibar. Ideko is the technology centre of the Danobatgroup. With a workforce of 120 employees and a budget of 11 million euros per year, Ideko has all the resources to come up with the latest innovations. "At Ideko, technology is developed for the entire group. This has the advantage of sharing knowledge and expertise. For example, Danobat's grinding expertise is used in Soraluce's multitasking machines, which combine milling, turning and grinding," says Kortabarria. Santi Fernandez of Ideko adds: "The amount of knowledge and experience is growing at lightning speed because we share everything with each other. That is the strength of a cooperative. Our R&D is now divided into several segments, including ICT and automation, production technology, design and precision engineering and dynamics. Well-known technologies that originated here at Ideko and are now being successfully applied include DAS+ (Dynamics Active Stabilizer) and DWS (Dynamic Workpiece Stabilizer), to name but a few." DAS+ prevents vibrations in the machine by using sensors to measure vibrations in the main spindle. Two built-in actuators then create counter-phase vibration that eliminates the vibration effects of the process. DWS, on the other hand, eliminates chatter in the workpiece that usually occurs when slender and thin-walled parts or assemblies are machined. DWS is placed on the workpiece using a magnet or pneumatic system. Sensors then measure vibrations in the workpiece, after which DWS also creates a counter-vibration. Thanks to DAS+ and DWS, the machine's performance can be maximised. The result is higher productivity and tool life, as well as much better surface quality. At the Summit, Soraluce presented both systems live.
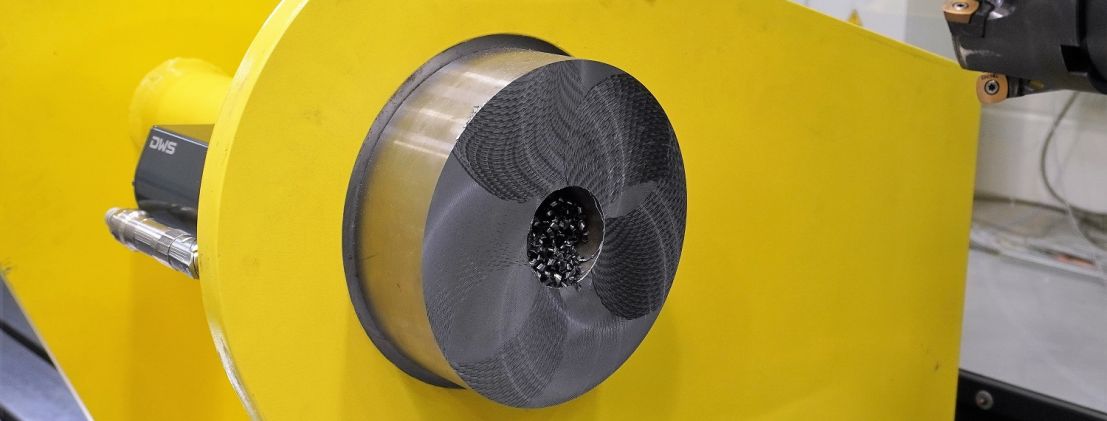
Spindle is the heart of the machine
From Itziar and Elgoibar, we return to Bergara, where Soraluce has also made plans for a new facility for milling head production. This state-of-the-art production centre will open in 2024 to increase capacity. Indeed, in addition to manufacturing all machine components, inline motors and heads are also be developed and produced in-house. "The milling head is the most important part of the machine because it is largely responsible for productivity and accuracy. We therefore place high demands on this. For example, the concentricity tolerance is a maximum of 2.5 micrometres. To achieve this kind of accuracy, the whole process has to be perfect," says Jon Ander Munagorri, Sales Area Manager at Soraluce. To mill the high-precision heads, Soraluce has invested in a new milling machine from Yasda set up in an acclimatised room. "Even the foundation is cooled to achieve the desired accuracy". In the new facility, another identical Yasda will be added to the machinery fleet. This will partly serve as a back-up to ensure delivery reliability. After machining and assembly, the milling heads are extensively tested and checked for temperature and vibration during an eight-hour cycle.
Special projects
The Summit offered an impressive overview of Soraluce's portfolio. For example, the machine builder showed a number of special projects. Highlights included an FR 14000 milling boring machine developed for machining concrete columns for wind turbines. The machine is equipped with a special head for machining the desired contour. Further down the hall was a large five-axis machine for machining composite aerospace parts. This machine too was equipped with a special head with an extraction system to remove dust. Also impressive was a 68-metre-long automated cell with 14 3.5 x 3.5-metre pallets and a tool magazine with 500 tools. It takes Soraluce as much as 1.5 years to produce such a complete cell. "Projects like this are a great calling card. They show that we think along with the customer and that, on the contrary, we can also deliver unique solutions," says Borbonus.
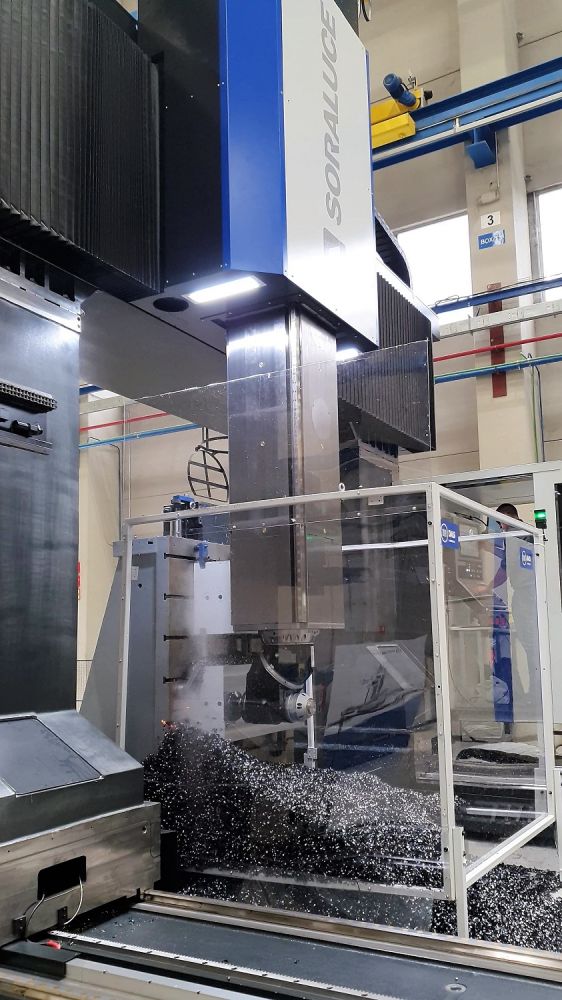
New Performance Line
The 500 customers attending the Summit did not just come to take a look at Soraluce's new assembly plant. For most visitors, the highlight this year was the presentation of the new Soraluce Performance Line. With one basic design and three machine concepts, this new line offers an endless number of solutions to meet specific customer requirements. "Due to the modular design, all machines in the Performance Line share key components such as the column, ram and milling heads. This ensures higher reliability, easier maintenance and high flexibility to arrive at the most suitable solution," says Borbonus.
For the Performance Line, Soraluce applies all the experience gained from the development of their larger models. Thus, the new machine series has the same design principles as Soraluce's other machines. The machines feature a cast-iron frame, linear guides and active and passive damping technology. Furthermore, we find direct-drive motors with high power and torque in the ram. The motors are water-cooled for better thermal stability. Furthermore, the Performance Line offers a new choice of milling heads, including high-quality mechanical heads with automatic rotation, high speed and high accuracy. The heads are also water-cooled for maximum stability and accuracy.
The Perfomance Line consists of three concepts: the TA bed milling machine, the FA 'Floor Type' milling and boring centre and the SA starbed milling machine. Find out more about these machines.
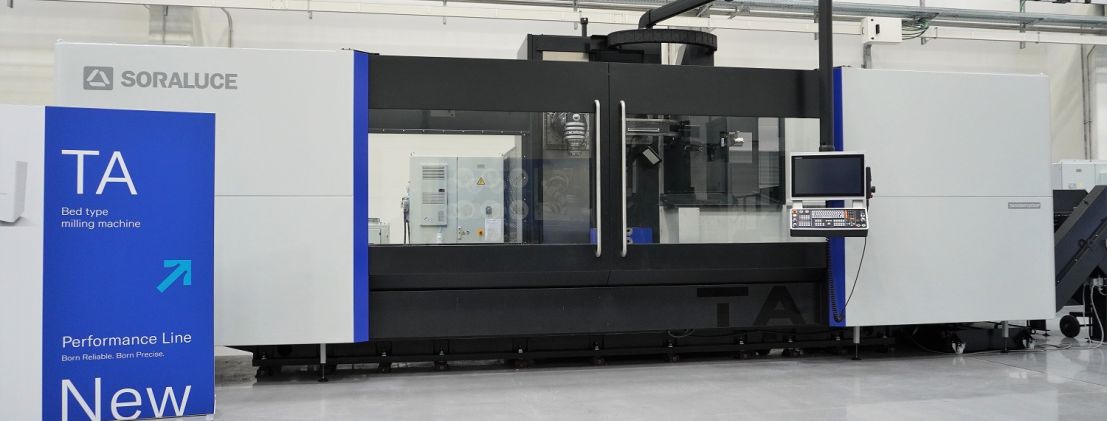
*This is automatically translated. It may contain translation errors...