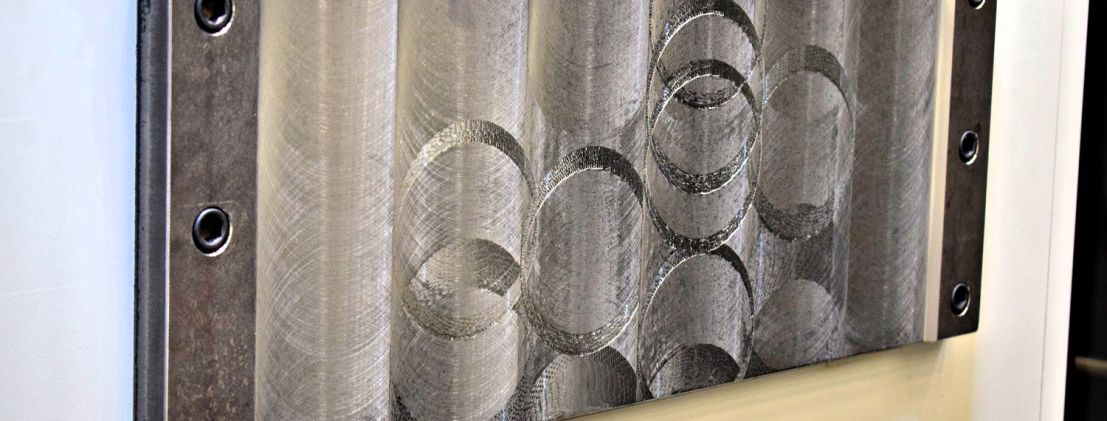
Soraluce Eliminates Vibrations with DAS+ and DWS Technology
Tackling vibrations directly at the source is the solution for Soraluce to prevent adverse effects of vibrations in tools, machines and fixtures. To this end, the machine builder has developed a number of systems that actively monitor and control the machining process.
In 2015, Soraluce presented the Dynamics Active Stabiliser (DAS) system for the first time. This system suppresses vibrations that occur during the machining process. DAS+ prevents vibrations in the machine by using sensors to measure vibrations in the main spindle. Two built-in actuators then create counter-phase vibration that eliminates the vibration effects of the process. According to Soraluce, several analyses carried out on customers operating a machine with this system show that in 99 per cent of applications, vibration is prevented thanks to DAS+. As a result, in many cases, machining performance can improve by up to 300%. This while the surface quality of the workpiece goes up significantly, tool life is extended by up to 30% and because the machine has less to endure, maintenance costs go down. According to Andreas Lindner, managing director of Bimatec Soraluce in Limburg, D, the productivity gain is due to the fact that the cutting parameters do not have to be adjusted downwards to avoid chatter. "Instead, by absorbing the vibration with a counter vibration, we can increase the cutting parameters to achieve more productivity." The system operates over the entire range of the machine. This means constant efficiency is obtained regardless of the spindle position.
Dynamic Workpiece Stabilizer
With its suite of stabilisation solutions, Soraluce aims to address vibrations directly at the source to prevent adverse effects of vibrations in tool, machine and fixture in real-time. Soraluce's latest solution is its patented Dynamic Workpiece Stabiliser (DWS) system. This system eliminates chatter in the workpiece that usually occurs when machining flexible, slim and thin-walled parts. DWS is placed on the workpiece using a magnet, sensors measure the vibration and the system creates a counter vibration. The top photo clearly shows the difference in surface quality with DWS switched on and off."You have to compare it a bit to noise-cancelling headphones. The headphones produce an identical anti-noise from all the noise signalled from outside. As a result, the sounds cancel each other out, filtering out noise from outside. This is how DWS works, but there is more to it," Lindner explains.
DWS is an active damping device consisting of a controller and one or more actuators placed on the vibration-prone part of the workpiece to be machined using magnets. A total of four of these DWS units can be placed simultaneously and strategically on a workpiece. Each unit weighs 6 kg, making it portable and therefore easy to place on any type of workpiece. Moreover, DWS is not tied to one machine but can be used on multiple machines. This makes the solution economically advantageous.
"DWS is quite an improvement over traditional alternatives. Previously, expensive special tools or fixtures were designed. In addition, for large workpieces, temporary reinforcements were often welded into the workpiece or pieces of wood were placed in strategic locations. These are not the most high-tech solutions and often result in all kinds of unwanted stresses in the workpiece. In practice, this resulted in workpieces that were out of dimension or simply lost their squareness the moment these traditional solutions were removed."
Thanks to DWS, machining time can be significantly reduced. Where previously all cutting parameters had to be adjusted downwards to generate as little vibration as possible in the workpiece, machining performance can be fully exploited with DWS. Especially for large workpieces that are generally machined with Soraluce machines, hours of machining time can be saved. This will improve dimensional and surface quality and also increase tool life.
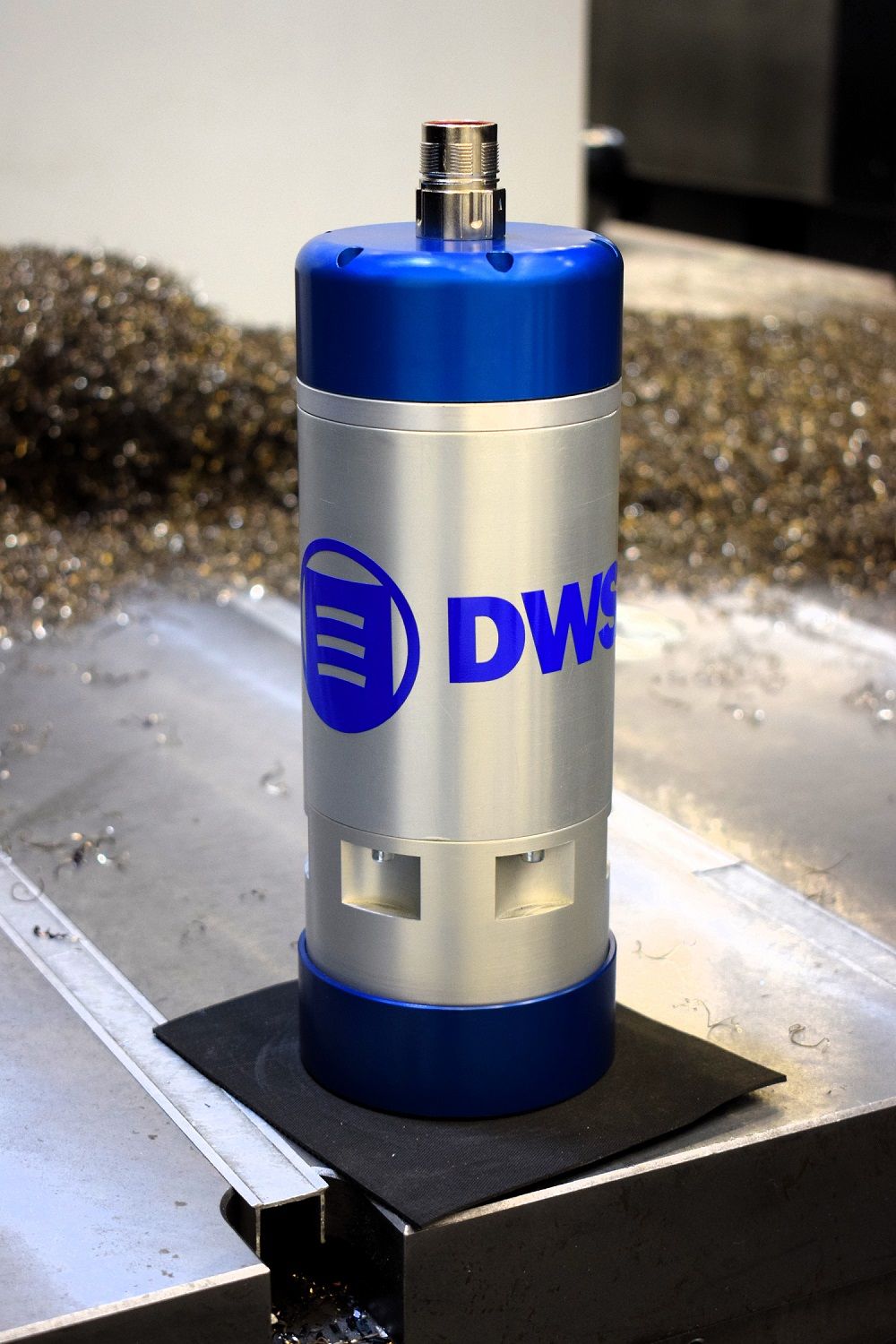
You can hear and feel it
"With the DAS+ and DWS systems, we have developed smart systems that enable us to counter chatter. Our users can produce more accurately, faster and more cost-efficiently thanks to these systems," Lindner said. During the 25th anniversary, Soraluce presented both systems live on an FSR gantry milling machine. A test stand allowed people to see whether the system was switched on or off. However, visual was completely unnecessary as visitors could hear and feel exactly when the anti-vibration system was switched on and when it was not.
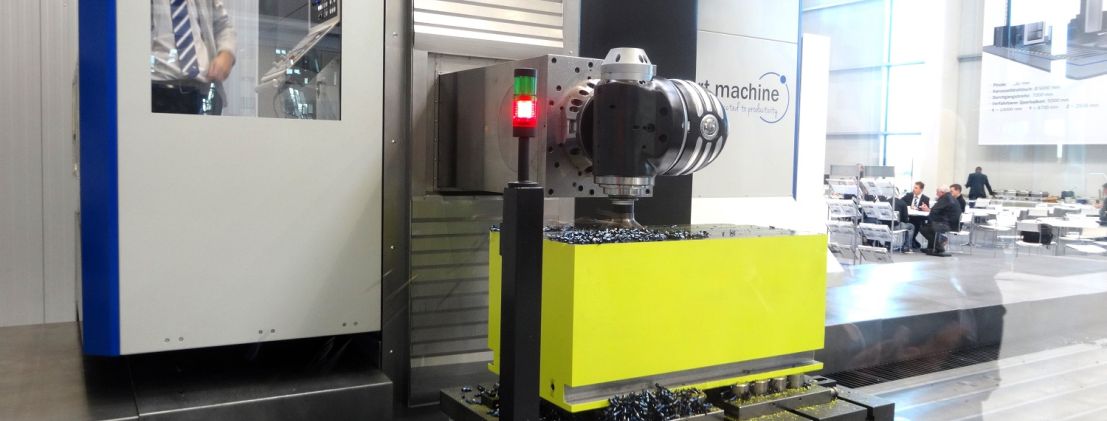