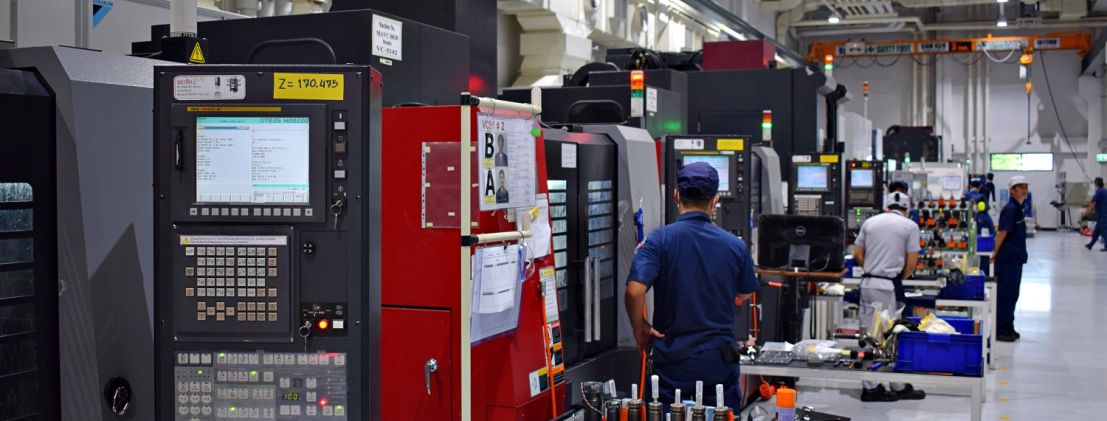
Take a Look Inside Sodick’s Factory in Thailand
Sodick, manufacturer of wire and zinc EDMs, gave our editor a glimpse into the machine builder's production facilities in Thailand. What is interesting is the modern machinery, the craftsmanship and the fact that they produce the complete machine in-house - from the machine bed, the hand-scraping of the guides to the electronics.
Anyone walking into Sodick's production plants in Thailand for the first time will notice that it consists of very modern machinery. This is partly because all machinery was replaced after a major flood in 2011. "You have to imagine that the water was 2 metres high. It was a disastrous sight to see the entire factory underwater. So all machines needed to be replaced," says Peter Capp, CEO of Sodick Europe. The flooding was also the reason for constructing a second factory on a site that lies 4 metres higher than factory number 1. " Sodick equipped both factories with high-quality machining centres. To make high-quality machines, you have to work with high-quality equipment." Sodick has now split production between the two factories. In the first plant, the wire EDMs are produced and in the newest plant, the zinc EDMs.
Ceramic components
The wire and zinc EDM machines are available in various types and sizes with which Sodick covers a wide range. In doing so, Sodick adheres to a selection of distinctive features to ensure the quality and accuracy of the EDM machines. Thus, all models are equipped with ceramic components, such as bearings, work tables, table pedestals and upper and lower arms. Due to the hardness of the ceramic, the parts must have the desired dimensions even before curing because post-machining is only possible with diamond tools. This is an expensive process and requires a lot of tools and machine tools. Post-machining is therefore kept to a minimum. The manufacturing process of the ceramic parts is as follows: The production of the ceramic parts is done in an in-house workshop where 'clay' is moulded into a shape using a mould. This mould is then briefly heated to partially harden the ceramic already. From then on, it can still be easily machined.
After machining, the ceramic part goes into a furnace at a temperature of 1,400 oC for another four to five days. During this process, the material acquires its extreme hardness. For the hardening process, Sodick has three kilns in operation. After the hardening process, small operations such as tap holes still need to be done. Due to the hardness of the ceramic, the holes cannot be tapped, so they glue in threaded bushings.
Making the ceramic parts is a time-consuming and expensive process compared to cast parts. The reason Sodick chose this material anyway has to do with its low coefficient of thermal expansion. In addition, ceramics conduct electricity little to no at all. Due to its poor electrical conductivity, all energy is converted into the spark. This allows for more precise and efficient cutting, which are advantages that outweigh the costs.
-
Ceramic parts in the wire and zinc EDMs include bearings, the table, table bases and upper and lower arms. Thanks to these ceramic parts, thermal expansion is prevented and all energy is converted into the spark. -
The ceramic parts are shaped using a mould. After the hardening process, the ceramics are extremely hard which makes it challenging for the machining process. (Pictures: Tim Wentink)
Linear motors
Besides the ceramic, linear motors are a feature that sets Sodick's machines apart. These motors are manufactured and tested in-house. The motor consists of a permanent magnet plate and a coil and features a cooling system where the cooling channels pass between the coils. Heat is thus removed directly at the source. Unlike ball screws, linear motors have fewer wear parts, couplings and other mechanical components. This has the advantage of fast, precise and vibration-free movement of the machine's axes. This results in better dimensional accuracy and surface roughness of the workpiece. The fast movements also enable better chip removal and, in the case of sinker EDM, less wear on the electrode. All this in turn shortens production times.
Gaining experience with automation
"You can slowly see automation joining Sodick's production plants in Thailand. This has everything to do with wages that are rising in low-wage countries. Take China, for example. Wages there have risen so explosively in recent years that it is almost no longer interesting to produce there. In Thailand, the increase is not as bad as yet, but here, too, wages will go up over time. That is why it is good to gain experience with automation now so that we can guarantee the same quality in the future without having to violate the competitive prices of our wire and zinc EDMs." In the sheet metal department, Sodick uses an automated bending cell with a Prima Power BCe Smart 2220 panel bending machine. The welding department employs several welding robots to automate simple welding jobs, and in the machining department, a robot loads and unloads both a wire EDM from Sodick and a five-axis machining centre from OKK. "At Sodick Thailand, a total of 175 machines are produced per month. It is fair to say then that the current form of automation is still in its infancy. Especially when you realise that 95% of the components are produced in-house. Then we are talking about circuit boards, cables, machine frames right down to the linear guide."
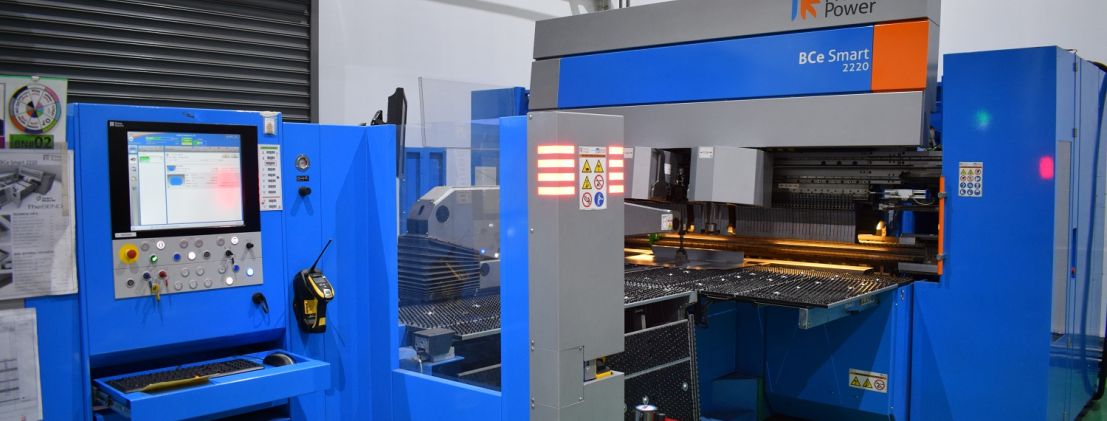
Responding quickly to changes
Because Sodick still benefits from low labour costs today, several employees are often responsible for one machining process. This has the advantage that every step in the production process can be thoroughly checked. According to Capp, this has a positive impact on the quality of the final product. And because all parts are produced in-house, Sodick is not dependent on suppliers with their uncertain delivery times and quality issues. In addition, it is possible to make changes quickly. The PCBs are a good example of the benefits of independence. "Developments in this field are going incredibly fast. The functionalities of a PCB are increasing rapidly. By producing them ourselves, we can quickly adapt new PCBs to our machines. In addition, every printed circuit board made belongs to a specific machine sold. The same applies to most parts. So no stock is produced. Another advantage is that we manually check and test each circuit board ourselves.