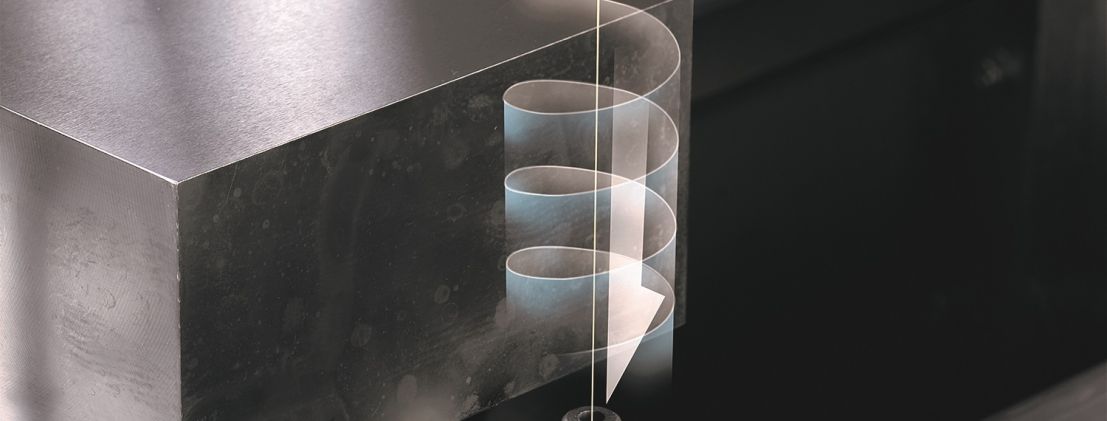
Sodick iGroove reduces wire consumption with rotating wire
Sodick's patented iGroove technology can reduce wire consumption by up to 30% during wire cutting. iGroove causes the wire to rotate around its axis during the downward motion. The wire's surface area is increased during the machining process, resulting in a more uniform wire wear. In addition, iGroove has a positive effect on the surface quality of the workpiece.
The patented iGroove technology is a standard feature on all Sodick ALC series wire EDMs. Sodick's new wire EDM rotation mechanism adds functionality, control and process reliability to the wire. The wire is rotated around its axis during the downward motion as opposed to the conventional EDM process. As a result, the workpieces are always machined from the top to the bottom with the fresh surface of the wire. The major advantage of iGroove is that wire consumption is greatly reduced. With the rising prices of raw materials, it is becoming increasingly interesting to reduce consumption. Consumption of wire accounts for half of the consumable costs of wire cutting. With iGroove, wire consumption for wire cutting can be reduced by up to 30%. This means that manufacturers can make substantial savings in production costs. At the same time, iGroove achieves higher surface quality and improved geometrical accuracy.
Ceramic wheel
The iGroove rotation mechanism is positioned in the lower arm of the Sodick wire EDM. To rotate the wire Sodick has developed a simple, yet ingenious solution. The rotation mechanism is equipped with a ceramic wheel with a hollowed-out ring in which the wire runs. The wheel is placed slightly off-center by means of a shaft. Because the wire is under tension, the wire tries to find the deepest point of the hollow rounding. This causes the wire to start rotating automatically and constantly. Because the ceramic wheel is positioned on a shaft, the wheel can move both to the left and to the right. Thus, the direction of rotation can be adjusted. The correct direction of rotation is automatically defined by the CNC control.
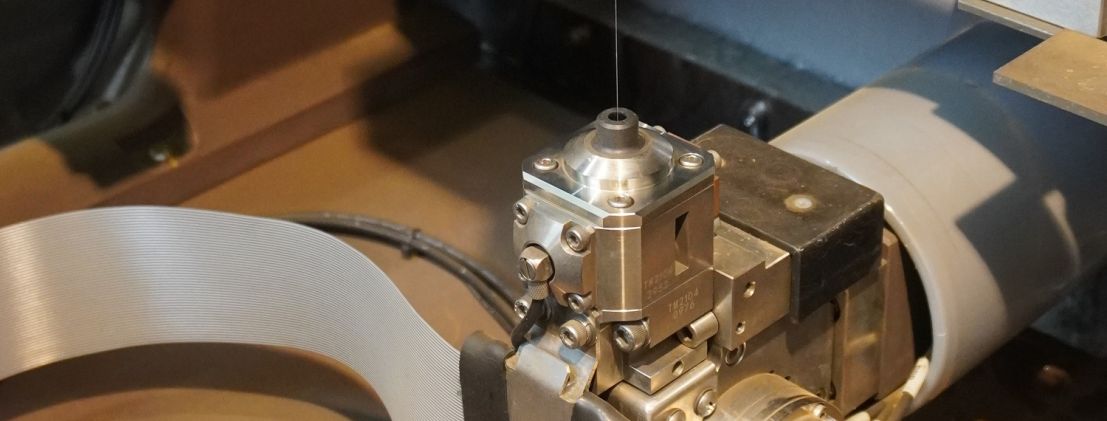
Homogeneous surface
In addition to reducing wire consumption, iGroove technology also improves surface quality and geometric accuracy. In conventional wire EDM, the wire wears out as it penetrates further into the material. Especially on thicker workpieces, this creates a surface that tapers. To compensate for the wire wear and still obtain a straight surface, the wire is always set at a slight angle. Another possibility is to increase the feed of the wire, but this can result in frequent breaking of the wire. By rotating the wire, the problem of tapering surfaces is immediately eliminated. Due to the rotation, the wire does not wear in one place, as the fresh surface of the wire is continuously used. Therefore, compensation is unnecessary, and a higher surface quality and dimensional accuracy is obtained. Under the microscope, it is very easy to see the difference between a workpiece punched with iGroove and one made by conventional wire EDM. With iGroove, it is clear that the surface is more homogeneous. That is, there are fewer black dots on the surface. In other words, it is smoother.
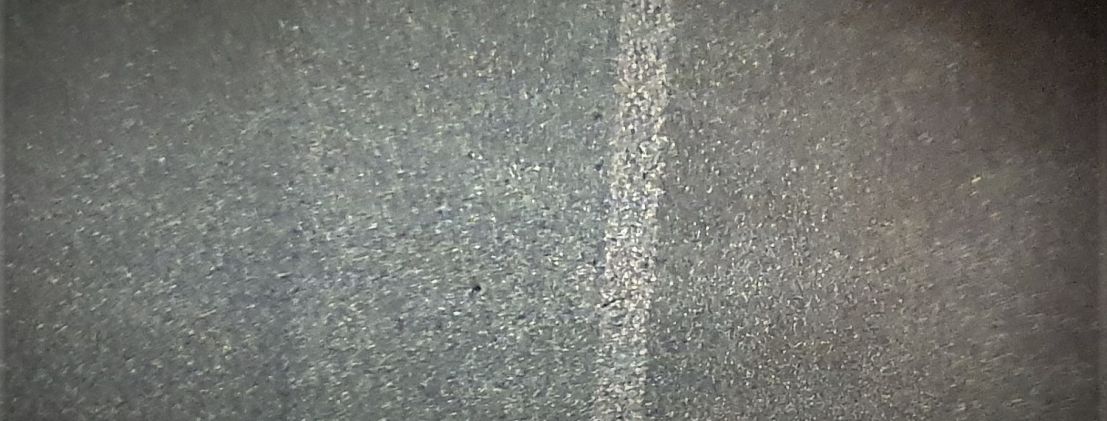
ALC Series
Wire EDM machines in the ALC series are among Sodick's high-end machines. The latest technologies are applied in these richly equipped machines. In addition to iGroove, the ALC series now features a newly designed larger capacity dielectric tank (the ALC400G tank has been increased from 675 liters to over 790 liters and the ALC600G tank has been increased from 850 liters to over 990 liters) and the number of filters has been increased from three to four to further increase filtration efficiency. Furthermore, the ALC series is equipped with the latest SPW control with convenient functions that optimally assist the operator and the TH COM function that uses sensors to minimize and compensate for the effect of temperature changes in the machine.