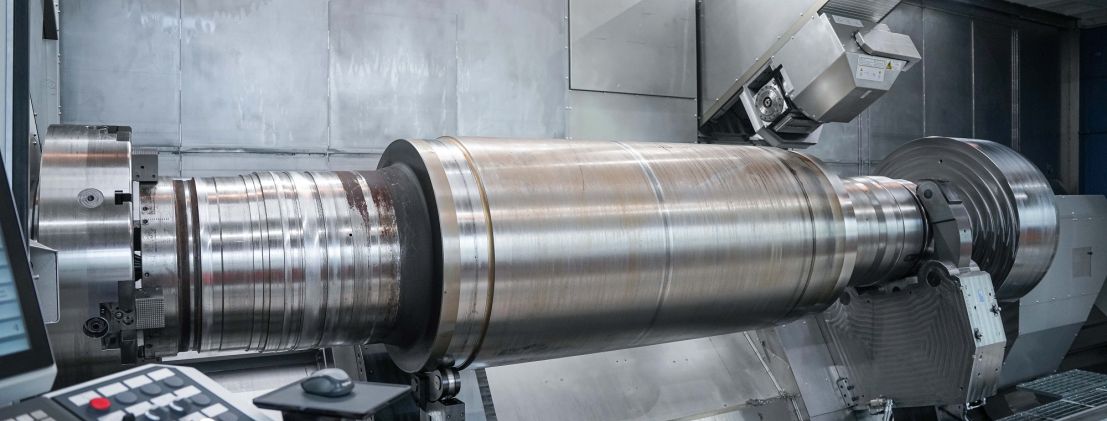
WFL puts extra effort in heavyweight machining
Higher, faster, further - as the saying goes, but now there’s “longer, wider, heavier”. Industrial requirements are constantly being pushed upwards. All of which means that WFL is entering exciting territory: heavyweight machining. The machining of large and very heavy components is often an extremely laborious undertaking that involves significant costs. Maximum process reliability and, above all, time savings in a component’s throughput time are the name of the game.
Combining all machining and measuring operations into a single Millturn complete machining centre from WFL massively increases the efficiency of manufacturing. The unique Millturn machine concept and turning-boring-milling unit with gearbox guarantees unparalleled chipping performance with the highest level of precision. An investment that pays dividends very quickly.
It all comes down to the right machine design
Special needs demand special measures. Gas and steam turbines or components for wind turbines, rollers, crankshafts and transmission parts in machine construction – WFL can now machine large and, above all, heavy parts with workpieces weighing up to 60 tonnes. What makes this extraordinary is that these types of heavy components can be machined in just a few clamping operations and in a single machine. A Millturn can even easily handle high-strength steel or HRSA (heat resistant super alloy) material. Special-purpose machines, such as those needed in multi-step production, are a thing of the past.
A Millturn eliminates the need for tedious changeover processes. Warpage-free and secure clamping is critical for premium quality standards and is based on the many years of experience of the WFL machining specialists. Large masses have a tendency to deform or change simply as a result of their net weight. The sag of a turbine shaft weighing 60 tonnes is so great that this needs to be taken into account when clamping the workpiece. This variable can be compensated with the correct design of the clamping device and clamping method. FEM calculation (finite element method) can be used to precisely determine how the workpiece can be correctly clamped and supported. In this case, WFL uses a rolling or hydrostatic steady rest depending on the characteristics of the workpiece. This ensures optimal machining quality and production. The accessibility to the machine with folding grate elements and tread plates also ensures the best possible ergonomics.
What’s more, the enclosed working area enables machining under high coolant pressures. The UHPC pump (Ultra High Pressure Coolant) can be used to reach up to 200 bar. This ensures an optimum tool life even with high machining parameters. The WFL M100 to M200 machine assemblies provide ideal conditions for creating a perfectly tailored machine for every customer requirement.
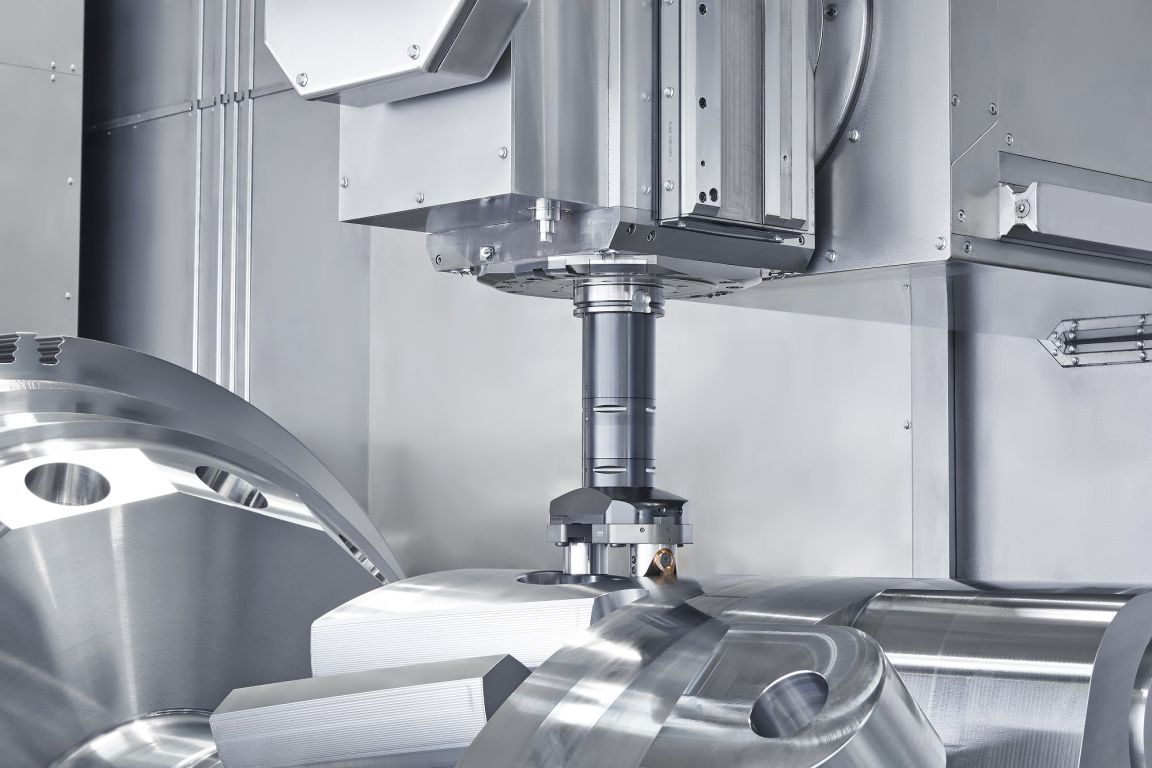
Process reliability through in-process measuring
Flexible measurement technologies perfectly support the user and once again clearly highlight the benefits of measuring components with large dimensions. The added time and safety as well as the elimination of measuring errors ensure maximum machining quality. WFL measuring cycles are carefully considered down to the last detail. For example, special calibration methods using the measuring probe and temperature compensation – which is particularly important when working with large diameters – allow the expansion of the material to be taken into account. The WFL measurement methods can even be used to produce a workpiece with maximum precision in adverse production conditions (e.g. external influences such as temperature). It is also possible to precisely measure the position of the workpiece in the working area. This is necessary to precisely manufacture extremely narrow shape and position tolerances, for example, fir tree profile slots or locating holes.
The CrashGuard Studio programming software also supports an effortless review of the machining program. This makes it possible to minimise production errors ahead of time.