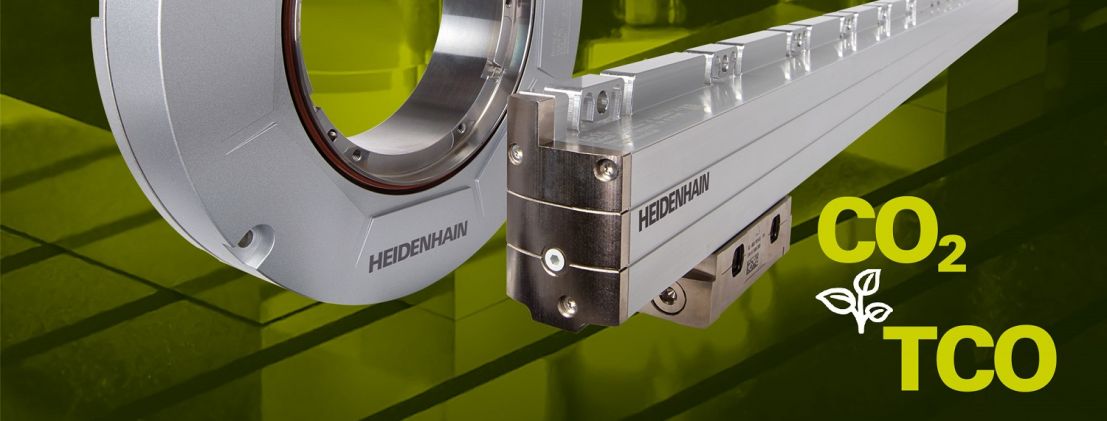
Heidenhain increases process reliability while reducing costs and CO2 footprint
Sustainability and system costs, also referred to as Total Cost of Ownership (TCO), are trending topics for machinists and machine manufacturers in the machining world. Heidenhain developed actual solutions to make machine tools more cost-efficient through better utilization of resources.
Today's manufacturing challenges include better machine utilization and achieving higher quality while at the same time producing more quickly. In order to reach these goals, machinists expect their machines to remove more material in less time but still achieve perfect results starting from the very first part. Encoders, touch probes and a tool breakage detector from Heidenhain open up expanded possibilities for maximum performance, process reliability and cost efficiency.
Heidenhain TD 110 tool breakage detector
Heidenhain recently presented the new TD 110 tool breakage detector for inspecting tools with diameters greater than 0.4 mm for damage. Using its inductive sensor, it detects changes in length starting from 2 mm without contact, directly in the work envelope while the spindle rotates at operational speed. Saving up to six seconds at each tool change results in significant time and cost benefits. The sturdy and compact TD 110 can be retrofitted in the work envelope of nearly any machine tool, in direct proximity of the table. The corresponding signals are transmitted to the control over the touch probe interface. Process reliability can be increased by the control issuing a message or triggering an NC stop or a user-specific reaction.
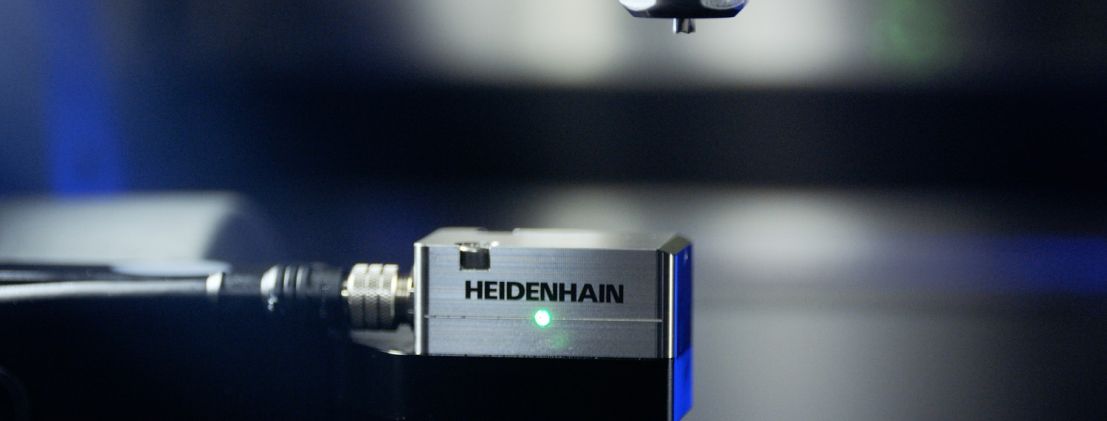
Heidenhain probes
Quicker and in-process setup and measurement of workpieces: this is made possible by the TS 460 workpiece touch probe from Heidenhain, with its very high measurement feed rates of up to 3000 mm/min. The time saved during probing, which can be as great as 30%, then becomes available to machinists as valuable productive time on the shop floor. The integrated flusher/blower unit of the TS 460 provides for high measurement accuracy since it cleans any chips from the probing surface that would otherwise falsify the measurement result. And, the probe can optionally be equipped with an effective anti-collision buffer that not only prevents expensive damage but also decouples the touch probe thermally. The TS 760 touch probe from Heidenhain enables workpiece measurement with particularly high 3D accuracy and very low probing forces. This makes it ideal for precision parts in moldmaking and highly sensitive workpieces. Its measurement feed rates of up to 1000 mm/min ensure a high level of performance.
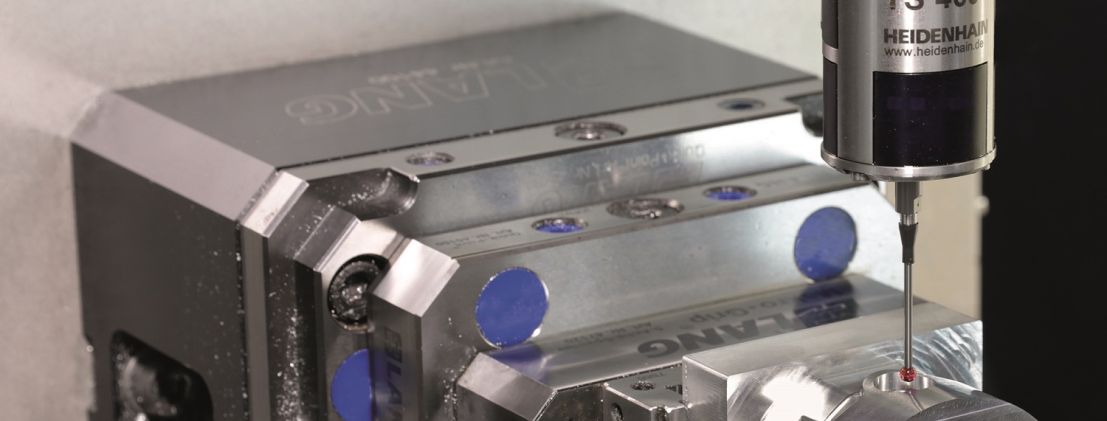
LC and RCN encoders from Heidenhain: 99% less CO2
In the area of machine components, Heidenhain is presenting at AMB the LC linear encoders and RCN angle encoders with optimized optics for crystal-clear sensing, even in the presence of liquid contamination and condensation. In many cases the encoders work just fine without any compressed air. This simplifies sealing-air needs, letting you enjoy the benefits of Closed Loop position measurement at significantly lower system costs. Also, omitting the sealing air reduces the machine's CO2 footprint by up to 99%.
New scale for long axes
The LB 383 C sealed linear encoder from Heidenhain is the new specialist for position measurement on machines with long axes. It is available in measuring lengths of up to 72 m. Thanks to its sturdy scanning unit, the new LB 383 C is particularly tolerant to contamination and at the same time very rigid in the measuring direction. This increases process reliability and permits significantly more powerful controller parameters, resulting in better machine performance. The LB 383 C also saves money, since its profiles are adapted to those of the LC 200 linear encoders. This not only reduces the amount of stock you need, but also obviates the need for special connecting pieces for compressed air.