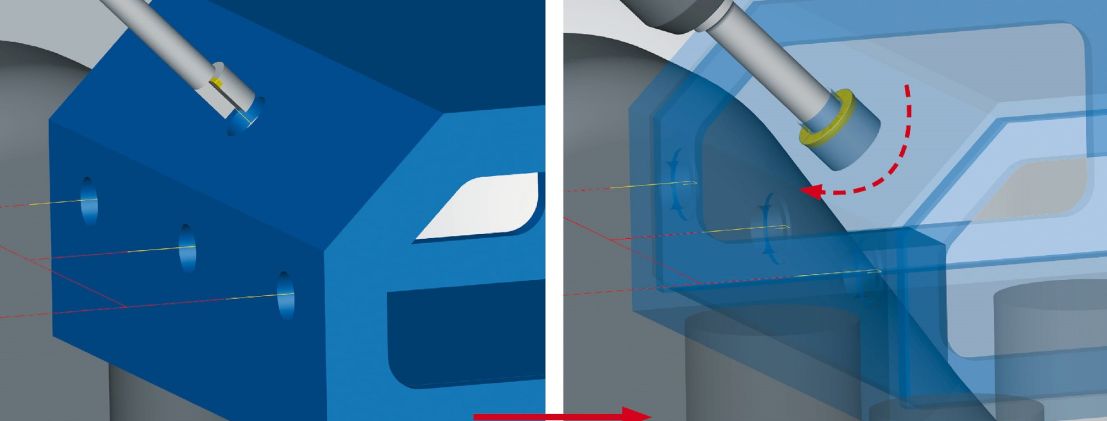
OPEN MIND Releases hyperMILL 2023 with very useful features
The shift to hyperMILL Release 2023 makes the CAD/CAM suite from OPEN MIND Technologies even more powerful and introduces innovative functions. Not only does the software load faster, but the calculation time of tool paths was able to be accelerated as well. In addition, the “General Transformation Pattern” function assures that you save time when machining recurring geometries. The new back boring machining strategy attains the highest degree of convenience and safety via its use of VIRTUAL Machining technology.
OPEN MIND has equipped hyperMILL 2023 with a machining strategy for back boring. Programming the controller for the tools used to deburr and mill a countersink on the inaccessible back side of a hole can now be done with incredible ease. Because collision control is carried out using a 3D model of the tool in the virtual machine, damage created when inserting and retracting tools is safely avoided. Watch the video below to get an impression of how easy and reliable the programming for a 2.5D back boring is with the new hyperMILL 2023 machining strategy for back boring.
Automatically transform any function
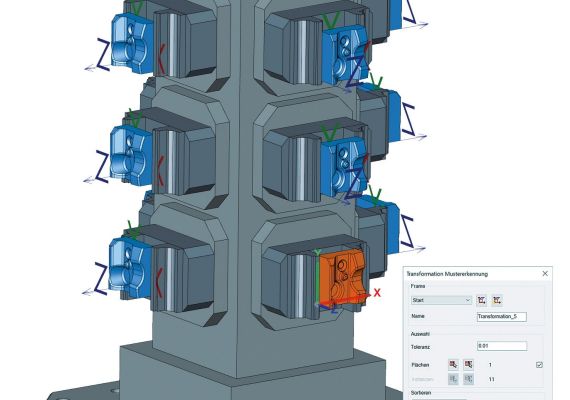
Up to now, standard features such as pockets and holes were able to be selected automatically. With the “General Transformation Pattern” function, OPEN MIND now makes it possible to select any reference geometry and search for that same reference in all other models – regardless of its spatial orientation. This creates a general transformation pattern including a frame at each reference feature. This makes it easy to program recurring shapes with a single click. The function is also suitable for multiple setups, for example.
5-axis strategy for more uniform surfaces
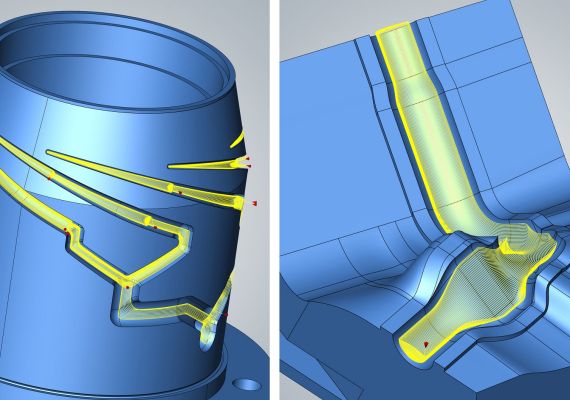
The “5-axis halfpipe finishing” strategy makes it incredibly convenient to program continuous toolpaths for grooves, tubes, and halfpipes with any cross-section along an arched guide curve. This is a great advantage for users, as previously, this machining operation may have had to be divided into several steps. This strategy opens a wide range of applications, for example, in molds and dies where the tool axis points in the demolding direction.
CAM in dialog
The example of back boring and its collision control based on a digital twin shows how hyperMILL VIRTUAL Machining is already playing a role in standard functions. Simulation technology based on real NC and machine data is becoming increasingly more important. OPEN MIND is driving the necessary communication between CAM system and machine controller forward. Currently hyperMILL VIRTUAL Machining supports controllers from HEIDENHAIN, SIEMENS, Mazak, FANUC, FIDIA, OKUMA, rödersTEC, D.ELECTRON, HURCO, and Haas. Others are to follow.
CAD, CAM and data
hyperMILL 2023 not only leverages advances in computing power and software engineering to increase performance, but it also streamlines processes. For example, the hyperMILL SIMULATION Center loads faster because it does not include unnecessary data for the calculation at hand. The optimized handling of data also proves to be an improvement in another area. hyperMILL now makes it possible to import individual components from assemblies. Users can now use filters to select individual components when importing assemblies from other design systems’ native data. This reduces loading times for large assemblies and eliminates the need to subsequently delete individual parts that are not required.
Another new feature in hyperCAD-S, the CAD part of the software suite tailored to CAM programmers’ needs, is the revision of the “Holes” function. A hole can be composed and parameterized from a library of hole fits, countersinks, and hole ends via a dialog, which includes a preview. To improve graphic clarity, threads can also be displayed if required.