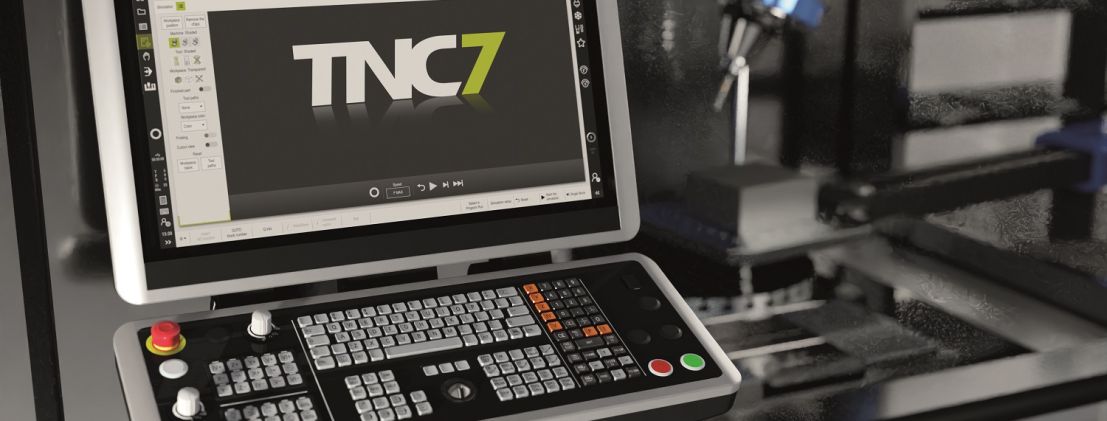
Heidenhain presents more manufacturing reliability, productivity and resource efficiency at AMB
Performance, CO2 footprint and digitalization are trending topics for users and machine manufacturers in the machining world. At AMB, Heidenhain will be presenting real-world solutions for the closely interrelated and often abstract requirements behind these terms. These solutions enable more chips in less time, perfect machining results from the first part onwards and highly automated processes with minimal idle time.
TNC7: the new CNC control from Heidenhain
The new TNC7 control will give machine-tool users and manufacturers exciting new ways to program and operate their machines. Operation is intuitive, task-focused and customizable thanks to numerous smart functions that take shop-centered manufacturing into a new dimension. And even more enhancements have been made for AMB 2022. AMB visitors can discover the new TNC7 at the Heidenhain booth and at the TNC Club booth in Hall 2, and also at the booths of the machine manufacturers Axa, Hedelius, Hermle, Matec and Samag.
TNC7: new graphical 6D workpiece setup
Along with providing graphical setup support for workholding equipment, the TNC7 now also delivers new probing cycles that enable fast graphically supported probing for any type of workpiece, including complex free-form parts. The TNC7 promotes process reliability by visualizing the entire production environment, including the fixtures, workpieces and the machine envelope. All of this data can be used during programming to create a realistic 3D simulation of the machining process. This can now be done without changing the operating mode.
TNC7: convenient programming
The new NC sequences of the TNC7 make it very easy to operate. The user can save any frequently used NC program sections to his Favorites and add them to new programs at any time. Users who work in low-light environments will be grateful for the new control’s new Dark mode, which improves touchscreen visibility for relaxed eyes.
User-friendly setup followed by efficient and reliable milling
The demo moderators at the Heidenhain booth will be showcasing how fast, easy and reliable it is to machine a workpiece on the TNC7, from setup to final deburring. The workpiece blank is aligned in no time thanks to graphical 6D setup support, even if it’s a complex, pre-machined workpiece. As a result, the entire machining environment is stored in the TNC7. Machining will be performed with Optimized Contour Milling (OCM) for next-generation trochoidal milling, including finishing and deburring cycles. OCM automatically calculates the best trochoidal milling strategy for any pocket or island, allowing a much wider range of parts to be machined with optimal cutting values for highly productive, reliable and tool-friendly milling. For even more process reliability, the TNC features process monitoring functionality. And throughout the demo, the StateMonitor software, a Heidenhain Digital Shop Floor solution, will be collecting and visualizing machine data.
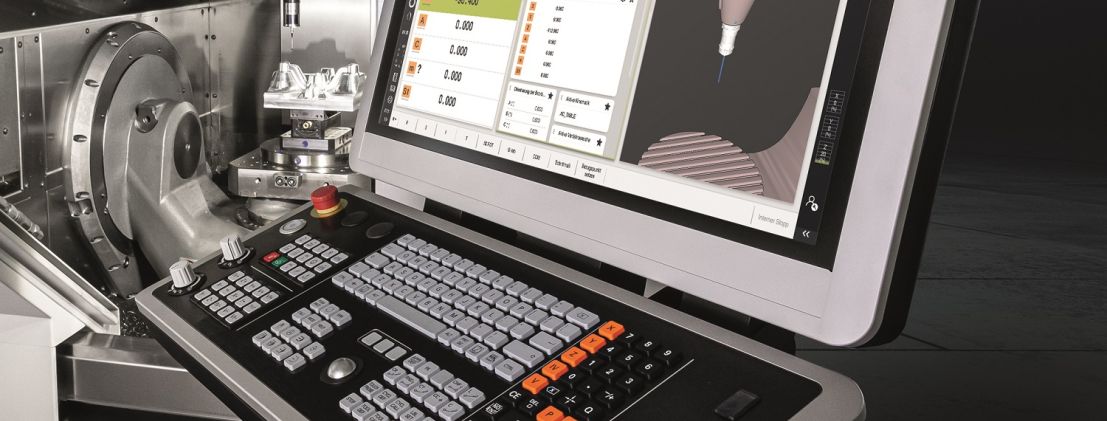
Software for the Digital Shop Floor: the new PlantMonitor
The Digital Shop Floor from Heidenhain offers practical solutions and competent services for full digitalization with 360° of insight into the shop floor. This includes the StateMonitor software for machine data collection, which enables real-time monitoring of the production status of CNC machine tools. For analyzing production data from multiple instances of StateMonitor, Heidenhain also offers the new PlantMonitor software, which can network machines located across different buildings or corporate sites.
Consultation and services for the Digital Shop Floor: the Digital Twin
The Digital Twin delivers greater manufacturing reliability. It is a realistic digital model of the machine for use on the Heidenhain programming station. The Digital Twin provides the kinematics, parameters and functions of the real machine on the shop floor, allowing them to be used for design, programming and simulation work in the office. This saves setup, simulation and debugging time at the machine while improving process reliability and productivity.
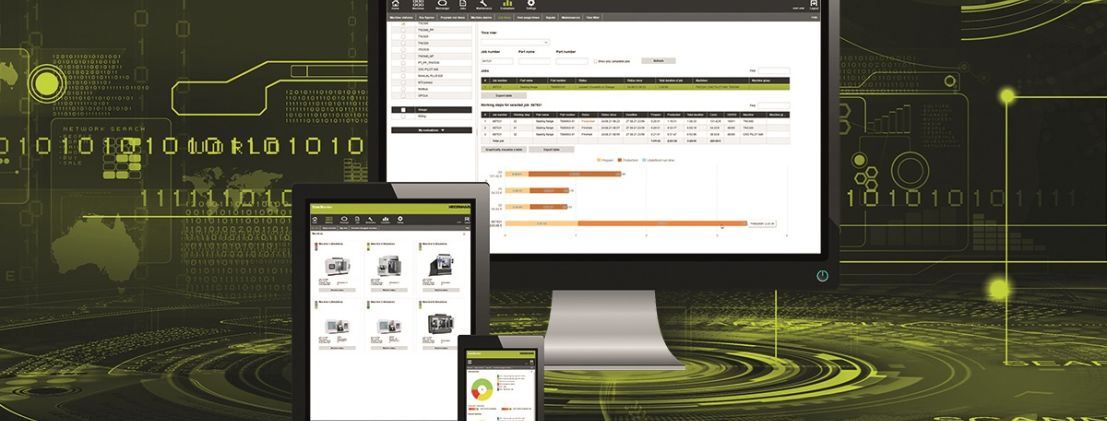
Reducing the machine’s CO2 footprint while increasing productivity
At AMB, Heidenhain will be presenting various solutions with which users and machine manufacturers can increase their resource efficiency. The TS 460 workpiece touch probe, for example, features very high probing feed rates of up to 3000 mm/min that can shorten the probing time by up to 30%, freeing up more time for production. In the realm of machine components, the LC linear encoders and RCN angle encoders with optimized optics see clearly even when liquid contamination and condensation are in play. In many situations, these encoders operate reliably without sealing air, thus simplifying the overall sealing air system for reduced system costs and a smaller CO2 footprint.