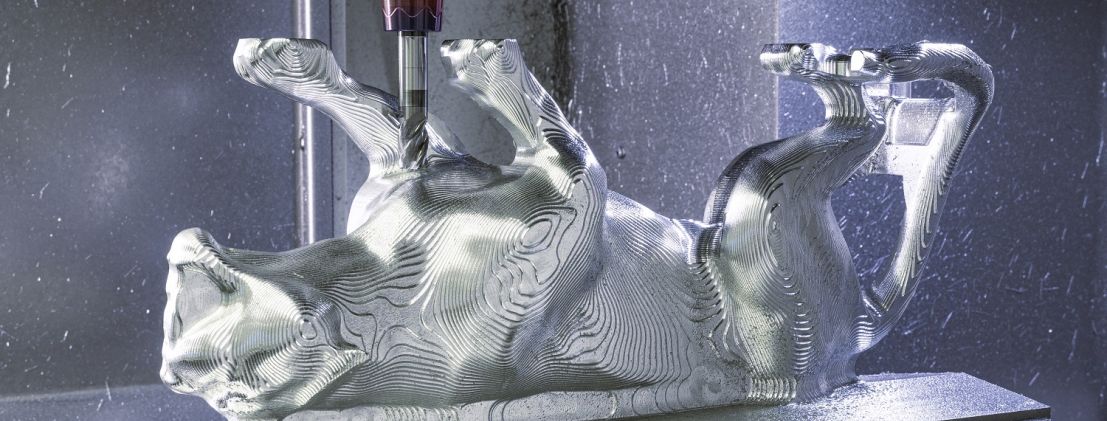
Haimer and Open Mind milled the Augsburger Panther
Haimer is a premium partner and supporter of the Augsburger Panther hockey team in the German Hockey League. The prestigious system supplier around the machine tool took this opportunity to demonstrate the performance capabilities of its tools and tool holders by creating a model panther. The CAM specialists at Open Mind took on the challenging programming task using their hyperMILL® software.
The ‘Augsburger Panther’, a member of the DEL (German Hockey League) are the most renowned ‘panthers’ around. Haimer GmbH, headquartered in Igenhausen, located just 30 minutes from Augsburg, is a proud fan and sponsor of the professional hockey team. The family company, a market leader that develops, manufactures and sells high-precision metal cutting products, came up with the idea of milling a panther out of aluminum at the Haimer application center. The panther is a masterful part showing that 5-axis-milling with HAIMER tool holders and solid carbide endmills can compete with the sport of hockey in terms of speed, power and dynamics.
Head of the Haimer application center Konstantin Brodowski sees even greater parallels: “Hockey isn’t just about speed and brute force. Each player must possess excellent technical skills and contribute them into a perfect team. Haimer works in very much the same way by incorporating the perfect synergy of its high-tech products with most modern machine tools and the best in class CAD/CAM software.”
One-two between machining and programming experts
In their search for ‘teammates’ for the panther project, Haimer turned to Open Mind, a longstanding partner and CAD/CAM manufacturer based in Wessling, Germany. Their hyperMILL CAM system is the leader in 5-axis machining according to many players within the machining industry, making Open Mind the perfect match when it comes to programming completely freely shaped contours. They showed no hesitation in answering ‘yes’ to the question of whether an application engineer was up for the job of programming the unusual showpiece and joining us on the milling project. Manager of Global Engineering Services Christian Neuner explains: “A model such as this one is a great opportunity to put the versatility and flexibility of our software to the test. In many ways, the panther analogy very much applies to us. hyperMILL® has lots of functions that allow CAM users to truly put a machine’s power to the ultimate test to achieve the desired goal.”
That’s why Jakob Nordmann, application engineer at Open Mind, set up camp in Igenhausen, Germany for a few weeks, where he teamed up with Haimer applications engineer Daniel Swoboda to set up the perfect programming and machining infrastructure. As for the milling machine, they chose the linear, 5-axis DMG Mori HSC70 machining center located in the Haimer Application Center, which is ideally suited for precise aluminum machining and excellent surface finish.
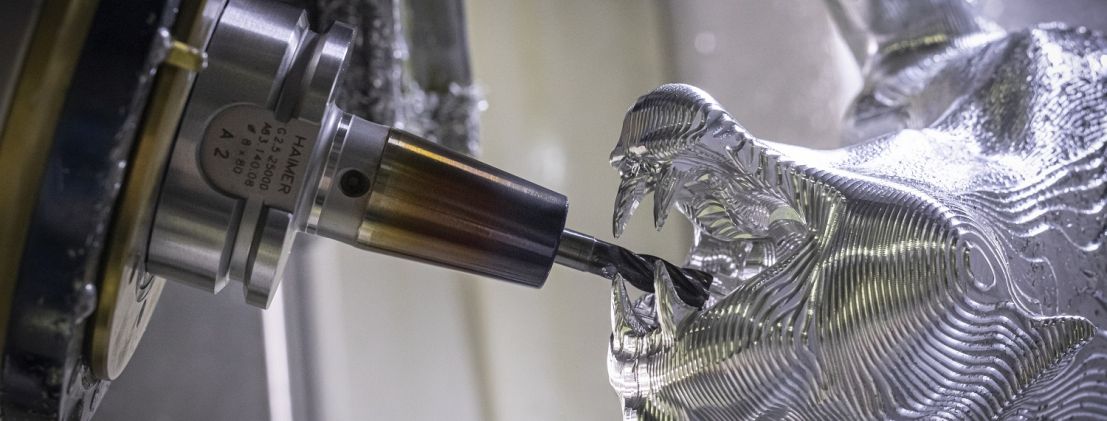
Tool solutions for any challenge
Machining of the panther’s head proved especially challenging, in particular the extremely detailed mouth and teeth. The long and thin shape of the delicate tail section was equally difficult to master, as it was extremely sensitive to vibration. What’s more, access to many of the parts was extremely difficult, which is why those responsible decided to make the statue in two set-ups, for which a Lang macro grip 5-axis clamp was used as a fixture.
The limited accessibility also impacted the type of tools selected. Though already using the shortest tools possible, the application specialists still required tool lengths up to 278 mm. That’s why Daniel Swoboda opted to use the modular Haimer Duo-Lock tools for the roughing applications. This system consists of carbide tool heads that are connected to different extensions via an extremely stable interface. He specifically chose a four-flute cutter with a corner radius from the Duo-Lock Haimer MILL Alu series. These fine balanced tools feature superior length repeatability. They offer a degree of sharpness with just the perfect balance in terms of abrasiveness and resistance. “We clamped the coated, cylindrical extensions of the Duo Lock tools using the Haimer Power Shrink Chucks,” says Daniel Swoboda. “This allowed us to achieve significantly more rigid clamping and less vibration than we would have had if we used standard tool holders. This, in turn, allowed us to achieve greater depth of cut and a higher metal removal rate.”
For the finishing process, we went with the full radius version of the solid carbide endmill from the Haimer Mill Alu series because of its micro-geometrical properties, which are designed for smoothness and top surface quality. Those involved in this project took the very limited space conditions into account when clamping with the extra slim and low-vibration Haimer Power Mini Shrink holders.
Open Mind colleague Jakob Nordmann adds: “What I found most helpful for me while working on this project was the fact that all the Haimer holders and tools were also available in the form of DXF and STP files. The models are available on the Haimer home page for easy download. It takes just three clicks of the mouse in our hyperMILL Toolbuilder to enter them into the database. After this, they are immediately ready for programming and simulation.”
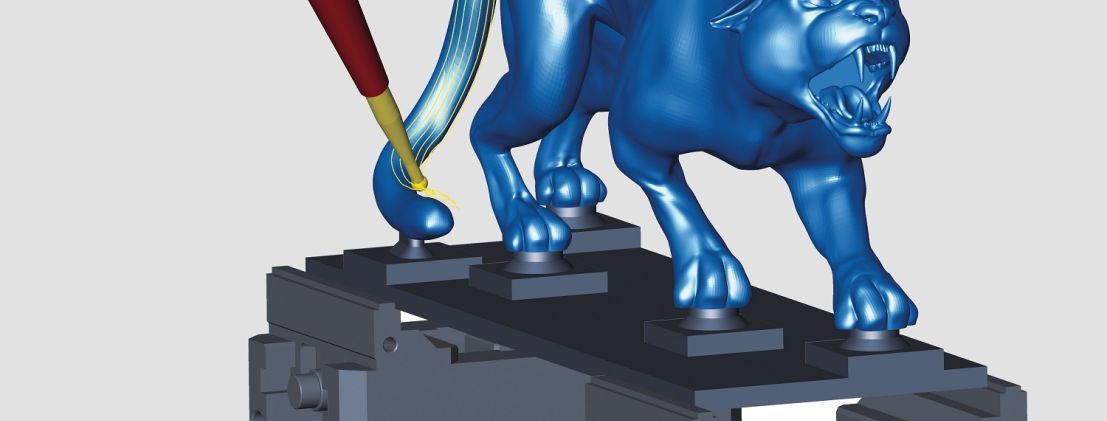
Helpful tips: CAD for CAM and simulation
Creating a visually appealing model demanded careful and excellent programming. The first core issue we encountered: The panther was presented as an STL data model, hyperMILL specialist Jakob Nordmann explains: “Since conversion into a surface model would have taken too long, we decided to mill on the STL network, but with line-by-line milling of 1mm in order to ensure that the faceted structure is not visible.”
“For especially detailed areas, like the mouth and tail section or with the creases of the joints, we generated additional surfaces that can be combined with the STL network in hyperMILL.” For this, Nordmann used hyperCAD-S, the ‘CAD for CAM’ system specially designed by Open Mind to help meet all the needs of programmers.
Since the limited space required different tilts of the tool, his focus was on maintaining the exact line spacing and a seamless transition without any visible gaps. “I used the ‘edit toolpath’ command for this, Nordmann reveals. “This allowed me to determine the entire toolpath and divide it into sections, which then made it possible to edit in various tilts using different tools. This saved me a lot of time.”
Equally imperative when it came to milling the panther was the hyperMILL® Virtual Machining Center, a process-safe NC simulation solution where virtual machine movements fully mimic real movements and ensure reliable collision detection.
It took the team approximately three intensive weeks to complete the first free-standing panther. Anyone who is interested can admire the model at both the Haimer and Open Mind booth at future exhibitions. And, of course, the Augsburger Panther will also be receiving a model for the entrance area of the stadium as well as the dressing room tunnel so that the players always have the right motivation when they hit the ice.
-
The panther, which is about 500mm in length, was machined from an aluminum block in just under 13 hours. -
The finish was done using the full radius version of solid carbide endmills from the Haimer MILL Alu series, which were clamped in the extra slim yet low-vibration Haimer Power Mini Shrink holders.