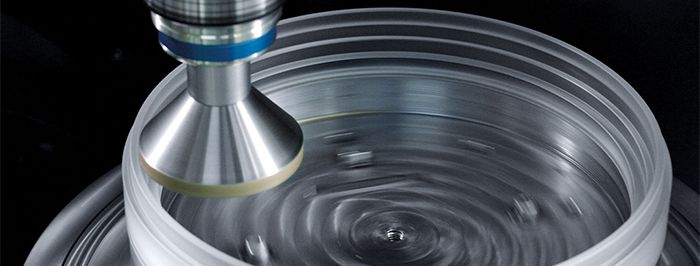
DMG MORI gears up for the future of semiconductor manufacturing
The semiconductor industry is entering an era of extreme precision and rapid technological change. As chip architectures shrink and application demands rise, equipment manufacturers are under pressure to deliver performance, purity, and reliability at increasingly microscopic scales. DMG MORI, a global provider of high-precision machine tools, is responding to these challenges with advanced manufacturing solutions tailored for semiconductor production.
One of the most critical steps in chip production is lithography, where intricate circuit patterns are projected onto silicon wafers. To support this, DMG MORI provides high-precision machining centers designed to manufacture components used in lithography systems—such as those supplied by ASML Holding. These systems require extremely stable mechanical structures, precise guideways, and vibration-dampened drive systems. Through decades of continuous development, DMG MORI has refined its equipment to ensure process reliability and dimensional accuracy across demanding applications.
Ensuring reliability across the entire wafer production chain
Each silicon wafer—typically 200 mm in diameter—can hold hundreds to thousands of individual chips. Applying complex circuit structures to these tiny areas requires an environment free from contaminants and mechanical deviations. To meet this need, DMG MORI machines are engineered for ultra-precise production of components that form part of lithography equipment. This includes process steps ranging from material application to fluid film control, exposure, and development. The company’s ultrasonic machining technologies are central to meeting these demands. They enable tolerances in the micrometer range and ensure cleanliness standards suitable for semiconductor applications.
The cleanONE concept: mitigating contamination risks
A critical element in maintaining purity during component manufacturing is the cleanONE process developed by DMG MORI. This multi-stage protocol governs the use of certified cooling lubricants and mandates the replacement of potential contaminant sources—such as zinc, copper, or brass—with stainless steel components. The objective is to eliminate the release of particles into the cooling circuit, thus preventing contamination at every stage of production. Rigorous analysis confirms compliance with particle-free requirements, providing a verifiable advantage to semiconductor manufacturers.
ULTRASONIC technology: high-speed precision for hard-to-machine materials
The semiconductor sector demands rapid, high-precision machining of challenging materials like silicon carbide, aluminum, titanium, and glass ceramics. DMG MORI addresses this with a range of platforms—monoBLOCK, H monoBLOCK, duoBLOCK, and large-format Gantry/XXL systems—each engineered for stiffness, power, and speed. Bernd Dötterl, Head of the Semiconductor Excellence Center at DMG MORI, explains: “To machine these often high-strength materials with precision, machines must be extremely rigid and powerful, enabling high torque, speed, and feed rates. Only then can axes be moved quickly and accurately to ensure the desired production quality.” To further enhance productivity, DMG MORI emphasizes process integration—combining multiple machining steps within a single setup. This not only improves efficiency but is essential for meeting the industry's nanometer-scale accuracy requirements.
Scaling up for a miniaturized world
Despite the shrinking size of semiconductors—now reaching dimensions as small as 2 nanometers—the complexity of production systems is growing. Modern cars can contain over a thousand chips, while demand for embedded semiconductors in consumer electronics and appliances continues to climb. This has implications across the entire supply chain, from optics and packaging to the machine tools that shape every component. “Smaller chips mean larger systems,” says Dötterl. “We are ready for this future thanks to our extensive experience with large-scale, high-precision machinery.”
As the semiconductor industry continues its evolution, DMG MORI’s approach—focused on cleanliness, integration, and accuracy—positions it as a crucial technology partner for chip production in an increasingly miniaturized and complex world.