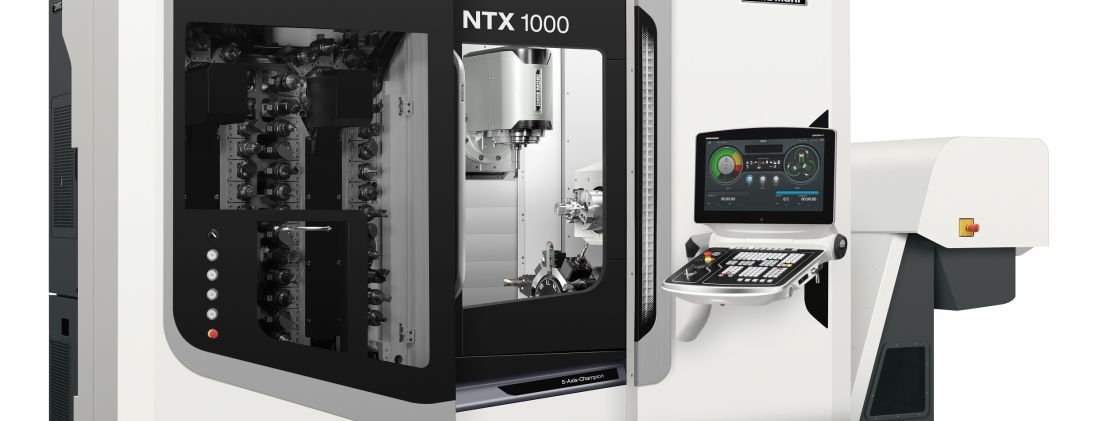
DMG MORI renewed the NTX 1000 Mill Turn Center
The existing NTX 1000 is a compact integrated mill turn center that is capable of high-efficiency machining of complex-shaped workpieces with a perfect combination of turning and milling. The machine has received as many as approximately 500 orders since its release in 2010. The second-generation NTX 1000 is jointly developed with customers’ requests and needs toward the existing model reflected on every detail to achieve high reliability. The model is equipped with an operating system CELOS that uses a touch panel operation, which is a game changer for every machine tool in use today, and the curvy and rounded appearance overturns a conventional image of factory equipment. The second-generation machine has gotten the cutting-edge technologies required for automation, high precision and energy saving.
Small footprint
The renewed DMG MORI NTX 1000 requires less floor space than the existing machine which is already compact. The footprint is the smallest in its class of 10.4 m2. Despite its space-saving design, the X-axis travel is extended from 380 mm to 455 mm, and the Z-axis travel 460 mm to 800 mm, allowing the widest machining area in its class. The small footprint and wide machining area drastically improve productivity per unit area. The max. indexing diameter of the Turret 2 is enlarged to 680 mm, while the optimal design ensures a sufficient machining space. This enables simultaneous machining with the tool spindle and the Turret 2.\ The compact tool spindle and the Turret 2 which allows a flexible tool layout are able to avoid interference with tools and fixtures.
The cooling oil circulation structure (patent pending), in which cooling oil circulates inside the ball screw, ball nut and spindle, minimizes heat generation and has strong resistance to environmental temperature variation, ensuring stable, high-precision machining for long hours. Besides, the Turret 2 is equipped with BMT® (Built-in Motor Turret) that minimizes heat generation and vibration, which improves the level of milling precision and performance and drastically increases production capacity.
Automation friendly design
The machine is flexibly compatible with automation with the bar feeder specification and the in-machine traveling robot specification. As to the newly developed in-machine traveling robot specification, a robot is installed inside the machine to handle workpieces. The operator can manipulate the robot and check the operation status using the NC unit (Siemens spec. only) as if it were a part of machine operation.
Energy-efficient parts
In an effort to reduce environmental burden and running costs, DMG MORI uses energy-efficient parts such as LED lighting, and cut down lubrication oil consumption by 90% through the optimization of various machine functions. We also work on machine design which enables efficient machine operation aiming at effective energy-saving improvements. The second-generation NTX 1000 has achieved shorter cycle times by optimizing M codes and employing the new function to reduce canned cycles. We have enhanced energy-saving functions used during automatic operation, such as the function to adjust the coolant discharge rate according to machining load and the function to shut off the power of channels in standby mode.