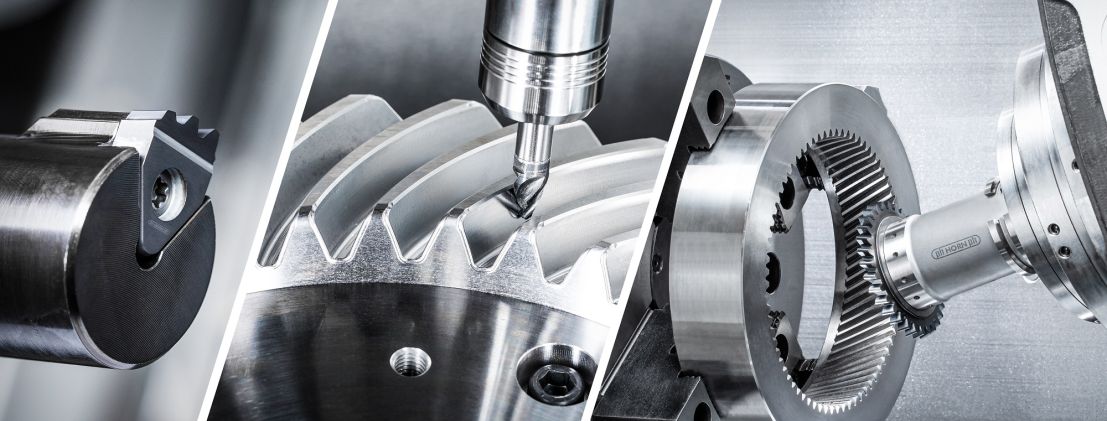
Paul Horn and DMG MORI work together on gears
Gear broaching, gear milling and gear skiving - otherwise known as the technology cycles: gearBROACHING, gearMILL, gearSKIVING. Paul Horn and DMG MORI have launched a campaign covering these three core areas in gear cutting to demonstrate the high performance of the solutions that have been jointly developed through a combination of machine, cycle and tool. A major advantage is that many existing machines can be adapted to the individual processes.
The exclusive DMG MORI technology cycles assist shop floor programming for increasing productivity and safety as well as for expanding machine capability. The advantages are clear: up to 60 percent faster programming, error minimization through conversational programming, new technologies (gear cutting) and the technology know-how stored in the application software.
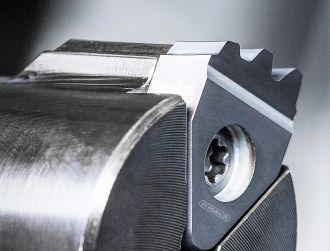
The exclusive DMG MORI technology cycles assist shop floor programming for increasing productivity and safety as well as for expanding machine capability. The advantages are clear: up to 60 percent faster programming, error minimisation through conversational programming, new technologies (gear cutting) and the technology know-how stored in the application software.
Standard or special tools
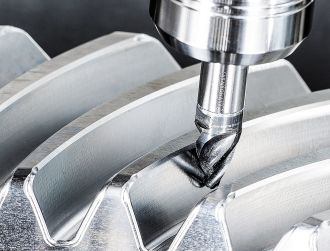
As far as the tool is concerned, Horn's standard or customer-specific special tools may be used, depending on the process and application. When skiving internal and external gears, sizes up to module 8 are possible in gear quality up to ≥ 7. Gear milling with standard tools up to module 3 achieves a gear quality of ≥ 5. Gear quality of ≥ 9 can be achieved when gear broaching internal and external gears up to module 4.
Events and trade fairs
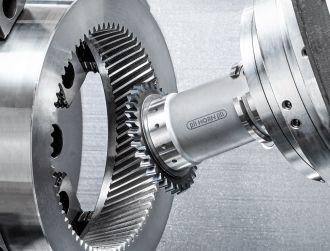
To provide practical proof of these results, there will be numerous events and trade fairs in 2022 that will focus on the joint gear cutting processes developed as part of DMQP (DMG MORI Qualified Products). The first event was the DMG MORI Open House in Pfronten in May.