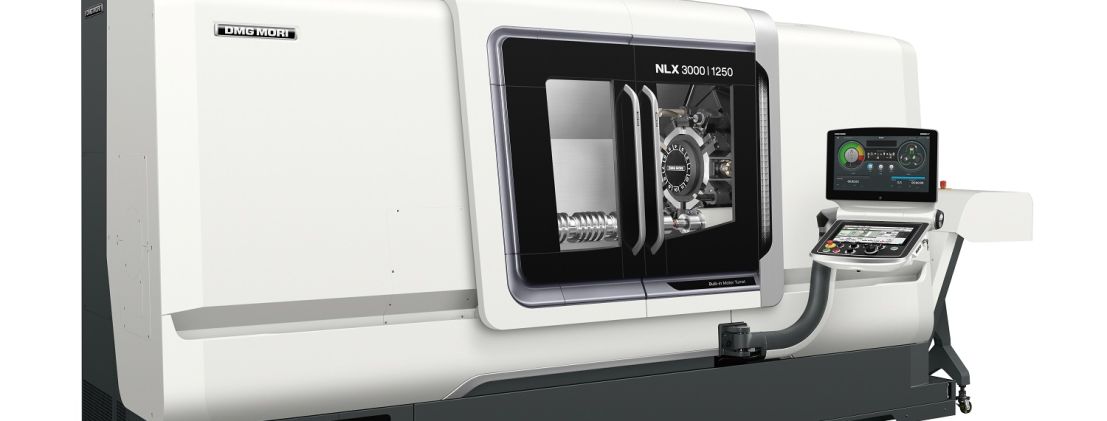
DMG MORI presents five new NLX machiningcenters
The NLX series is a line of high-rigidity, high-precision CNC lathes consisting of 9 models with 30 specification variations. Having an extensive lineup from a two-axis lathe up to a lathe capable of 6-sided machining with the Spindle 2 and Y-axis, the NLX series provides the ideal solution for every customer’s machining requirements. At JIMTOF2014, DMG MORI will be showcasing the five newest NLX models varying in specifications: NLX 1500SY|500, NLX 2000Y|500, NLX 2500|500, NLX 2500SY|700 and NLX 3000Y|1250. All of which come with the new DMG MORI design and CELOS.
Ever since its launch in 2010, the NLX series has been DMG MORI’s best-selling series with more than 3,000 units sold worldwide. The NLX lathes employ the coolant circulation system in their beds to keep thermal displacement to a minimum and the flat guides on all axes to ensure stable turning.
Built-in Motor Turret
The NLX machines are equipped with the BMT (Built-in Motor Turret) to minimize heat generation and vibration, providing greater cutting performance and accuracy. The BMT itself has also been improved to achieve a maximum rotational speed of 10,000 min-1. The significant increase in speed from the 6,000 min-1 on the previous model enables the machines to maximize performance in aluminum cutting and small-diameter drilling. Furthermore, the improved BMT has solved the issues of vibration and heat generation that can arise during high-speed machining at 10,000 min-1. Vibration in the turret was reduced to less than one-third and the turret temperature increased to less than one-tenth of those of a gear-driven turret, resulting in a substantial improvement in accuracy. The BMT is by far the best turret in its class, enabling the lathes to have the same machining capability and accuracy as machining centers. The TRIFIX high-precision, high-rigidity, VDI quick-change turret is also available as an option (for NLX1500, 2000, 2500). With holder-mounting repeatability of 6 µm or better, the highly precise quick-change turret ensures much faster tool changes, contributing to a reduction in setup times.
Reduce environmental burden
Energy-efficient components such as LED lighting are used to reduce environmental burden and running costs. DMG MORI has also focused on improving operating efficiency, and reducing machine power consumption through the optimization of M codes and the use of functions to adjust coolant supply volume according to the machining load. These energy-saving functions, coupled with the improved machine design for faster mechanisms, enabled CELOS-equipped models to successfully reduce cycle times and power consumption. For example, when compared with a machine that has been used for 15 years or longer and is about to reach its replacement time, a CELOS-equipped model can cut down the annual energy consumption by approximately 45%.* The visualized energy-saving effects can be checked on CELOS.