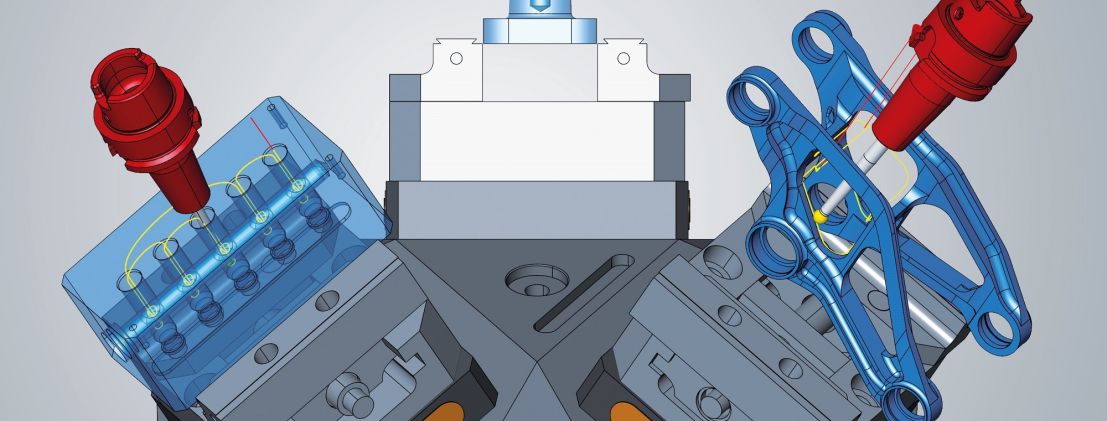
OPEN MIND Releases hyperMILL 2025 Packed with New Features
OPEN MIND has introduced the 2025 version of its hyperMILL CAD/CAM suite. A key innovation in this release is an automatic deburring function designed for ease of use. On the CAD side, the update includes a new tessellation algorithm and a simplified element display, both aimed at improving performance and accelerating model processing.
Deburred edges and holes are not only crucial from a functional point of view, but also contribute significantly to the quality and value of the end product. hyperMILL 2025 offers a package with three new strategies for deburring directly on the machine. Users can deburr a wide variety of component geometries quickly and reliably. 5-axis Deburring is an effective solution for breaking the sharp edges of a component. Once the edges have been selected, the strategy calculates all toolpaths automatically. The strategy supports both a 3-axis and a 5-axis mode, in which machining is indexed where possible. The same applies to the strategy for deburring edges on holes and intersecting holes. Another strategy in this context is hole brushing, in which a special brushing tool deburrs cross holes, threads, or other features or improves the surface quality. The machining process is divided into different phases, and the machining parameters such as spindle, feedrate, speed, coolant, and dwell time can be defined for each phase.
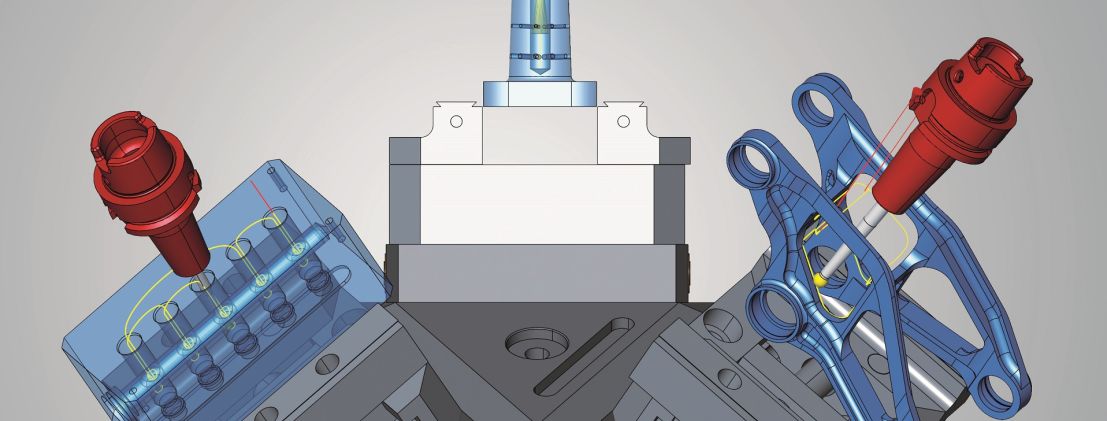
5-axis automatic mode
The new 5-axis algorithm in hyperMILL calculates an optimum machining sequence of simultaneous and indexed tool movements, thanks to the pre-analysis of the entire toolpath. Indexed processing (which is preferred, as it runs faster) and simultaneous processing phases are selected automatically. The new 5-axis ISO Machining strategy allows surfaces to be machined according to the course of the ISO lines (U and V). A new high-precision surface mode with a homogeneous point distribution can be used here, in addition to feed adjustment for curvatures and 3D radius correction. This is also available in 5-axis profile finishing for surface and cavity machining. Both strategies are adaptations of proven 3D techniques.
Milling and turning
The pocket milling algorithm has been redeveloped for 3D-optimized roughing in order to achieve greater efficiency during roughing, especially when machining large lateral infeeds. You can better control toolpath rounding by defining the contour radius and the path radius separately. This is important for the new “Axis Parallel mode” machining strategy when machining flat surfaces. There are also new functions for turning. It is now possible to use the 3D model to create a V-sketch for turning contours very quickly and easily. You can use the V-sketch to define the dimensions and tolerances. Based on these values, the turning contour can be moved to the center of the tolerance.
The new automatic stock chain provides security, especially when switching between turning and milling operations or other projects with a large number of process steps. hyperMILL creates all stock automatically and in the correct sequence, even if the job sequence has been changed.
-
5-axis machining of ISO surfaces with increased surface quality and programming support through intelligent algorithms. -
The improved version of 5-axis profile finishing incorporates many familiar and innovative functions from 3D profile finishing. -
New handling of stock: hyperMILL creates all stock automatically and in the correct sequence across all processing modes.
hyperMILL VIRTUAL Machining
Lathes with a turret and a main spindle are mapped as a digital twin for hyperMILL VIRTUAL Machining. Turning in hyperMILL now supports FANUC and Mitsubishi controls as well as Siemens controls. Another new feature is job calculation with the virtual machine. This means that the machine model is available to hyperMILL during toolpath calculation. Collision control and avoidance are carried out taking machine geometry and limits into account. It results in more precise, optimized toolpaths, especially in tight spaces.
hyperMILL and Hummingbird-MES
The integration between hyperMILL and Hummingbird-MES is also progressing, for example, in the area of tool management. The release of the new version means that users can benefit from an even deeper integration of both systems. Tool data from the hyperMILL tool database can now be managed consistently and conveniently across systems. Tools can be exported directly from hyperMILL, including all relevant technology parameters. These tools are automatically locked in hyperMILL as soon as they are transferred to Hummingbird in order to avoid inconsistent tool data. This creates a consistent, reliable, and efficient process for tool management – from the CAM system to Hummingbird and other systems such as a tool presetter.
-
Job calculation with a virtual machine: More precise and optimized toolpaths, especially in tight spaces or when the machine head is working close to the component or at the machine’s limits. -
hyperMILL VIRTUAL Machining technology now provides support for lathes with a turret and a main spindle in conjunction with FANUC and Mitsubishi controls.