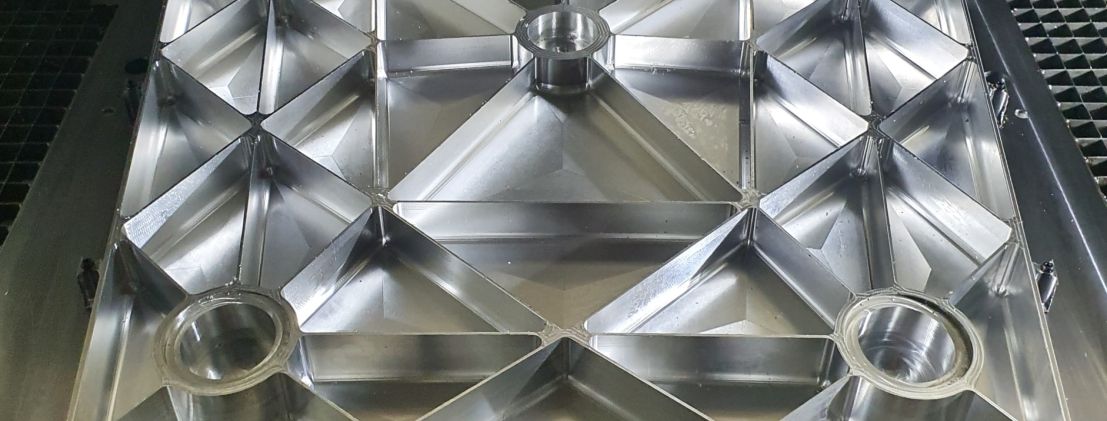
Sheeram Aerospace Takes-off With hyperMILL from OPEN MIND
Established in December 2017, Sheeram Aerospace & Defence LLP has grown at a phenomenal pace since its inception with significant investment in the very latest technology. With a multitude of 3 to 5-axis machining centres and associated technologies, the company has already expanded its facilities to more than 34,000sq/ft to support its high-profile client list. To streamline productivity and enable the company to manufacture a diverse range of components, the company has invested in the industry-leading hyperMILL CAM solution from OPEN MIND Technologies.
Located on the outskirts of Rajkot in the Gujarat province of India, Sheeram Aerospace & Defence LLP specialises in the production of wing structures, engine components and jigs and fixtures for the aerospace industry as well as serving customers in the space, renewable energy, die and mould, transport, oil and gas and medical industry sectors. To succeed in such demanding sectors, the company has a string of OEM supplier accreditations and is currently supplying many of the world’s leading aerospace primes. With dedicated machining, assembly and measurement departments, high-end machine tools and inspection equipment, the 50-employee business needed an equally high-end CAM system – this is where OPEN MIND came into the equation.
Where it all began
Most manufacturing companies start with general subcontract work on a couple of turning and machining centres and build their business gradually, not Sheeram Aerospace. Whilst the company may have started with a few lathes and 3-axis machining centres, that is where the similarities to other businesses end. Sheeram always had a vision of becoming a leading supplier to the aerospace industry in India and thanks to OPEN MIND Technologies, the company is compressing a typical 10-year journey to becoming a key aerospace supplier into just three to four years.
Sheeram has three generations of expertise in managing successful businesses and this experience identified that large-sized aerospace component manufacturing is not widely available in India. This is because the sector involves a very high capital outlay, a gestation period of 3 to 5 years before reaping returns, a very real challenge of suitable manpower availability, skillset and quality management system implementation. Furthermore, there is a significant cost associated with the production of large-sized components. With a clear vision of entering this niche area of critical aerospace component machining, the management team invested in proven large bed 5-axis machining centres from its inception. The first machine installed was KX-200 from the French machine tool manufacturer Huron.
As the management was previously associated with the manufacturing of large-sized multi-axes machines and was aware of the capability of hyperMILL along with the proven case studies, they chose hyperMILL as the CAM platform suitable for their requirements.
Making Way for hyperMILL
In 2020, the company received Request For Quote (RFQs) from two government departments for critical impeller and first-time developed Tera Hz frequency Antenna reflector panels. Shreeram immediately approached OPEN MIND and released the PO for hyperMILL in October 2020.
With 5-axis machines, a seat of hyperMILL and a demonstrable example of its ability to machine impellers, Sheeram then targeted ISO: 9001 and AS9100 D certifications as well as supply chain certification with the key primes. With the foundation blocks in place, the company started to receive an increasing number of RFQs.
The tender process for the operation of critical structural aluminium 6061-T651 parts continued for 8 months with numerous machining and inspection trials undertaken. With a 6µm root mean square over the 850 by 850mm parabolic surface area on one side and the other side having a 91% material removal with multiple pockets with wall thicknesses of 2mm – the machining was significant with the 150kg billet being machined to just 10.5kg. Add stress relief into the equation, and it was little wonder that Sheeram was the only Indian manufacturer that technically qualified for this extremely complex job. Since winning the ongoing order in 2022, Sheeram has machined more than 66 of these high-value complex space antenna reflector panels.
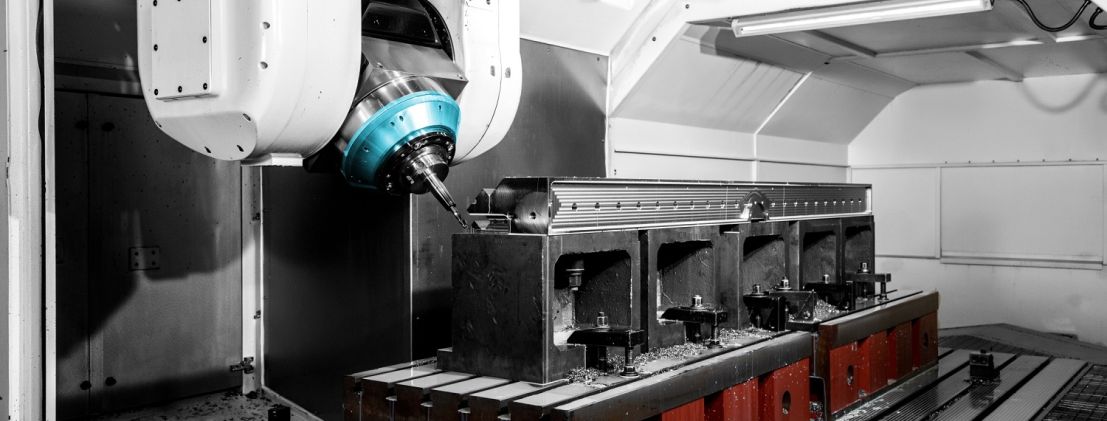
hyperMILL MAXX Machining
Whilst hyperMILL has simplified the programming process, the company’s continuous quest for innovation has also seen it apply hyperMILL MAXX Machining to the pocket roughing cycles of the panels. The result has been a further 30% reduction in machining times from 40 to 30 hours. To potentially reduce the overall machining time even further, Sheeram has been successfully trialling barrel tools on the panels. As the pioneer in developing the barrel tool CAM strategy and also being instrumental in working with cutting tool manufacturers to develop the tools in the first instance, OPEN MIND has all the 5-axis strategies to help Sheeram yield even greater results with these tools.
Alluding to this, Mr Sandeep Satani, Chairman and Managing Director of Shreeram Aerospace & Defence LLP says: “These complex parts have a total production time of 80 hours each. Forty hours are spent machining with the remaining 50% of the time spent on set-ups, as the parts continually have to undergo stress relieving at every stage. Since machining the first 66 parts, we have now machined an additional 18 parts with barrel tools – this has reduced our finish machining times from 8 hours to 4.”
Instigating the adoption of barrel tools for this project was a cooperation between Sheeram, OPEN MIND and high precision tool manufacturer EMUGE-FRANKEN Group. As Mr Sandeep Satani adds: “hyperMILL MAXX Machining is reducing our roughing time by 30% with trochoidal HPC milling strategies. Now, the barrel tools are yielding an additional 50% saving on finishing. With the increased stepover which can be realized with the barrel cutter and the finishing strategies, we are witnessing significantly improved surface finishes. Our surface finishes have improved from 0.8µRa to 0.4µRa and this is on pocket walls that in many instances are only 2mm thick.”
Obtaining precision levels of just 6 microns
With 2mm thick walls on the pockets of the Tera Hz frequency Antenna reflector panels, minimum depths of cut had to be taken to reduce vibration. However, the increased step-down with the barrel tools has enabled Sheeram to enhance the surface finishes with minimum vibration. Alluding to this challenge, Mr Sandeep Satani continues: “During the tender process, there were two other companies in the running to win the order for the reflector panels. The complexity of the parts meant that two of our rivals could only achieve a precision level of 95 and 70 microns respectively – this was outside the parameters of the project. When machining trial parts as part of the tender process, we achieved precision levels of 9 microns against tender requirement of 12 microns. We were the only company in the tender process that could successfully machine the parts. Subsequently, we have enhanced our machining processes to yield a consistent precision level of just 10 microns. Now, with the support of OPEN MIND on our machining strategies and EMUGE-FRANKEN on the cutting tools, we are obtaining precision levels of just 6 microns.”
When Sheeram initially acquired a seat of hyperMILL, the company was in the fortunate position of having a vastly experienced hyperMILL programmer to train and develop other members of staff whilst also programming some of the most challenging components the industry could imagine. This has created a culture where internal staff have now become well versed in the intricacies of programming difficult parts despite having limited experience – a factor that demonstrates the ease of use of hyperMILL.
Critical components
Some of the critical components the company has manufactured include a Haynes 188 Cobalt indigenisation project that constitutes an 800mm diameter formed ring with a 3mm wall thickness and a 3-start Inconel inducer blade with various wall thicknesses for aerospace engines. Other challenging projects include a carbon composite aircraft wing assembly fixture, Inconel turbine discs and UAV development engine parts from aluminium alloy 7075 that require two parts with up to 90% mating surface contact. Shreeram has proven case studies for the supply of nearly all types of aerospace tooling that includes large-sized fabricated assembly tools. The company has now delivered over 300 projects to Tier 1 and OEM aerospace manufacturers. With companies like Boeing, Airbus, Lockheed Martin and many others implementing strategies to create a manufacturing base in the region for both production and the support of MRO programmes, Sheeram is in pole position to work with these globally renowned brands.
Concluding upon the future opportunities for Sheeram and its partnership with OPEN MIND, Mr Sandeep Satani says: “India has just landed its Chandrayaan-3 Lander (rocket) on the moon and we are becoming a world leader with our space programme. In addition, Indian airline IndiGo & Air India recently placed the world’s largest aircraft order for 1000 aircrafts. Both the space programme and the heavy investment in the aerospace industry will need local manufacturing support and an MRO supply chain. With a niche for machining critical precision parts up to 3.5m, Sheeram is in a great position to support this growth. Furthermore, our partnership with OPEN MIND is enabling us to compress our lead times to increase our throughput to deliver an exceptional level of service to the industry as it evolves.”