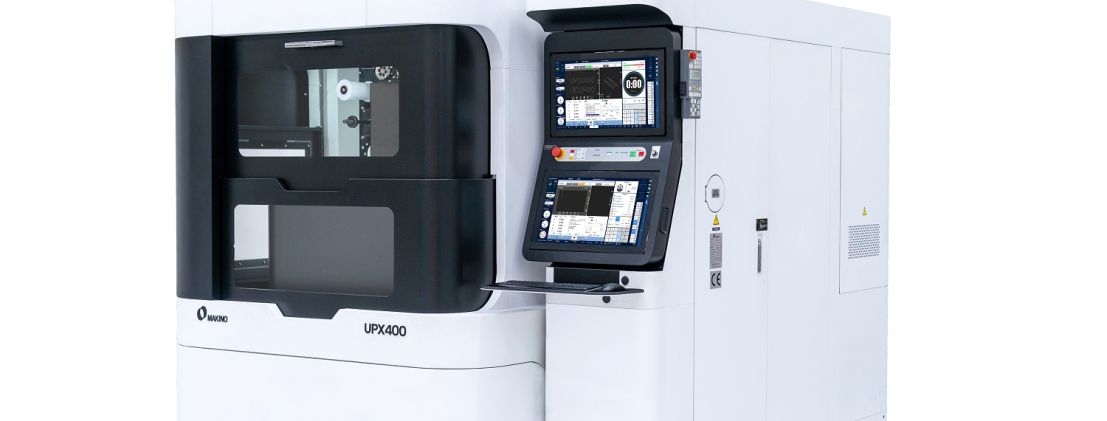
New Makino UPX400 Wire EDM Improves Surface Finishing for NEV Components
The demanding machining requirements for new energy vehicles (NEVs), e.g. even smoother surfaces of battery components, more uniform housings and less noisy NEV gears, have presented the high-end wire EDM market with new challenges. What’s more, these stricter requirements come when the shortage of skilled machinists is badly affecting the industry. To answer these challenges, Makino launched the UPX400 wire EDM machine.
The solution to the demands of machining NEV components is an even smoother surface finish. Besides, the evidence points to the service life of dies and moulds being up 500% longer through better finishing. Die & mould makers have traditionally relied on hand-finishing jobs to achieve the required level of surface smoothness. But the shortage of skilled machinists means they are looking for an alternative. Makino has listened to these needs and developed the UPX400 to improve surface finishes, reduce polishing time and prepare the metal for coating. This stable, ultra-high-precision machine is designed not only to satisfy tougher machining demands, particularly in the NEV market, but is also engineered to support automated jobs.
What’s new? Key features
The machine’s gate-type design divides the axes between the table and the head, which enables deformation and accuracies to be controlled with even greater precision. For example, cutting a steel component with five passes can achieve a roundness of 0.67 micron and a surface roughness (Ra) of 330 nm.
The new table has been designed from scratch and is insulated to reduce the time required for full voltage to be reached. This significantly reduces cycle times while improving the surface finish. The new design enables surface roughness to be reduced by almost 50% with the same number of cuts as on other WEDM machines.
The new EW200B power unit reduces the amount of hand polishing needed after machining. The new generator generates shorter and faster pulses on the wire and a better-controlled, faster-discharged spark. As a result, Rz roughness is about 40% lower than on comparable machines.
In response to the shortage of skilled labour, Makino’s R&D specialists were determined to develop a machine that is easy to operate and can be maintained in the same way as Makino’s U3 or U6 machines. U series users will be immediately familiar with the UPX400 or UPX600 thanks to the same upper and lower independent pumps, the same Hyperdrive Extreme system for simplified usage and maintenance of the machine, and the same Hyper I control unit to facilitate operability.
Although the UPX499 is a water-based WEDM machine, it can easily compete on the very demanding oil-based market and achieve similar or even better rough-ness levels in just half the time.