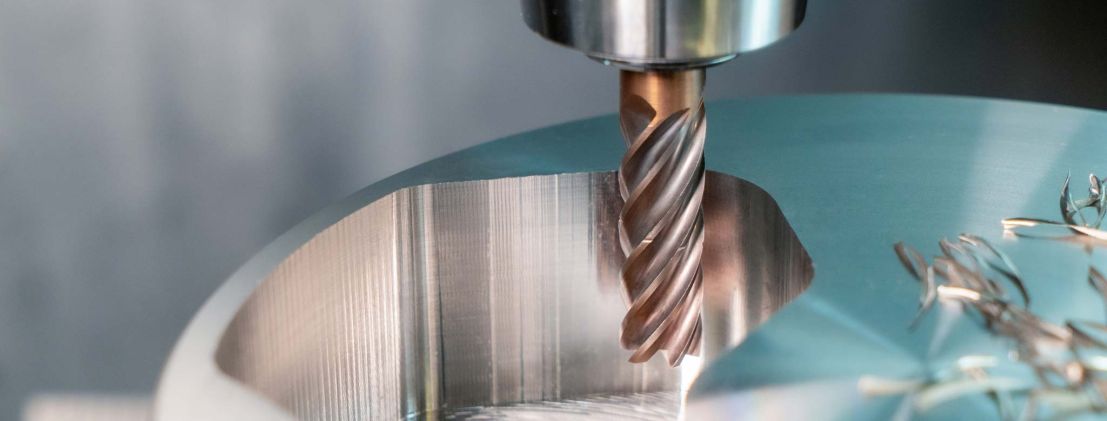
Mapal clearly divides four focus sectors at AMB
On a 390 square metre stand Mapal's trade fair presentation is clearly divided into the four focus sectors of automotive, aerospace, die and mould making and fluid power technology. Siegfried Wendel, Chief Sales Officer, comments on the AMB presentation: "We have used the last two years very intensively and strategically realigned ourselves. We have formed a team for our defined focus industries and brought the product portfolio to market maturity. We will present the results of the new market strategy in full for the first time at the AMB.”
“Our customers' future investment plans will certainly also focus on the concept of sustainability. We are taking action in many areas to make machining processes more sustainable. The technology of minimum quantity lubrication plays just as important a role as the hydraulic expansion technology. Replaceable head solutions or the streamlining of tool circulation through intelligent and reliable tool management solutions bring further advantages in terms of sustainability. We look forward to discussing this topic in detail at the trade fair."
New cutting materials for reaming and fine boring
Mapal presents the two new cutting materials HP016 and HP018. They are specially designed for the particular requirements of reaming and fine boring high-alloy and stainless steel as well as cast steel and hardened steel. The HP016 cutting material is suitable for all machining operations with a slightly interrupted cut, while the HP018 cutting material is used for continuous cutting conditions. Both are based on a silicon-doped PVD coating on two different carbide grades with low cobalt content, which stands for extreme wear resistance and high dimensional accuracy.
The new cutting materials will be used for the market launch in the reamers of the MN series, among others. These tools stand for the highest accuracy, can also be optimally used for hard reaming and reaming stainless steel thanks to the new cutting materials. They function according to the “Mapal principle” - with one indexable insert and guide pads arranged around the circumference, which are made of carbide, cermet or PCD depending on the application.
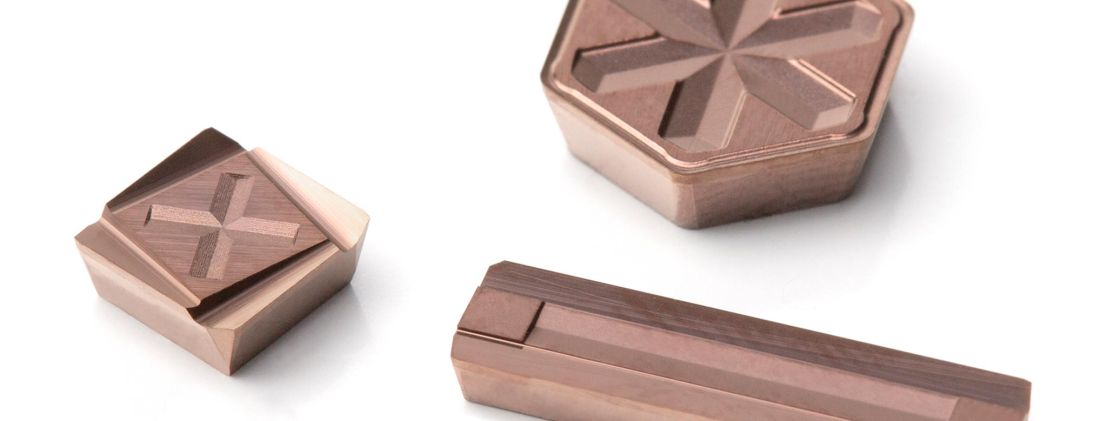
E-Mobility: Basic, Performance and Expert Solutions
Tool solutions for e-mobility are of particular importance in the automotive sector. For demanding components that will be produced in high quantities, Mapal presents different machining levels: Basic, Performance and Expert. The new classification describes the different machining solutions depending on the quality requirements, number of units and investment. The Performance Line is aimed at series production and focuses on machining with special tools. It is mainly used when new components are to be produced efficiently and economically on existing systems.
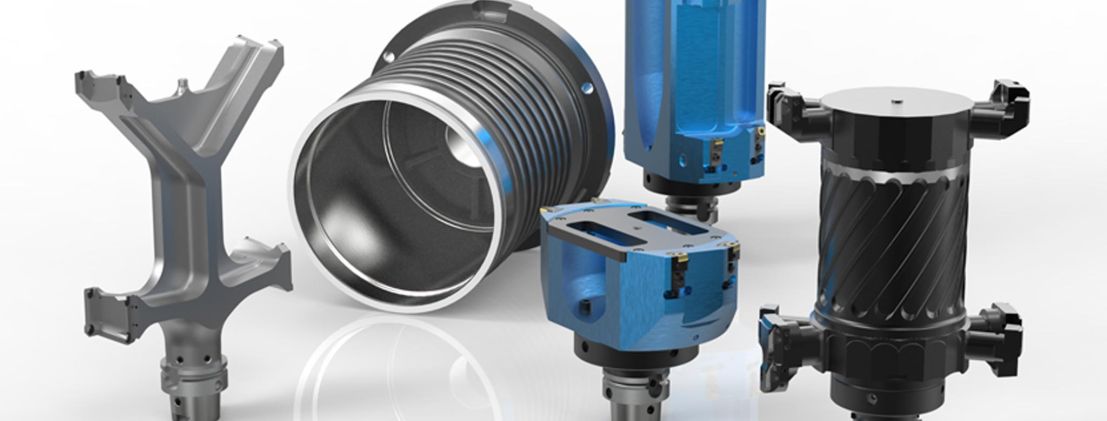
Increase economic efficiency in aluminium milling
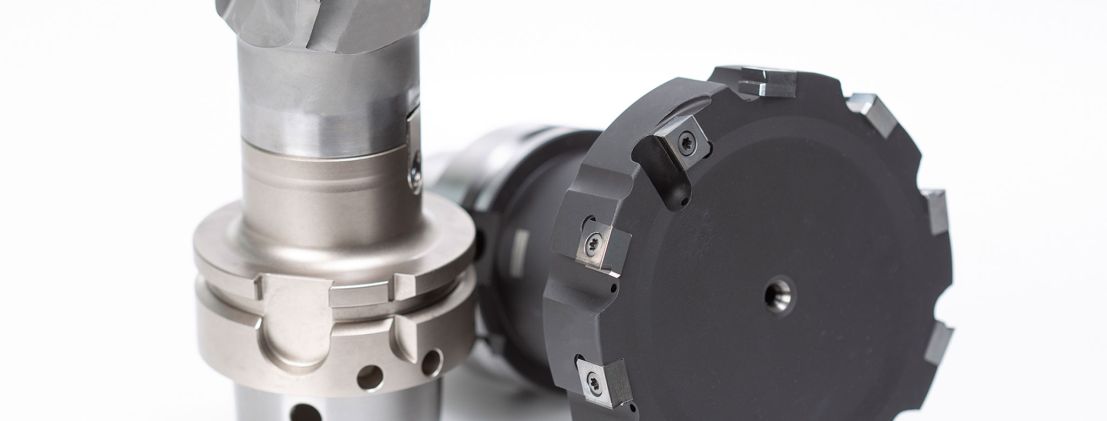
Mapal is expanding its aluminium milling program with two new products. The FaceMill-Diamond-ES is a versatile all-rounder that ensures high economic efficiency and sustainable process reliability in demanding production conditions with smaller quantities and changing component types. The indexable insert milling cutters of the new NeoMill-T-Finish series significantly increase the economy and efficiency of finish machining in series production. The finish milling cutter with exchangeable inserts functions according to the plug & play principle: customers change the inserts directly on site without adjusting them afterwards. In addition, this also means that fewer tool bodies have to be kept in stock. What makes the new milling cutter unique is a patent-pending system of insert arrangement, which results in a homogeneous wear pattern of the cutting edges, longer tool life and thus a low cost per part.
Titanium trochoidal milling
The tool program for titanium machining is expanded by two efficient milling tools. The five-edged trochoidal milling cutter OptiMill-Tro-Titan is characterised by maximum metal removal rate and shines with excellent surfaces due to unequal spacing and unequal pitch of the cutting edges. It is designed for trochoidal milling in partial cutting, trimming and for cutting depths up to 3xD. The new radial insert milling cutter NeoMill-4-HiFeed90 will be available as an end mill, screw-in milling cutter and milling cutter head from January 2023. The universally applicable high feed milling cutter stands for high productivity and is characterised by the highest stock removal rates, very high feed rates and large chip depths.