Last week, DMG Mori hosted an Open House event in Bielefeld, Germany, dedicated to showcasing the latest technologies driving future-oriented production. Among the event's highlights were 20 high-tech machines, including two world premieres: the CTX 750|2000 and the LASERTEC 30 SLM 3rd Generation, as well as the innovative CELOS X Factory. Attendees had the opportunity to explore these state-of-the-art solutions, designed to enhance efficiency, precision, and productivity in manufacturing processes.
One of the two world premieres during the Open House was the new CTX 750|2000 universal lathe. Thanks to the left and optional right spindle, the CTX 750|2000 enables 6-sided complete machining of workpieces up to 2,040 mm in length. With its large working area, the world premiere is designed in particular for the production of large components and long shafts. Thanks to left and right spindles and a 170 mm Y-axis for off-center milling with driven tools, 6-sided complete machining of demanding workpieces is possible. Like its smaller sister machines, the CTX 750|2000 therefore stands for maximum flexibility in an attractive price segment. The new size in the CTX series also serves the four pillars of Machining Transformation (MX), with which DMG MORI is shaping the future of manufacturing: Process Integration, Automation, Digital Transformation (DX) and Green Transformation (GX).
"In the premium segment of universal turning, we see the CTX 750|2000 as the perfect companion for the complete machining of long workpieces," says Dr. Claudio Merlo, Managing Director of DMG MORI Tortona, positioning the new development. The work area is dimensioned for workpieces with a diameter of 700 mm and a length of 2,040 mm. It is also easy to automate, for example with the Robo2Go Max. The app-based CELOS X control system with 24" multi-touch display enables simple integration into company networks and drives digitization forward - naturally with the highest safety standards. Modern drives such as the synchronous spindle motors and GREENMODE ensure energy-efficient operation. This reduces energy consumption by up to 10%.
Stability and extensive cooling measures
The CTX 750|2000 has a left-hand spindle with a speed of up to 3,250 rpm and a maximum torque of 1,975 Nm. The right-hand spindle reaches 4,000 rpm and 770 Nm. The turnMASTER spindle concept with four bearings ensures maximum stability and precision, as well as offering a large bar capacity of up to ø 127 mm. The positioning accuracy in the C-axis is 0.001°, while the X- and Y-axes are equipped with a direct measuring system from MAGNESCALE as standard. The air/oil cooling for the turret gears ensures optimum temperature control. In the top performance option, a VDI 50 turret with direct drive enables high-speed milling of demanding applications. The driven tools achieve speeds of up to 6,000 rpm and a torque of 85 Nm. The Y-axis can be moved by +/- 85 mm so that workpieces can be machined off-center.
Automation solutions from a single source
Automated production solutions are an essential way for DMG MORI to maintain competitive production in the long term. With the CTX 750|2000, autonomous operation can be realized in unmanned night and weekend shifts. The Robo2Go Max is suitable for loading and unloading chuck parts or shafts in medium batch sizes. The robot with a payload capacity of 210 kg is designed for shaft parts weighing up to 115 kg with a maximum length of 1,200 mm and a diameter of 200 mm. Such a solution brings additional flexibility to production automation.
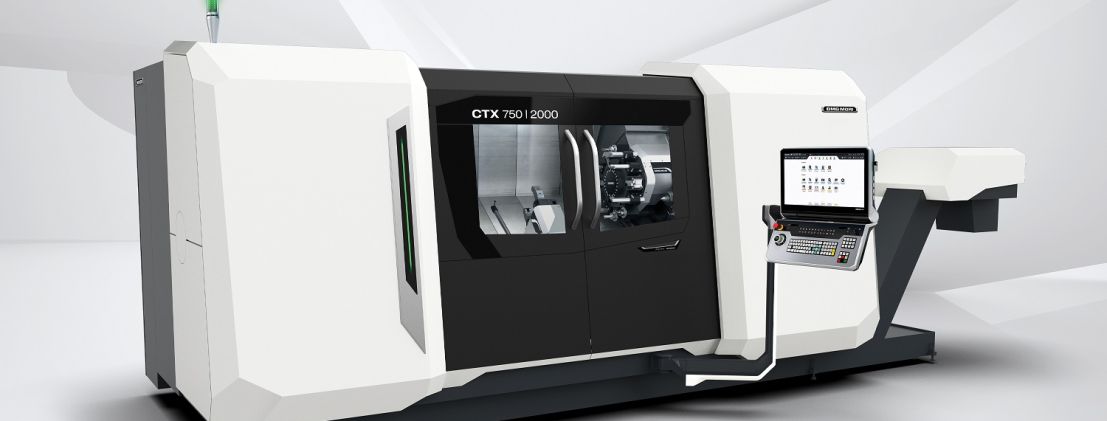
Additive Manufacturing with the new LASERTEC 30 SLM 3rd Gen
DMG MORI lays a fresh foundation for Additive Manufacturing with the introduction of the LASERTEC 30 SLM 3rd Gen at their Open House in Bielefeld. This new platform for additive manufacturing has been designed from the ground up using all the additive and machine tool design know-how within DMG MORI. With its new quad laser full overlap working area, and a build volume of 325 x 325 x 400 mm, the center of market demand is targeted. The LASERTEC 30 SLM 3rd Gen is the new benchmark for robustness and repeatability.
The LASERTEC 30 SLM 3rd Gen builds on strengths from previous versions and accommodates customer requirements in an ever-changing market for additive manufacturing. The most obvious feature when looking under the covers is that the LASERTEC 30 SLM 3rd Gen basic structure uses castings. The same material and design principles are used on the majority of DMG MORI milling and turning machines. Using a casting is standard practice for DMG MORI, but is new to additive manufacturing. It is a material that guarantees the best rigidity and predictability for manufacturing.
Thermally stable
Unlike machine tools, there are no dynamic forces from the movement of the axes on a LASERTEC 30 SLM 3rd Gen. However, temperature changes that cause thermal expansion within the machine are inevitable. DMG MORI has years of experience in minimizing the effect of and compensating for temperature changes within its products. Great care has been taken to ensure that the process chamber is an isolated unit within the machine. Therefore, the Floating Process Chamber is free to expand in all directions during temperature variations. In contrast, the optics are mounted on the rigid casting Gantry Frame. The distance in Z between the optics and powder bed is kept constant by calibrating the recoater to a reference surface. In addition, the Z-axis is actively compensated for any displacement. Therefore, problems related to the distance between the optics, the top surface of the powder bed and associated problems with the recoating layer can be eliminated.
Reduce time with an automated powder material processing unit
To reduce time between build jobs and to increase flexibility, the DMG MORI rePLUG units have been an important competitive advantage on previous SLM products. The rePLUG is a self-contained automated powder material processing unit that can be exchanged with other rePLUG units. Existing customers with qualified processes, which are often found in the aerospace and medical industries, appreciate and rely on the rePLUG system to ensure top-quality powder is continually in use. The excess powder from the working area is sieved, stored and prepared for re-use, all under an inert gas atmosphere within a closed loop. This not only minimizes oxidization or any moisture build-up but also reduces potential operator exposure to the powder. An important safety consideration. For other customers, the rePLUG makes changing between different materials much easier. Other related components inside the machine itself can be as easily cleaned, making the LASERTEC 30 SLM 3rd Gen the quickest machine to change between materials on the market. This greatly widens the range of applications that a single machine can be used for.
For the first time on a DMG MORI LASERTEC SLM, it is possible to exchange the build container quickly. This further increases machine efficiency since it is no longer necessary to wait for the build job to cool down. Covers for the build container and the working area are stored inside the working area during operation. These are used to close off the build container upon removal and to ensure that the inert gas atmosphere inside the machine is preserved. The next build job can be quickly started without a renewed inert gas flooding.
Disruption during manufacturing is further minimized by camera monitoring of the surface of the powder bed. After each layer, the surface is scanned for anomalies before the re-coater moves. If there is a protrusion that is not detected in time, then the bi-directional re-coater is equipped with a collision protection mechanism to shorten any subsequent downtime. Upon making contact with a protrusion sticking up from the bed, the re-coater immediately detaches from the drive system, thus avoiding further damage.
The newly designed inert gas flow over the powder bed ensures a consistent laminar flow during operation. The secondary gas flow below the protective glass aims to avoid any residue build-up on the protective glass. The wind tunnel-like design ensures unprecedented gas flow performance. The protection glass itself is under constant observation by a secondary camera system that gives a warning if there is a problem. Additional lighting is provided in the area of the protective glass to support the operator when checking and cleaning the protective glass between build jobs.
Good ergonomics
DMG MORI places a lot of emphasis on the usability and ergonomics of the machine. Reducing the operator contact with the powder is a primary consideration. Another key area where the LASERTEC 30 SLM 3rd Gen excels is with the CELOS X operating environment. CELOS X guides the operator through all the steps required to get a job running. For example, it prompts the operator to clean the safety glass and shows how it is done. It also walks the operator through the powder refilling process or how daily checks and maintenance are to be performed. CELOS X guidance is important for the adoption of safe and efficient operating procedures on the shopfloor.
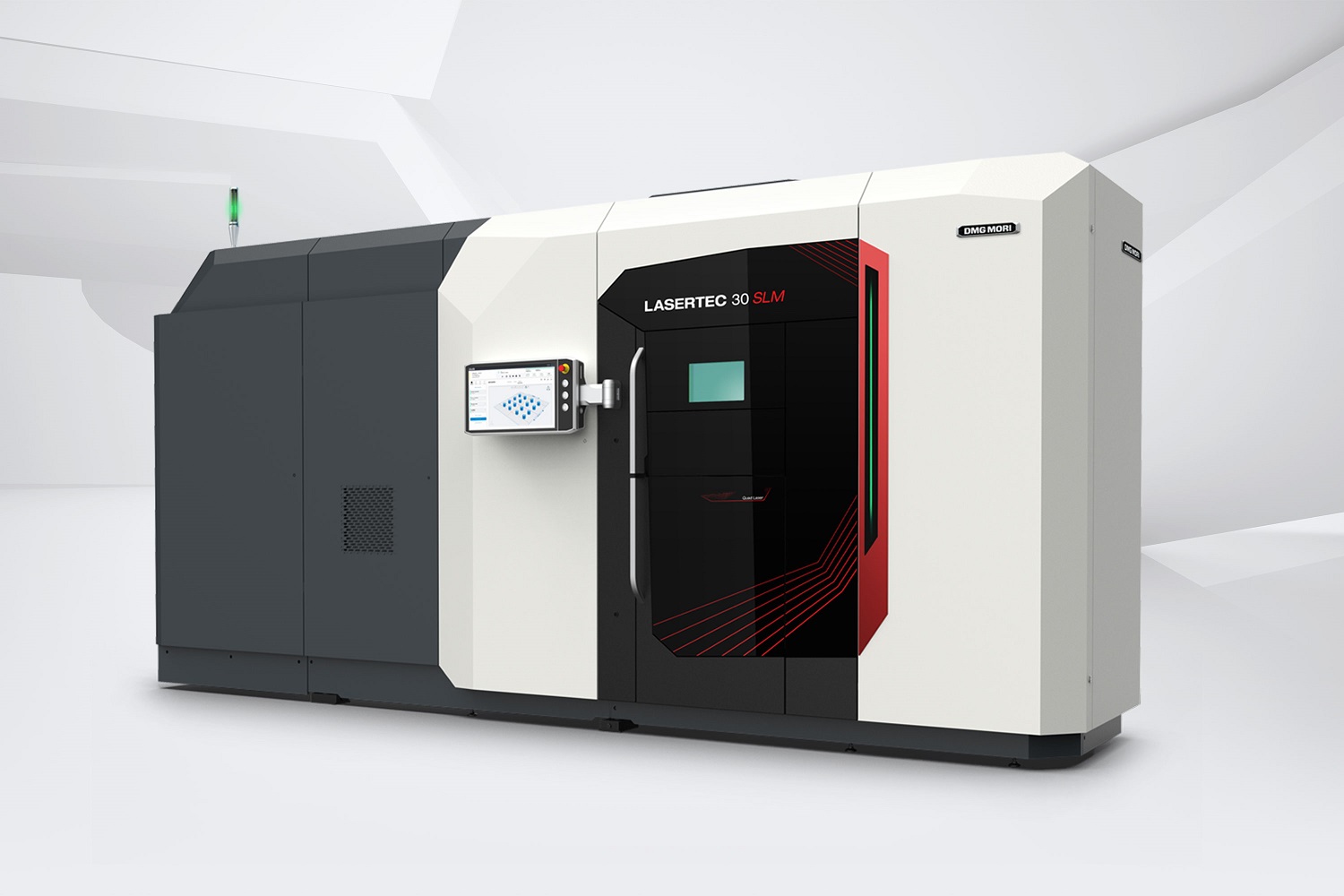
Combating the skills shortage with efficiency and sustainability
With the CELOS X Factory in Bielefeld, DMG MORI demonstrated the full potential of Machining Transformation (MX) under real production conditions and supported its customers in implementing the concept.
The constantly growing variety of products, increasing quality pressure, resource scarcity and shortage of skilled workers pose major challenges for manufacturing companies. Against this backdrop, efficient and sustainable manufacturing solutions are more in demand than ever. With Machining Transformation (MX), DMG MORI is paving a future-proof path to a competitive future. Based on the pillars of Process Integration, Automation, Digital Transformation (DX) and Green Transformation (GX), the machine tool manufacturer realizes holistic manufacturing concepts from design to quality control. The CELOS X Factory in Bielefeld embodies this philosophy with additive and subtractive technologies, automation solutions and digitization products.
As a separate production area in Bielefeld, the CELOS X Factory is more than just an experience center or a demo factory. "We produce series components for use in DMG MORI machines, from simple turned and milled parts to highly complex components in metallic 3D printing," explains Dr. Rinje Brandis, Head of CELOS X Factory. The DMG MORI machine tools and automation solutions are the heart of the CELOS X Factory. They are supplemented by machines from partner companies. This allows a wide variety of production processes to be mapped. Dr. Rinje Brandis adds: "In addition to machine technology, the CELOS X Factory also focuses on people. With tailor-made digitization solutions, we impressively demonstrate how assistance systems, no-code programming and artificial intelligence can be used to counteract the shortage of skilled workers."
Fully digitized smart factory
What sets the CELOS X Factory apart from a pure demo factory is the end-to-end digitization of real production. With a view to the requirements of the future, this digital process world goes far beyond the current status quo. Dr. Rinje Brandis gives examples: "Orders can be tracked at individual part level, the CAD/CAM process chain extends into quality management thanks to PMI models and energy monitoring looks at individual process steps." The digital transformation is therefore making a significant contribution to the green transformation. "Increased productivity, reduced energy consumption and careful use of resources make it easier to meet sustainability targets."
Manufacturing solutions for integrated processes
The extensive features of the CELOS X Factory are already evident in the engineering. SIEMENS NX acts as a hybrid CAD/CAM system for product development, design and production. The CELOS X Factory machine park includes a CTX beta 1250 TC for 6-sided turn-mill complete machining as well as a DMU 40 and DMU 50 for 5-axis simultaneous milling. A Robo2Go Milling enables automated handling on the DMU 40. In additive manufacturing, the CELOS X Factory team uses several LASERTEC SLM machines, including a LASERTEC 30 SLM 3rd Generation, which will celebrate its world premiere at Open House 2024 in Bielefeld.
Leading companies as partners of the CELOS X Factory
In post-processing, depowdering systems such as the SFM-AT350 from Solukon clean the additively manufactured components. A FOBA M2000 laser marking device marks the components for clear identification and a FANUC ROBOCUT α-C600iC wire EDM machine enables precise cuts. A CREAFORM HandySCAN 3D Black Elite is used for three-dimensional scanning of free-form surfaces and complex geometries in quality control. A Mitutoyo CRYSTA is used as a coordinate measuring machine. "These partners are among the leading companies in their respective sectors. This enables us to use a future-oriented production environment with innovative solutions and provide this for our customers' applications," says Dr. Rinje Brandis, assessing the selection of partners in the CELOS X Factory.
Focus on people - reducing complexity with digitization
The CELOS X Factory represents a real production environment with a variety of different machine technologies and operating concepts. In times of an ongoing shortage of skilled workers, digital solutions such as CELOS X and the no-code platform TULIP are more important than ever for creating customized apps to digitize work processes. All machines in the CELOS X Factory are connected to the TULIP-based MES system. This is supplemented by assistance applications that provide people with targeted support and thus significantly reduce the complexity of modern production systems. The experience gained from the CELOS X Factory forms the basis for customer projects for digital transformation.
Processing individual customer projects
Customers also benefit from the CELOS X Factory. Under the motto "Bring your own idea", they can bring their own tasks from their day-to-day production into this modern environment. In individual workshops, the DMG MORI Academy supports these customers in the development of initial solution concepts, which are tested in practice in the CELOS X Factory. This is precisely where Dr. Rinje Brandis sees the added value for customers: "On the one hand, the end-to-end digitized and automated process chain shows companies how sophisticated components can be manufactured more efficiently and sustainably. On the other hand, such manufacturing concepts reduce the demands on personnel, which also counteracts the shortage of skilled workers."
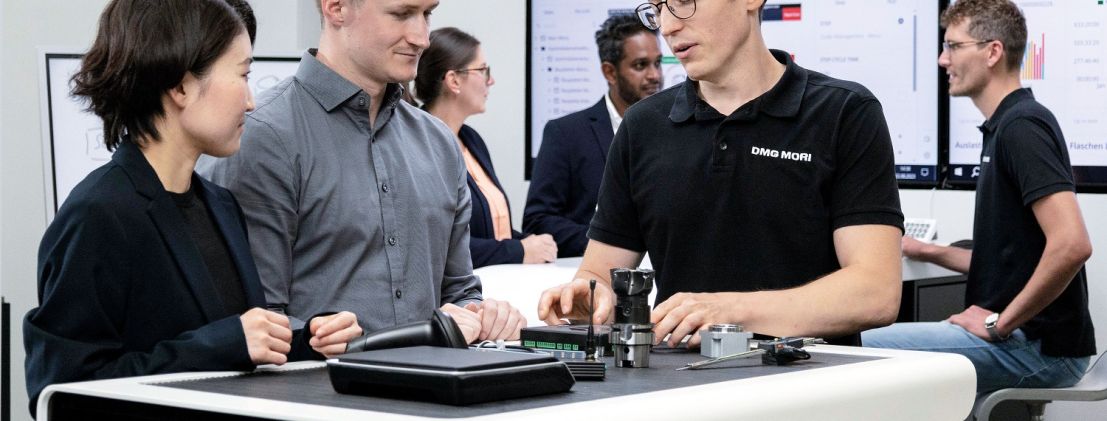