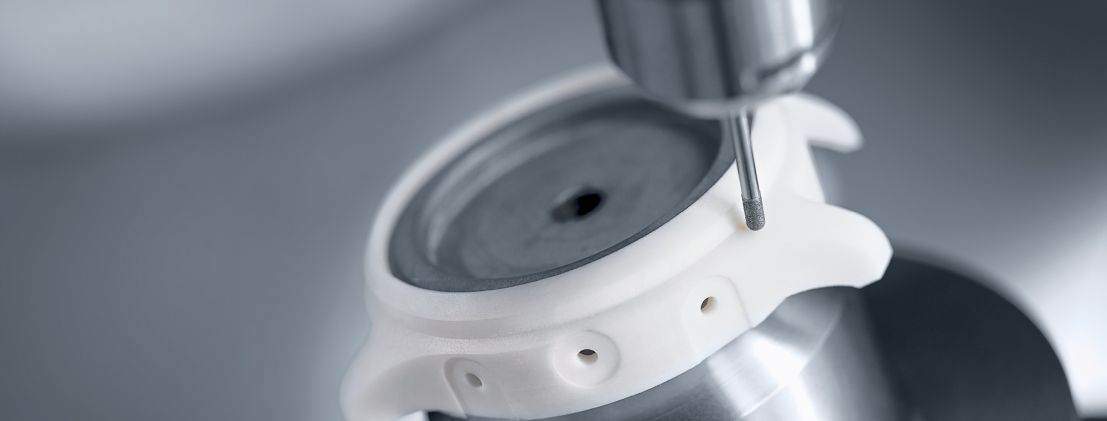
DMG MORI Redefines Precision With the 3rd Generation ULTRASONIC 20 linear
At the DMG MORI Open House in Pfronten, the newly unveiled ULTRASONIC 20 linear 3rd Generation demonstrated significant advancements in precision machining. Building on the successes of 600 predecessor models, this machine represents a breakthrough in 5-axis simultaneous machining technology. Achieving positioning accuracies of 3 µm in the linear axes and 3" in the rotary swivel axis, the machine exceeds even µPrecision standards. Designed for ultrasonic-assisted milling and optional grinding, it addresses the complex demands of advanced materials, such as ceramics and composites used in critical industries like semiconductors. The technology delivers reduced process forces, enhanced feed rates, better surface finishes, and extended tool life—all underscored by DMG MORI's ongoing pursuit of innovation.
The basis for the high precision of the DMU 20 linear 3. Generation and ULTRASONIC 20 linear 3. Generation is the new FEM-optimized machine bed made of EN-GJS 600 cast iron. It ensures 15% greater rigidity compared to the previous generation and is constructed like a measuring machine in a gantry design. This ensures enormous long-term stability, so that the machines achieve absolutely reproducible machining results over the long term - a decisive factor for quality assurance with strict production standards. The thermo-symmetrical design enables optimum regulation of temperature-related fluctuations. Cooling of the bed and the linear drives as well as direct position measuring systems from magneSCALE in all axes also contribute to the high accuracy.
100% linear technology for maximum accuracy and dynamics
Torque motors in the NC swivel rotary table and linear drives from Siemens in the X, Y and Z axes - their guides are 30 mm wide - make the DMU 20 linear 3rd generation a fully linear machine. The wear-free direct drives guarantee the best possible positioning and repeat accuracy and work without backlash. As a result, the DMU 20 linear already achieves first-class surface qualities. The ULTRASONIC model also guarantees these qualities in hard, brittle advanced materials. In addition, direct drives give the machining process maximum dynamics and accelerations of over 2 g. The machine achieves feed speeds of up to 60 m/min.
Wide range of spindles for every application
The wheel magazine of the DMU 20 linear 3rd generation offers space for 26 tools for a high level of machining versatility, while an optional chain magazine has 60 tool slots - regardless of the HSK interface. The maximum tool size is ø 70 mm x 200 mm in length and the weight is 1 kg. An optimized tool flap with chip flushing minimizes the risk of contamination in the changer. To be able to use even small tools at optimum cutting speeds, the DMU 20 linear 3rd generation has a spindle with 42,000 rpm with HSK-32 or HSK-40 interface as standard. An HSK-32 spindle with 60,000 rpm is available as an option. In the case of the ULTRASONIC 20 linear 3. Generation, the spindle has an ULTRASONIC actuator, which enables ultrasonic-supported grinding. The spindles have oil-air lubrication. For demanding workpieces with longer machining times, we recommend using the HSK40 CSC spindle with shaft cooling. A permanently grease-lubricated spindle is available for machining sensitive components (e.g. in medical technology) that must not be contaminated with oil or emulsion.
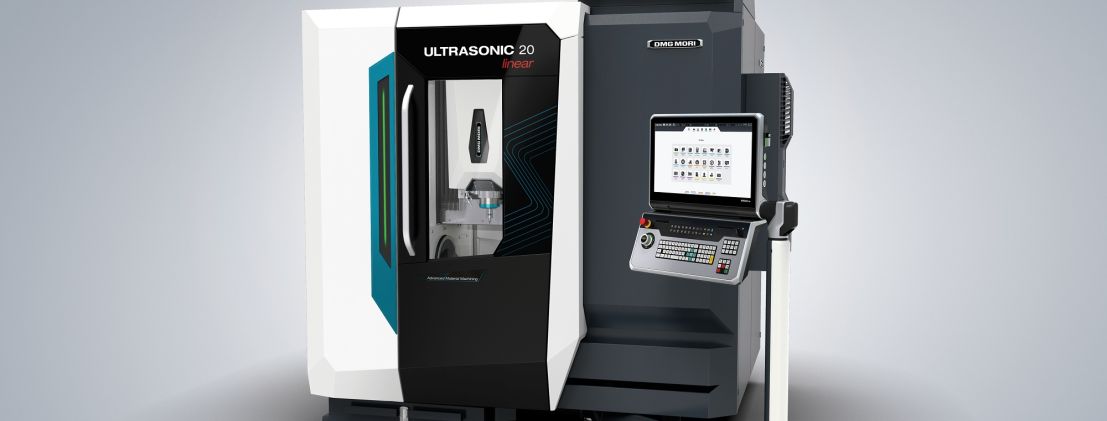
Wide range of spindles for every application
The wheel magazine of the DMU 20 linear 3rd generation offers space for 26 tools for a high level of machining versatility, while an optional chain magazine has 60 tool slots - regardless of the HSK interface. The maximum tool size is ø 70 mm x 200 mm in length and the weight is 1 kg. An optimized tool flap with chip flushing minimizes the risk of contamination in the changer. In order to be able to use even small tools at optimum cutting speeds, the DMU 20 linear 3rd generation has a spindle with 42,000 rpm with HSK-32 or HSK-40 interface as standard. An HSK-32 spindle with 60,000 rpm is available as an option. In the case of the ULTRASONIC 20 linear 3. Generation, the spindle has an ULTRASONIC actuator, which enables ultrasonic-supported grinding. The spindles have oil-air lubrication. For demanding workpieces with longer machining times, we recommend using the HSK40 CSC spindle with shaft cooling. A permanently grease-lubricated spindle is available for machining sensitive components (e.g. in medical technology) that must not be contaminated with oil or emulsion.
Large and clearly laid out workspace
The increased travel of the compact DMU 20 linear - it only requires a footprint of 3.8 m² - is 220 x 370 x 290 mm, which means that the Y-axis has increased by 80% compared to the previous model. This is mainly due to the larger swivel range of +130° to -93°. The axis can be swiveled in the direction of the operator, which offers a better view of the table and more flexibility. Components with a diameter of ø 220 mm and a height of 283 mm (with Erowa ITS clamping system) can be machined.
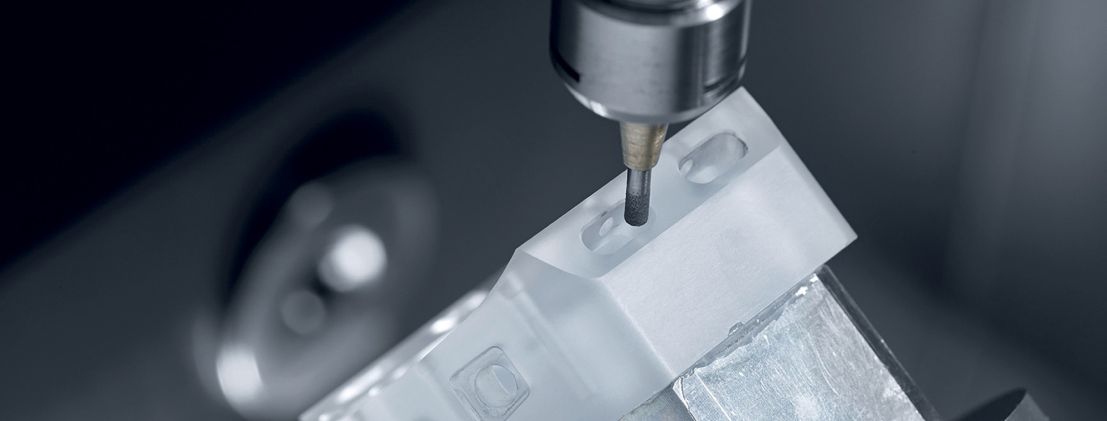
Process integration and automation solutions
Process integration and automated production are key pillars of the Machining Transformation (MX) practiced by DMG MORI. The machine tool manufacturer has also taken this into account in the case of the ULTRASONIC 20 linear 3rd generation - with ULTRASONIC grinding. The C-axis is optionally available with 1,500 rpm, so that the machine can also perform cylindrical grinding operations. The Schunk NSA 120 clamping system is offered exclusively with this option, as it fulfills maximum safety guidelines. With the ULTRASONIC AxialGrinding technology cycle, any 3D geometries based on rotationally symmetrical blanks can be conveniently programmed. The process integration is supplemented by in-process measurement and laser tool measurement. Automation solutions such as the PH 10 and PH 50 pallet handling systems or robot-assisted systems such as the MATRIS light ensure additional productivity even in unmanned shifts.
DMG MORI increases process reliability in automated production with reliable coolant and chip management. The optional 200-liter zeroSludge coolant tank, together with the box filter chip conveyor, ensures consistent disposal of fine chips and sludge. The internal protection is reinforced with stainless steel and ceramic-coated internal covers to prevent chip accumulation. The zeroFOG oil mist separation system, which is also available, keeps the working environment clean and is easy to maintain.
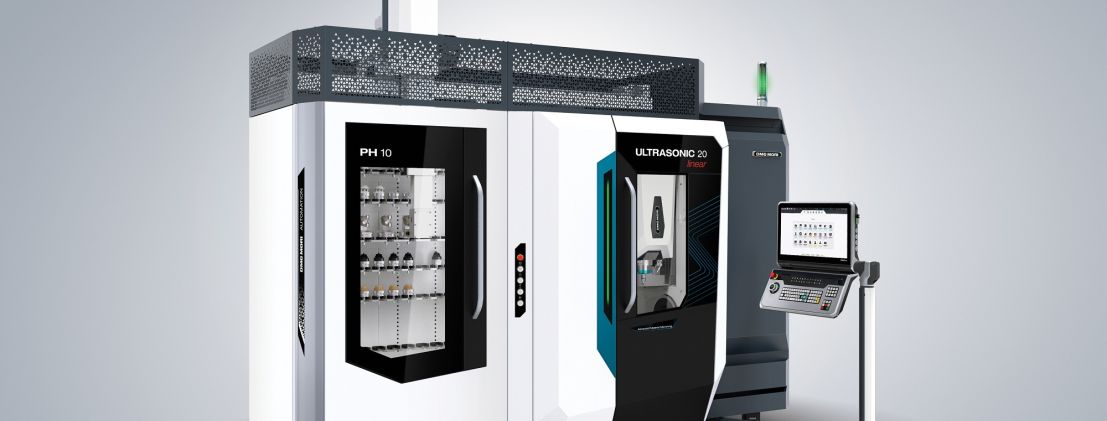
Technology cycles for digital transformation (DX)
With CELOS X on a SINUMERIK One from SIEMENS and a 24" ERGOline IV control panel with touchscreen, DMG MORI is opening up a user-friendly path to Digital Transformation (DX), another pillar of Machining Transformation (MX). While CELOS as an app-based control system offers maximum operating convenience, the SINUMERIK One is the step towards future-proof high-speed machining with a dialog-based ShopMill user interface. DMG MORI technology cycles also support simple programming of processes that previously had to be carried out with special machines, programs and tools.
With efficiency to the Green Transformation (GX)
Integrated processes, automation solutions and digital support promote efficient and resource-saving use of the DM 20 linear and ULTRASONIC 20 linear 3rd generation. The three pillars of the Machining Transformation (MX) thus also contribute to the fourth pillar, the Green Transformation (GX). DMG MORI is increasing the potential for saving energy and resources with the latest 400 V drives, optimized box guide lubrication and a revised air nozzle and air flushing design. The coolant service life has also been extended thanks to a new coolant system.
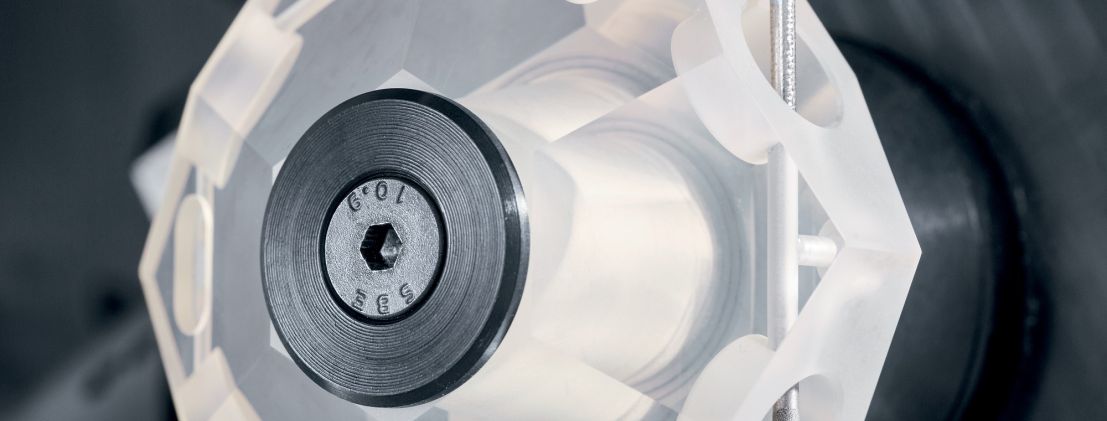