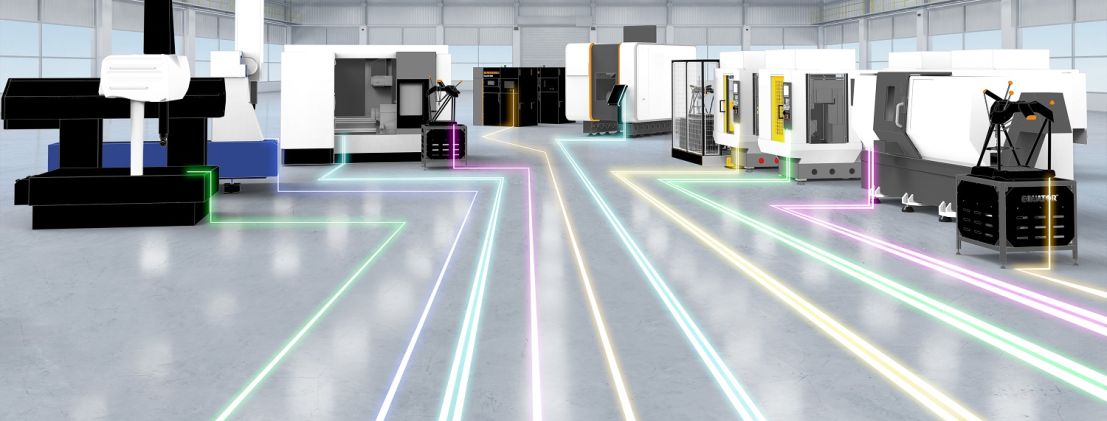
Renishaw showcases smart factory automation at EMO Hannover 2023
Renishaw will demonstrate its new smart manufacturing data platform at EMO Hannover 2023. Renishaw Central is a data-driven solution designed to transform the productivity, capability, and efficiency of manufacturing operations. Bringing the power of connectivity to the machine shop floor, the system collects accurate, actionable data on machines, parts, and processes from across the factory and presents it centrally for insight and interrogation at the point of manufacture.
The Renishaw Central platform provides machine shop connectivity, consistency, control, and confidence. It allows manufacturers to harness end-to-end process data and use it to develop a robust factory-wide system architecture. The platform enables you to monitor and update machining and quality control systems. Manufacturing process parameters can also be updated using its unique and patented Intelligent Process Control (IPC) software functionality. The ability to predict, identify, and correct process errors before they happen supports increasingly automated solutions and processes for long-term productivity, capability and efficiency gains.
"The Renishaw Central concept was born out of our own need to digitalise, visualise and control the manufacturing and measurement processes within our own production facilities. We wanted to reduce assumptions when problem-solving, and facilitate the adoption of automated process control," said Guy Brown, Renishaw Central Development Manager. "Because we live and breathe many of the same challenges faced by our customers, we're confident that we've created a digital solution capable of driving actionable data across machining shop floors everywhere."
Significant improvements in utilisation
Renishaw has used process automation technologies in the manufacture of its own products for over 30 years. During its in-house design and development, the Renishaw Central platform was deployed at Renishaw's own UK low-volume high-variety manufacturing facilities at Miskin and Stonehouse. 69 machines were connected to Renishaw Central, and both sites subsequently reported a reduction in unplanned machine downtime caused by automation system stoppages.
"Collaboration with those working directly with Renishaw Central in the machine shop, including production engineers, and maintenance and operations staff, allowed Renishaw to engineer a product that solves real-world problems. Our original aim for Renishaw Central was to introduce further automation for lathes using our IPC technology, and this is progressing well. But an unexpected and positive outcome has been Renishaw Central's ability to highlight and rank unplanned stoppages of our automation systems," said Guy. "Analysis of this information has guided remedial actions, leading to a 69% reduction in automation stoppages and significant improvements in utilisation."
A global selection of pilot customers who trialed Renishaw Central also confirmed that access to standardised end-to-end data provided an insight into their processes that has allowed them to improve manufacturing performance.