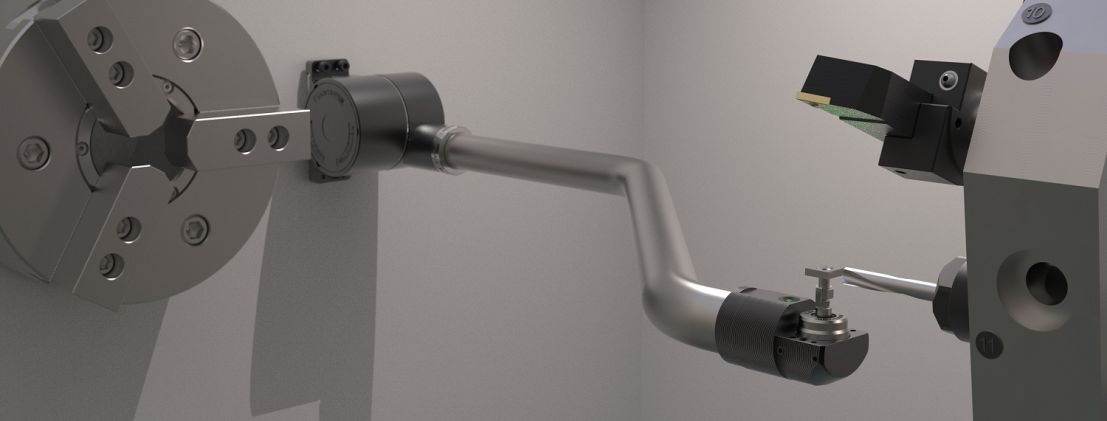
Renishaw reveals extra large tool setting arm for machine tools
Renishaw, will showcase its latest tool setting arm at EMO Hannover 2023. The HPMA-X is the latest addition to the company's family of high-precision tool setting arms and has been engineered to perform in the most challenging turning applications.
Building on the success of the original high-precision motorised arm (HPMA), the latest evolution now brings high-accuracy tool setting and broken tool detection to large CNC lathes. Lathes of this size typically require longer, heavier and more complex arm designs, which can be challenging to move smoothly and repeatably. Such designs are now possible with the HPMA-X due to an efficient and high-performance drivetrain, which includes a digitally controlled brushless motor and high-ratio 3-stage planetary gearhead. This intelligent system allows for precise speed control and collision detection, whilst maintaining high torque and powerful lift capacity.
“Our existing HPMA fulfils those applications which require an arm of up to 555 mm in length. The HPMA-X is targeted at the growing market of larger lathes needing arms over 500 mm and can be designed in many different configurations, up to 1000 mm in length,” said Steve Petersen, Marketing Manager for Renishaw's Machine Tool Products Division. “On these larger designs, our engineers have worked hard to ensure that the probe is presented into the working environment with exceptional repeatability”.
For arms of this size, ensuring a smooth transition as the probe is moved in and out of the working environment is critical in order to maximise the life of the product. Digital control and feedback systems within the accompanying interface (TSI3-X) provide smooth motion control, resulting in consistent acceleration and deceleration characteristics.
Additionally, the TSI3-X interface incorporates four customer-facing LEDs for real-time status monitoring. These indicate the status of the input drive commands and arm confirmation outputs, as well as conveying any motion or system health issues. Petersen continues, “We are seeing more and more manufacturers looking to implement process automation in their factories. Having machines sat idle, awaiting manual tool setting tasks is no longer an option if you want to remain competitive. The HPMA-X provides automated tool setting and broken tool detection on CNC lathes and can enable lights-out manufacturing.”
Productive and sustainable manufacturing
Renishaw's precision measurement and process control technologies, like the HPMA-X, enable productive and sustainable manufacturing. They can predict, identify, and correct process errors before they happen. This helps eliminate scrap and, in turn, reduces the wasted energy, time and materials involved in producing those scrap components. Factory automation drives operational efficiency by increasing machine uptime and overall output, without adding extra machines. Renishaw probing solutions for the automation of CNC machining processes allow manufacturers to increase machine utilisation and operate 24/7. With process automation technologies in place, physical automation can be implemented, which increases productivity and, in turn, can reduce waste and energy consumption.