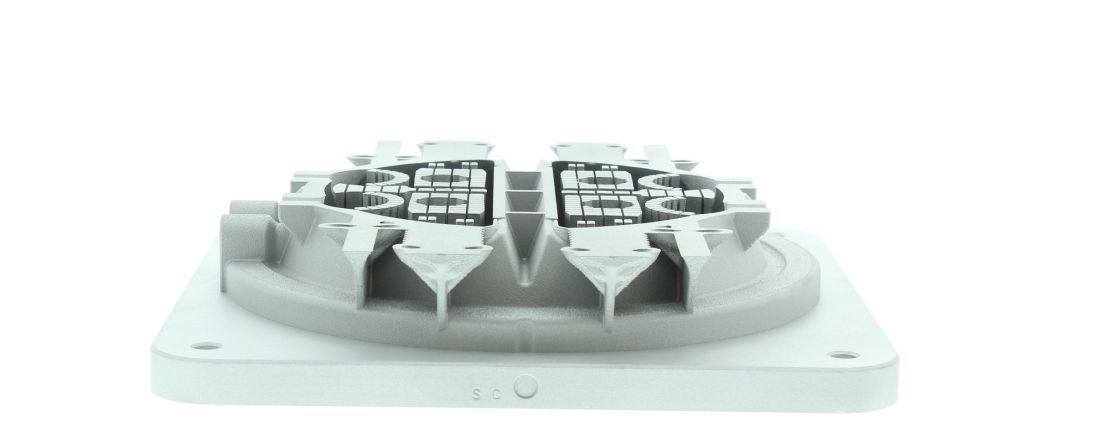
Renishaw RenAM 500Q 3D-prints metal with four lasers
With four 500W lasers, Renishaw's compact RenAM 500Q metal printer delivers much better productivity, while also increasing the quality of manufactured parts. This speeds up the manufacturing process by up to four times, making AM in metal attractive even for applications where it was previously uneconomical, and thus allowing the technology to enter new sectors.
Essential technologies at the heart of the RenAM 500Q are the optical system and the control software. Laser beams enter the system through four channels, where they are dynamically focused and routed to a thermally controlled galvanometer housing ("galvo housing"). Inside the galvo house are four pairs of digitally controlled mirrors, which guide the lasers in such a way that they cover the entire working area of the powder bed.
Stable process environment
Renishaw is an innovator and specialist in creating stable process environments, so is well placed to manage the additional process emissions caused by multiple lasers. An inert gas recirculation system, incorporating a pre-filter cyclone and a gas intercooler, gives the filter a long life and provides consistently clean machining conditions throughout the product build-up. The new system builds on the safety and operating features of the RenAM 500M single laser, and features dual SafeChange filters with auto-switching for minimal manual intervention. Additional studies showed that powder condition is maintained for maximum reuse, further reducing production costs.
Accelerate development
Companies are already experiencing the benefits of the RenAM 500Q. For example, Renishaw is using its AM expertise to help all kinds of companies develop new products. For example, off-road bicycle brand Atherton Bikes is working with Renishaw to additively produce titanium fasteners for the bicycle frames it makes. Using the RenAM 500Q allows the company to produce faster, as parts are developed and customized more quickly to meet the needs of the driver. While traditionally many tools are required, additive manufacturing is an entirely digital process. As a result, fastener parts can be customized in CAD and efficiently reproduced to a high standard.
Note: This article has been partially automatically translated.