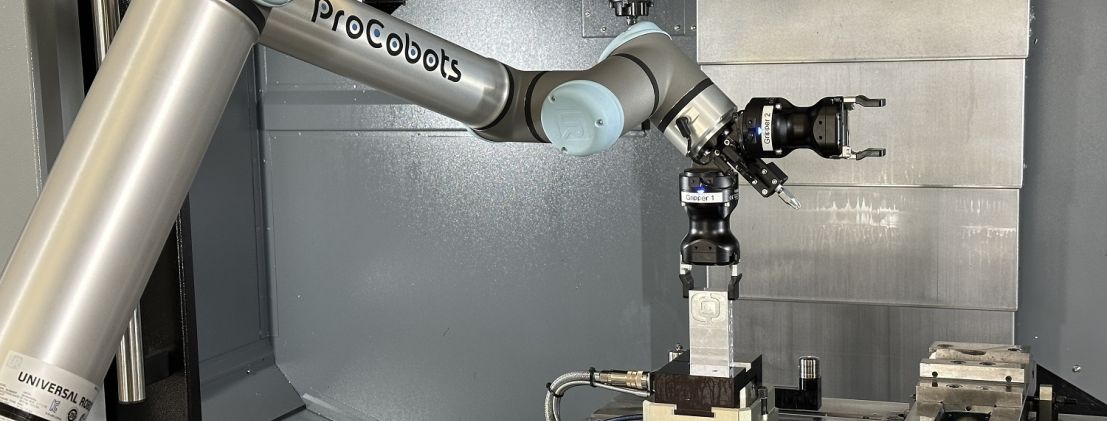
HURCO Handles Components Better with Cobots
HURCO Werkzeugmaschinen presents how easy automated loading and unloading solutions can help to process orders faster. The company is introduced its “ProCobots” automation for machining centers.
Anyone who wants to relieve their machine operators in their task of inserting parts into the ma-chine will find exactly what they need in a cobot. With the ProFeeder, HURCO offers a solution that small and medium-sized companies in contract manufacturing can easily use. The helpful cobots are available as a cart and table design. From setting up and teaching to the use, it doesn’t take long, because the job manager software is fully integrated into the MAX 5 control system of the HURCO machining and turning centers.
“No one needs a degree to use our ProFeeder: Truly anyone can work with it, even if they don't have any background knowledge of robots,” says Sebastian Herr, Head of Application Technol-ogy at HURCO. The cobot is easy to set up and completes its tasks virtually as a third arm. In this way, it gives the operator time for other tasks, such as setup or programming, and Herr as-sures it is “a very attractively priced solution, which can already pay for itself within less than a year.”
The ProFeeder Cart is delivered with two carts. This way the cobot can be loaded from one cart while the other is already being reloaded. Once the first cart has been processed, the carts are changed. The result is that downtimes are avoided. Grid plates are standardized so that the cobot can quickly pick up the components. The ProFeeder Table is a heavy-duty solution for a number of parts, which is why it has a large worktable. This mobile system can alternately load several machines at the same time. The grid plates can be changed here quickly.
Packing where you need it
The ProCobots consist of the “UR10e” robot arm and an adaptive gripping system. As a collabo-rative system, the cobot manages without any special protective housing because, unlike large loading solutions, it can be safely integrated into production. Alternatively, an electronic or pneu-matic gripper is available. The clamping force can be precisely adjusted on the electronic version in order to handle particularly sensitive components carefully. The pneumatic version also packs heavy components up to 6.5 kg into the machine.