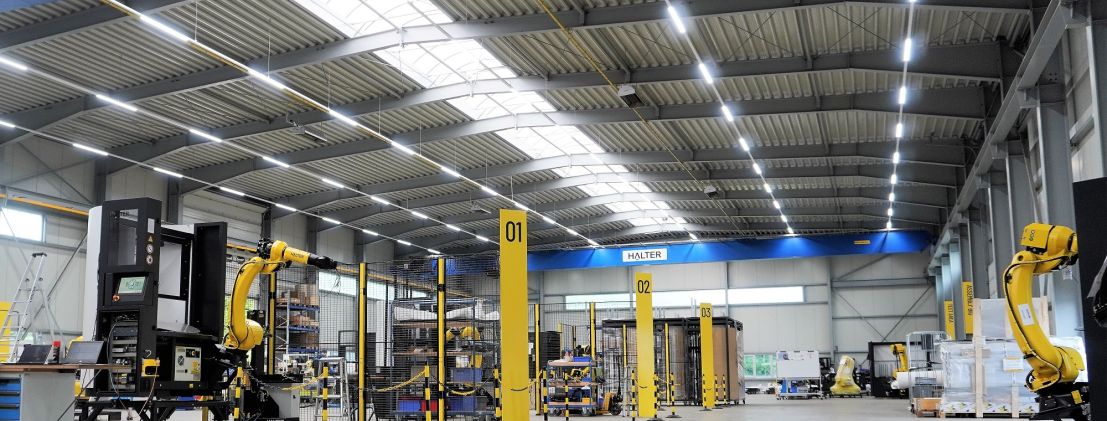
Halter CNC Automation ready for growth in new production hall
Halter CNC Automation has moved into a new production hall in Issum, Germany. The manufacturer of automation solutions had outgrown its premises and therefore moved into a plant with a floor area of 2,500 m2. With this, Halter is completely ready for future growth.
The new Halter CNC Automation premises are now set up for a production capacity of 250 systems per year. Over the last few years, demand for Halter's automation solutions has risen sharply. In particular, the German and American markets are growing fast, according to Halter. "Since the summer of 2021, things have been going fast. Despite Covid and now the war in Ukraine, manufacturing companies are so incredibly busy that they are almost forced to automate. Germany and the United States stand out for us. Both are countries where there is still a lot of serial work and where automation really pays off. If we look at the American market, where we have our own branch office, we can see that automation is now starting to take hold there. That's because the realization has now dawned that there is more to be gained from automation. After all, to get the most out of that expensive machine tool, you have to aim for maximum spindle hours. That's where automation comes in", says Wouter van Halteren, Managing Director of Halter CNC Automation.
Customer-specific automation
All of Halter's automation solutions, including the systems sold in America, are manufactured in Issum. Each system is built in a fixed slot and to order. Even though delivery times have been increased due to certain parts being in short supply, Halter can build an automation solution from start to finish in about two weeks. "The reason we build our systems in Germany has to do with the high-quality German engineering. Everything follows a fixed structure and fixed protocols, so the quality is always good and constant," says Frans Fontein of Halter CNC Automation. Halter took over the complete engineering and production of Fastems Systems in Issum in 2019. As a result, the company can now react flexibly to changes in the market and respond quickly to customer-specific needs. Because despite the fact that Halter has a portfolio of standard automation cells, it is increasingly common for there to be special requirements from the customer. For example, the need to measure workpieces on a measuring machine after machining, or to clean them in a cleaning machine. Thanks to its engineering department, Halter can quickly adapt its cells to carry out these types of operations.
Standard automation systems
Halter has three types of LoadAssistants available in its standard range. The Universal is suitable for turning and milling, the TurnStacker for turning parts and the MillStacker for milling parts. The three systems are available in Compact, Premium and Big versions with a robot arm of 12 kg, 20 kg, 35 kg or 70 kg. The compact was introduced last year, making it the newest member of the LoadAssistant family. The system has a compact design that allows it to compete well with cobot solutions. "An automation system has to be robust and not come to a standstill at the slightest bit. That is often the disadvantage of a cobot. That is why we have developed a cell that is similar in size to a cobot, but has a robust Fanuc robot and all the advantages of a Halter, such as, in particular, short changeover times," says Van Halteren.
For anyone interested in Halter CNC Automation's automation solutions, you can take a look at their systems at both the AMB in Stuttgart and the IMTS in Chicago.