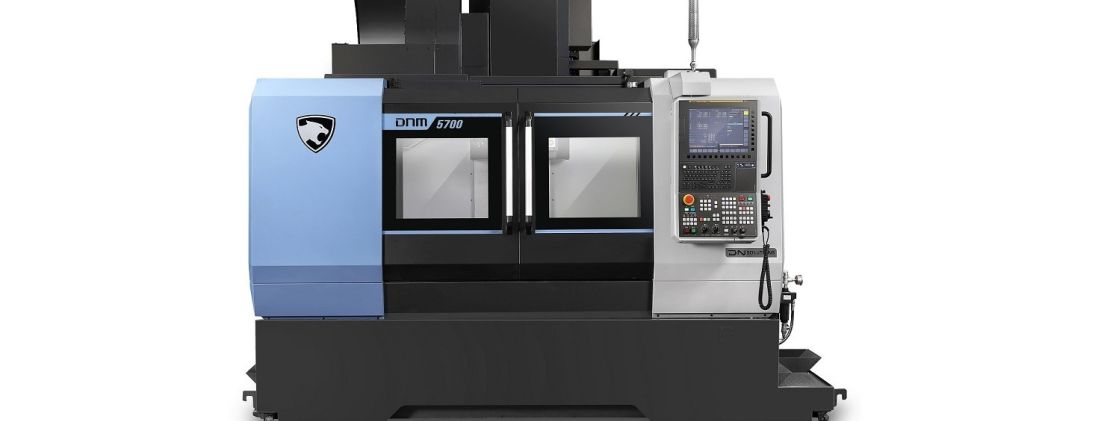
DN Solutions Launched the 4th-Generation DNM Series
DN Solutions has introduced the fourth-generation of the DNM Series of vertical machining centers with enhanced productivity and reliability. The new DNM series is equipped with the third generation of high-speed specification capabilities as standard, greatly improving productivity and reliability. DN Solutions’ development of various advanced options has enhanced user convenience significantly, and design improvements and environmental-friendliness have been realized.
Due to its outstanding performance and productivity, the DNM Series has become the global standard machining center from DN Solutions, which has posted a sales volume of over 50,000 units for a single product. The DNM Series delivers the machining capabilities and quality required by a wide range of industries, including the automotive, aerospace, and energy sectors.
Improved Speed and Productivity
With a large machining area, the new DNM Series enables precise and fast machining of a wide range of parts. LM guides are used to secure the rigidity of the feed system, while the direct-coupled spindle reduces spindle vibration and noise. The line-up features a Y-axis ranging from 400 mm to 670 mm, making it suitable for a wide range of workpieces and workspaces.
In particular, the new DNM Series’ tool change speeds are faster than those of the third generation. The new series integrates improved servomotor specifications and support structures to enhance the axis system's acceleration and deceleration performance, increasing productivity by up to 7.3% compared to the previous generation.
Next-level Reliability
The new DNM Series features thermal displacement compensation as standard to ensure that the machining results never vary whatever the machine's environment. In particular, the thermal displacement of the axis system has been improved by up to two times compared to the previous model, improving machining precision. In addition, the use of a round-type coolant will reduce heat and extend the tool's life cycle.
The new DNM Series also features Programmable Flood Coolant (PFC), which can be selected to automatically adjust the nozzle angle and set the oil cooler operating cycle according to the size of the workpiece and the geometry of the tool. The Automatic Tool Changer (ATC) shutter, which was an option with the third generation, is now a standard feature. It improves reliability by preventing lightweight and fine chips, such as aluminum, from entering the ATC.
Improved Operator-friendly Features
The series’ coolant and chip handling capabilities have further been enhanced. The capacity of the coolant tank has been increased by 20% to prevent downtime due to low levels of coolant and to improve refill intervals. In addition, the location of the coolant pump has been changed to facilitate maintenance. The chip discharge space has been increased by 20% to facilitate the discharge of large chips or large quantities of chips generated during machining. Furthermore, an optional feature is available to adjust the speed of the chip conveyor according to the amount of chips discharged.
The functions of the EZ WORK software, which can manipulate tool operation and machining operations, have also been upgraded. A bookmark function has been added to the Easy Work main screen, and the tool management screen has been reorganized. In particular, the newly added tool call function is expected to greatly improve operator convenience by allowing workers to input a tool number or magazine port number and call a tool, which then exchanges it directly on the spindle. In addition, rear tool storage is possible with other options, and the OP height can be adjusted.
Operation of Eco-friendly Machines
The new DNM series improves productivity and reduces energy consumption by reducing machining times. It is equipped with a power consumption monitoring function as standard, enabling power consumption management and energy saving. Additionally, energy consumption can be reduced by adjusting the speed of the conveyor depending on the amount of chips discharged or by optimizing the operation cycle of the oil cooler for the spindle depending on the tool.
Grease lubrication has been adopted as a standard feature for environmentally-friendly machine operation. The grease lubrication system not only spares workers the inconvenience of having to apply oil frequently, but can also reduce annual maintenance costs by 55% compared to systems that use oil.
Design with Added Usefulness
The size of the front window has been enlarged to enable workers to check the machining situation in real time. The optimal design prevents oil leakage or scattering outside the machine, and additional foot space is provided at the bottom of the coolant tank to allow workers to access the machine more easily.