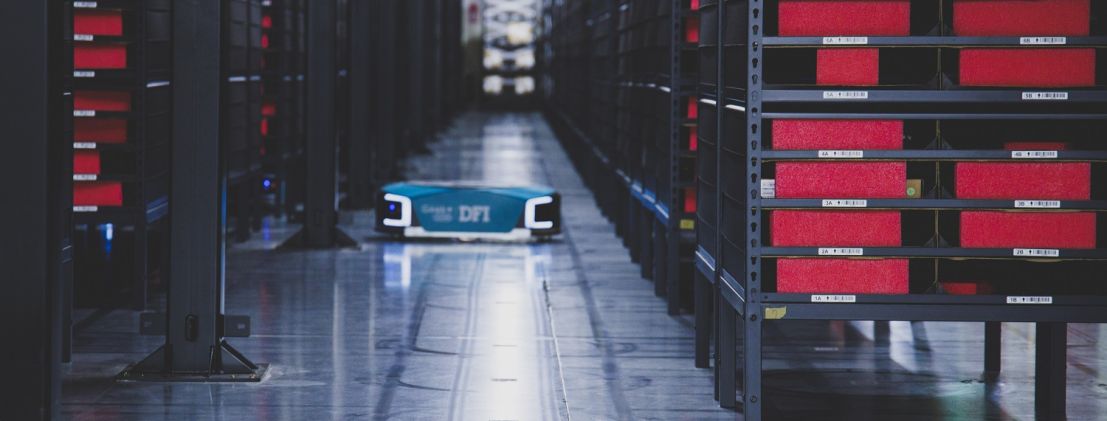
DFI's new smart factory improves production capacity by 30%
DFI, the world's leading brand in embedded motherboards and industrial computers, unveiled its new smart factory and invited the media to tour the plant in Taoyuan. DFI's new facility introduces multiple automated equipment. In addition to efficiency and precision, it features more rigorous manufacturing and inspection processes. Control of the manufacturing process has been enhanced, with output increasing by 30%, material mastery reaching 99.9%, and FPYR (First Pass Yield Rate) reaching 99.6%.
The global pandemic and severe labor and material shortages have recently plagued the international supply chain. Corporate automation and smart production have become keys to increasing future competitiveness. DFI has transformed the Taoyuan plant into a high-efficiency, high-quality, and high-material management smart factory by introducing new automation equipment.
Michael Lee, Vice Chairman of DFI, stated, "a wave of new infrastructure and IoT has swept the global industry in recent years. DFI has accumulated great expertise in the embedded field. We can help customers accelerate their integration of IT and OT to improve the deployment of smart functions to respond to the rapidly changing industrial environment. We will actively face the various impacts of the post-pandemic era and economic changes."
Alexander Su, President of DFI, further shared the company's management approach. "With the trend of corporate digital transformations, DFI will implement comprehensive production and quality management through the three operating strategies of 'smart new factory,' 'AIoT product lines,' and 'flexible and stable supply chain deployment.' We will provide integrated solutions and realize exceptional product performance and stable supply services to create maximum customer value."
The New Taoyuan Plant is the Face of Smartification
Efficiency: DFI has expanded SMT production to 6 lines and has integrated high-efficiency AS/RS unmanned vehicles with an automated smart warehouse system. Results include improved material turnover efficiency by 20% and output by 30%.
Accuracy: An automated X-ray component counter was introduced to accurately count and calculate the number of parts after mounting. The smart feeder provides two pathways of smart confirmation. A production traceability system provides complete material and product traceability, increasing mastery of materials and parts to 99.9%.
Product quality: The correctness of finished parts and production quality is ensured by 2D & 3D automated optical inspection (Pre-reflow AOI/Post-reflow AOI) and X-ray inspection. A wide temperature burn-in chamber conducts aging testing according to customer needs. It can satisfy the tolerability required by various key applications, with an FPYR of 99.6%.
Creating ultra-small products and high flexibility, high stability supply chains
In recent years, DFI has actively invested in the research and development of ultra-small motherboards and fully invested in developing Edge AI-related products. We have expanded the deployment of vertical applications, such as industrial automation, Internet of Vehicles, and medical solutions. The supply of high-quality products requires a firm yet flexible supply chain for support. DFI has created a stable supply chain by enhancing smart production management capabilities.
DFI's Taoyuan smart factory has successfully integrated the IT and OT systems. The production line's efficiency, accuracy, and quality have been enhanced. Hybrid cloud architecture has been established, and the connectivity and correctness of the information system have been improved. Sufficient production capacity and strong performance will drive the company's implementation of OT smart transformations.