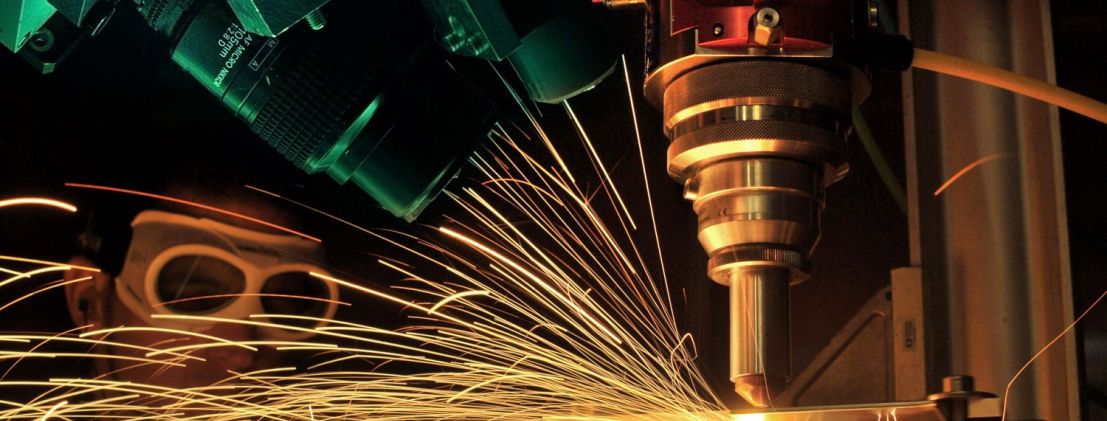
Laser machines with brains learn something new every day
Nowadays small- and medium-sized enterprises (SMEs) can afford lasers, but they often lack the capacity and know-how to optimally fine-tune them, especially when applications change frequently. The BMBF joint project DIPOOL, in which four industrial companies and two research institutes are jointly developing two demonstrators for laser cutting and laser welding, is focusing on laser machines with brains. Technology reporter Nikolaus Fecht learned about the role played by AI and minimally invasive modulation technology from Dr. Dirk Petring of the Fraunhofer Institute for Laser Technology ILT in Aachen.
An expert in the laser community once mockingly said, “If you can't afford physicists with PhDs, you can never use a laser efficiently.” On your institute's website, you talk about laser machines with brains. To what extent can they replace the expertise of specialists, Dr. Petring?
Dr. Dirk Petring, group leader of Macro Joining and Cutting at Fraunhofer ILT and scientific coordinator of the joint project DIPOOL: “First of all, your quote from an expert is certainly more than 20 years old and has long since ceased to be valid. In the meantime, we are on the path from automated to autonomous laser machines. The focus is entirely on the use of artificial intelligence (AI) because it can increase the autonomy and functionality of machines to an unprecedented degree. AI that has been well-trained by experts detects system deviations, errors and quality defects faster and more reliably than classic monitoring and control systems. AI can analyze sensor signals for more extensive pattern characteristics and even those previously unrecognized by experts.”
The joint project is creating a digital process online optimizer for intelligent laser machines, or DIPOOL for short. What is Fraunhofer ILT contributing, who is supporting it?
Petring: “We are combing one of the unique characteristics of laser tools – that they can be programmed and controlled temporally and spatially – with machine learning, or ML for short. Specifically, our work is about automatic and robust monitoring, quality assurance and optimization of laser machines for changing manufacturing tasks. DIPOOL aims to demonstrate, for the first time, the advantages of integrating machine learning for the two laser manufacturing processes with the highest turnover worldwide: cutting and welding. Apart from laser manufacturers, all industries that process sheet metal will benefit from the results. We are strongly supported by the Karlsruhe Institute for Industrial Information Technology IIIT, who masters the fundamentals of efficient signal analysis for machine learning. Finally, experts from Marx Automation are implementing the trained ML algorithms in the so-called inference system of the laser control.”
Machine learning sinks or swims with the data: What technology is being used to collect it?
Petring: “Among other things, a completely new, multispectral sensor system from 4D Photonics. We hope it can be applied to increase the information content of the process signals that can be used with ML, especially in laser beam welding. The smart system technology and sensor technology for laser cutting systems comes from Precitec. Its latest generation of laser cutting heads will be equipped with sensor technology and data interfaces developed specifically for the AI software and the DIPOOL approach.”
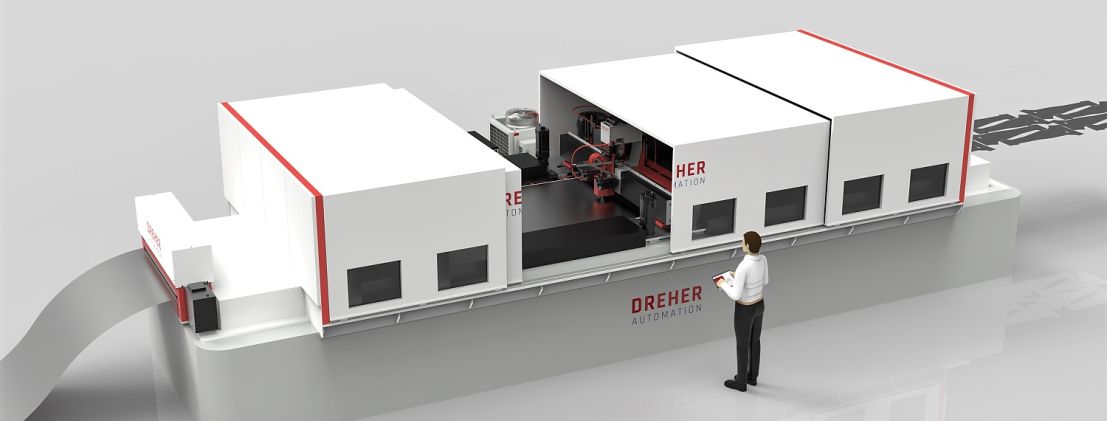
Who is testing the technology in demonstrators?
Petring: “The company Automatic-Systeme Dreher is using it in its demonstrator for high-speed laser cutting of shaped blanks from a running sheet-metal strip. In this test system, our new, intelligent ML-supported algorithms will be used to monitor the cutting process, automatically adjust it in the event of deviations, thus ensuring the required cutting quality and productivity with closed control loops. Laser service provider LBBZ is using the same digital optimization technology in a robotic laser cell to demonstrate how 3D welding can be improved.”
How do you improve processes with AI?
Petring: “It's about interpreting sensor signals from the process and drawing conclusions about the process status. What process status do we have right now and do I need to change something in the system? Is the seam only partially penetrating the joint or completely welded through it? Is the high-speed cutting process operating at the optimum speed? So, like a closed-loop control system, the inference engine has to make a decision. The goal is to recognize signal patterns. However, we don't use the raw data for this, but condense it before it is processed further by the AI with algorithms that we have already developed based on our domain knowledge of the process.“
How do you proceed from there?
Petring: “The process is called feature engineering: We don't feed the AI with all the process data, but with intelligently prepared data. The trick is to find the best compromise between data quantity and data quality because you can also overtrain a system in a machine learning environment. If the trainers overdo it with too much data, then the AI will only learn by rote. And, as soon as data deviates from what has been learned by rote, it is overwhelmed and can no longer make a sensible decision.”
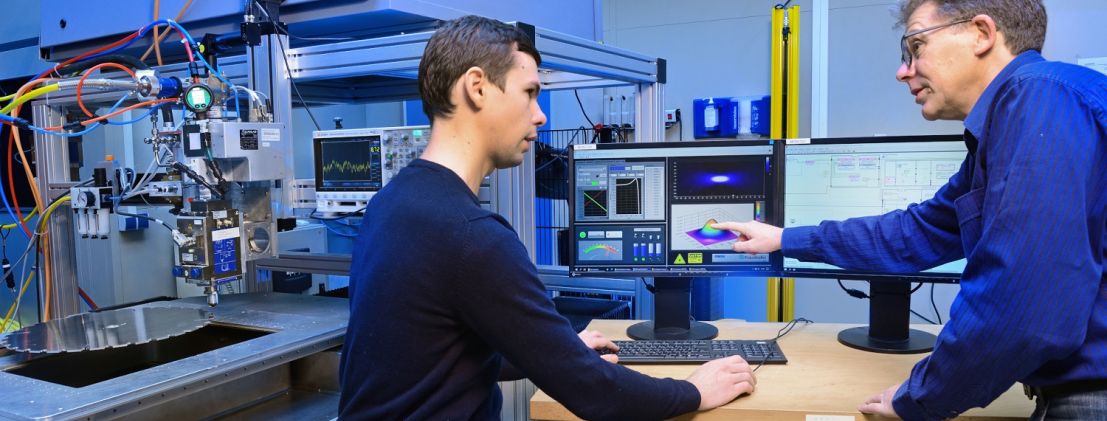
How do you ensure data quality?
Petring: “We don't constantly unleash the laser power on the process, but modulate it minimally. We periodically change the power very slightly and see how the process responds. To do this, one would ideally assume linear response behavior and build control loops on that. Unfortunately, this does not work for laser material processing because we are dealing here with strongly nonlinear processes. The processes react comparatively “sensitively,” but also quickly to parameter changes. Accordingly, the process signal response also changes quickly depending on the process status with a characteristic signal pattern. We and, in the future, AI will exploit this, for example, to recognize in real-time whether the control system can increase the cutting speed even further or should perhaps even reduce it somewhat in order to achieve optimum cutting quality. Without this modulation technology, only the signals of a so-called unquestioned process are generated, which can quickly be misinterpreted or not interpreted at all. This is why the integration of process monitoring in industrial laser machines has failed very often in the last 30 years.”
So the goal is to increase the reliability of interpretation?
Petring: “Exactly. At the moment, we are therefore primarily focusing on supervised learning in the DIPOOL project: We are testing the response behavior with minimally invasive laser modulation (MILM). With it, we obtain characteristic signals that are easier to interpret. In supervised learning, we thus train the ML system, usually an artificial neural network, to draw the right conclusions from the signal patterns and to initiate appropriate measures if necessary: They can range from instructions to the plant operator all the way to the automatic adjustment of process parameters. The trained “model” is then integrated into the plant control system as a so-called inference engine.”
Which sensors do you use?
Petring: “For example, multispectral sensor technology with different wavelengths, which is being developed by 4D-Photonics. Additional information can be derived from the different signal heights at various wavelengths. The broad color spectrum is comparable to a dynamically changing rainbow, which AI is predestined to evaluate. For laser beam cutting, Precitec specifically addresses the boundary conditions in a 2D flatbed cutting system during sensor development. Compactness and, above all, robustness of the solution are top priorities, in addition to the highly dynamic acquisition of the process responses.”
Do you see any chances of convincing small- and medium-sized companies of these solutions?
Petring: “Today, a system of this type can also be implemented for SMEs because the prices for laser and computing power have fallen significantly. Virtually all manufacturing companies are now under constant pressure to innovate – not least from competitors in China. This increases the willingness to invest in innovative technology. In addition, the process understanding for AI systems is also growing among medium-sized companies.”
Please give us an assessment. How much more efficiently can companies cut or weld with lasers thanks to AI control?
Petring: “That's a simple question, but of course it can’t be answered universally. Nonetheless, I roughly estimate that the overall equipment effectiveness (OEE) can be increased by 25 percent.”
The DIPOOL project will run until summer 2024. Is there already an end user in sight?
Petring: “Yes, the BILSTEIN GROUP has even set up its own subsidiary BILCUT in Hagen specifically for this purpose, which will be cutting shaped blanks for the automotive industry at high speed starting in 2025. DIPOOL project partner Dreher will build a laser cutting system based on the technology we have developed. This will enable BILCUT GmbH to supply individually designed blanks with excellent economic and ecological performance.”