"As things stand at present, the degree of digitalisation at shop floor level is still extremely low and, if at all, it is characterised by isolated solutions." This statement by a participant in a survey of exhibitors at this year's AMB shows the perception of the basic degree of digital maturity in the metalworking industry. The following comment is still heard too often in the mechanical engineering and plant construction industry: "It's only a question of time before a breakthrough..."
Despite the obvious caution of many users and failed attempts to create digital platforms, the topics of Industry 4.0 and Ilot are not unknown subjects in the mechanical engineering and metalworking industries in 2024. Everything needed to tackle modern concepts is available. OPC UA or Umati has existed for years as an adapted, universal machine tool interface. 5G campus networks are available as an efficient private mobile radio standard for networking machines and systems. Know-how is also available. Just one example: control technology suppliers such as Fanuc, Heidenhain and Siemens have long shown through daily use in related manufacturing industries what benefits are possible with digitalisation. It is therefore not surprising that many participants in a survey of AMB exhibitors also emphasised the topic of digitalisation. At this year's International Exhibition for Metal Working in Stuttgart, they want to prove that integrative digitalisation approaches are now already a must – especially for software suppliers.
Become more resilient with digital business models
The company Evomecs Maschinen, which was founded in 2015, now networks systems and processes in a non-branded way regardless of the location. The Munich-based company regards itself as a driving force behind digitalisation in order to counter the increasing rationalisation pressure, the growing shortage of skilled workers and intensive international competition. Those companies which have already managed to initiate the right measures would be more successful in future as production companies, but also more resilient since they can extend their value-added to digital business models.
The Evomecs software integrates all relevant elements of a metal cutting company, for example, ERP systems, CAM systems, tool presetters, tools, workpieces, warehousing systems, CNC machines and manual workstations. The ecosystem thus produced generates a large volume of high-quality data for a company's own production processes. According to Evomecs, this data can also be used, in principle, to develop data-based or data-driven business models.
Manufacturing companies must produce ever faster and more and more efficiently. Enormous expenditure for communication, administration and documentation is incurred, especially when manufacturing small unit numbers. This expenditure may also lead to expensive mistakes and damage in production and requires a high degree of expertise throughout the entire production process. Evomecs is convinced that companies should optimise, automate and therefore also digitalise, especially given the increasing shortage of skilled workers.
Evomecs software can be used to create a valuable data store which may form the basis, in principle, for a wide range of applications such as artificial intelligence. Users can generate production information which could be utilised to optimise processes. The Evomecs employees in Munich are currently working on concepts which enable data analyses, process optimisations and planning forecasts, but also voice input-based control of production for instance.
Fast product launches with simulation
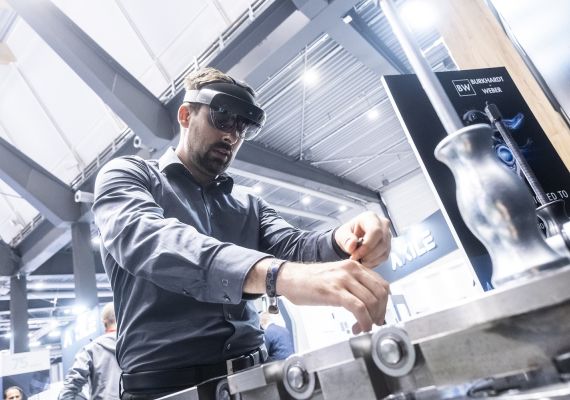
In the centre of a machine, in the metal-cutting process itself, there is also great optimisation potential with digital solutions. Modellings and simulations optimise operation at a later date, enable higher cutting speeds and feeds, and ensure a longer tool service life. The CAE supplier Third Wave Systems provides virtual test environments which lead to fewer downtimes and make trial and error tests superfluous.
During AMB 2024 the company will present technical innovations which substantially shorten market launch times. Visitors will be able to experience how a virtual iteration, compared with tests on the machine, significantly reduces both the number of tests and the number of errors. This leads to a sound design for manufacturing process with the emphasis on "first time right". According to the company, the lower amount of work needed for manual reworking enables machine running times to be reduced by 50 per cent.
However, the challenges for users still include a broad understanding of the strategic motives to achieve the necessary change in the way of thinking to a smooth flexible simulation technology. In the end, said the company, material-specific modelling and simulation technology is worthwhile. The American company is already receiving this feedback from the aerospace industry, the automobile industry and the orthopaedic medical technology industry.
Tool management
Digitalisation is also part of the daily work routine at Grob-Werke. According to the company, the focal point at this year's AMB will be the digital tool cycle. This is extremely relevant to meaningfully tackle increasing production costs. The responsible department of the family-run company from Mindelheim is therefore focusing this year on the automation of tool-related processes. Thanks to a large number of cooperation agreements with manufacturers of tool management systems and presetters, Grob offers users the opportunity to attain substantial cost savings in relation to metal-cutting tools. The underlying solution is called GROB4TDX which enables digitalisation of the tool cycle throughout production regardless of the machine manufacturer. According to the company, this is an essential step towards inexpensive and resource-conserving production.
Increase both efficiency and productivity in CNC machining
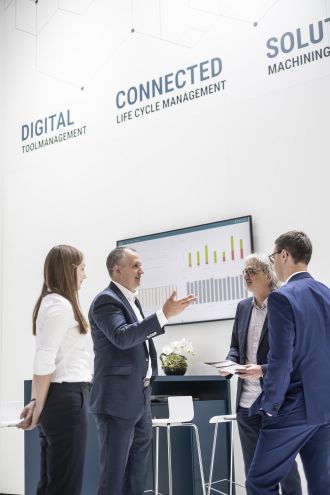
Another machine manufacturer also emphasises digital innovations besides hardware. MTE Deutschland produces bed-type milling machines and travelling column machines. The SBM 8000 rigid bed-type milling machine will be presented at AMB in Stuttgart. It is so called because the rigid table mountable over the floor ensures high basic stability. However, the Montabaur-based company says that there is another reason for one important step towards digitalisation: this machine is equipped with the latest Heidenhain TNC 7 control unit. A technology which offers functions to significantly increase both efficiency and productivity in CNC machining. Since CAD/CAM data is smoothly integrated, the programming of workpieces becomes faster and more precise. Intuitive multi-touch operation and the graphic user interface make it easier to operate the machine and improve the user experience considerably. The TNC 7 control unit also features several smart functions, for example, automatic workpiece probing and graphic support when adjusting clamping devices. These functions simplify the set-up process and optimise work processes. According to the supplier, the results are higher efficiency and more precision.
Perform preparatory work and save time
The Siemens Group is focusing again on the company's production halls: replacing machines during production may lead to bottlenecks and delivery delays with good capacity utilisation. A situation which causes problems for some production managers: a new machine with greater capacity and higher performance is required as soon as possible, but there is no time to replace it. That's because hundreds of CNC programs often have to be transferred from old to new control units, including those of the same manufacturer. Siemens engineers asked themselves how production can be continued when an existing machine is replaced, if possible without interrupting the production process. The offline programming tool SinuTrain from Siemens provides a solution in this respect. This "virtual CNC" acts exactly like the real CNC in the machine: the same Sinumerik Operate version functions here like in the corresponding future machine with the same machine data from the real machine. The consistency and syntax of the CNC programs can therefore be tested in the best possible way beforehand.
The SinuTrain user also has the same CNC editors as in the machine. The operating and programming know-how of the specialists on the shop floor can therefore be used for work preparation. Consequently, the new machine corresponds from the first day onwards exactly to the behaviour of the virtually prepared machine. A solution which would not be possible without the digital twin.
Permanent monitoring of stocks
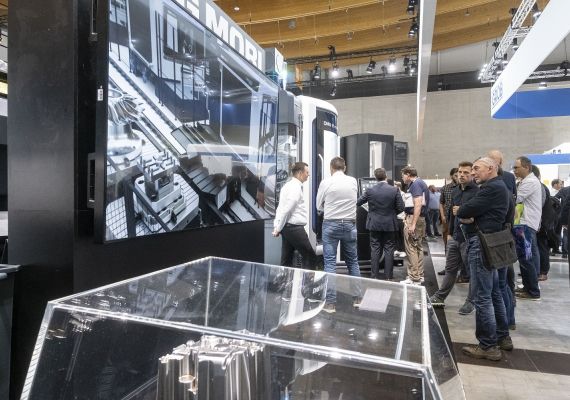
Software solutions also optimise the order process for materials which are to be processed. Bikar Aerospace is one example: since 2016, the company has acted as a metal service centre for the aerospace engineering industry. All services relating to material procurement, preparation and delivery are offered from a single source. The objective is to offer the fastest possible reactions to users' material call-offs and planning. A contract monitoring tool supplies real time data relating to stocks and enables a continuous comparison between the goods required at individual locations with the stocks at Bikar. This forecast monitor ensures a secure overview of the supply chain at all times. Users can therefore react promptly to uncertainties on the world market. The objective is to smooth the way to the digital future of the metal trade through the development of own software solutions and intelligent networking of systems.
Digital concepts at AMB
These examples with different approaches towards digitalisation of the metal working industry show the broad breadth of the market despite some reticence. This will also become clear at this year's AMB, which will be held in Stuttgart from 10 to 14 September 2024. Digital concepts will be a recurrent theme at the exhibition and will network machine tools, their control units, automation solutions relating to machines, embedded measuring systems and collaborative robotics. Digitalisation is therefore driving the industry forward on the road to producing more sustainably and more efficiently, and also competing internationally.
Planning to Visit AMB? Get 50% Off with Our Discount Code!
Use code 24SPAENER50 to enjoy a 50% discount on all AMB tickets. Purchase your discounted tickets here.