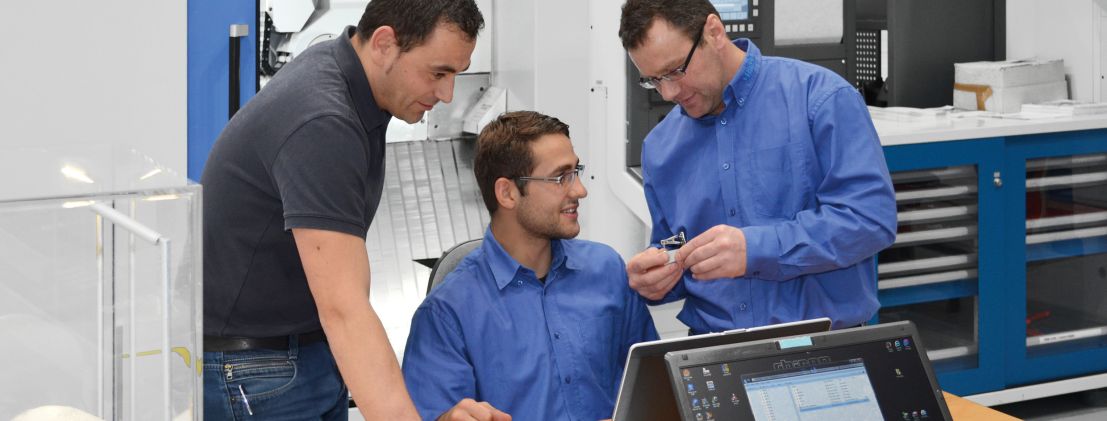
Chiron thrives in machining medical implants
Every year, more than 400,000 artificial knee or hip joints (endoprostheses) are implanted in Germany. The tendency is rising – a growing business. In a worldwide comparison, this figure far exceeds the average, but other countries are also experiencing rising numbers. The challenge for the manufacturer of prostheses and implants to deliver quality goods is getting bigger because of the traceability to the manufacturer that is now the rule. Goods of inferior quality can quickly lead to unpleasant consequences.
Efficient and secure processes are essential
How long an artificial joint lasts depends on many factors. Doctors usually don‘t dare to give a prognosis for individuals. But there are empirical values: according to statistics, an artificial joint art lasts about 15 years. In biomechanics laboratories such as that belonging to the University Hospital of Heidelberg, joint prostheses are stomped hundreds of times on metal trays and subjected to other stress tests. The durability and compatibility of the implants are tested. Dilapidated implants can often be found. The worst case, however, would be a prosthesis breaking – in the hip of a patient. To prevent this, the manufacturers of implants, which are to be regarded as long-term and surgically invasive and thus belong to risk classes IIa or IIb, are facing ever greater challenges. In addition to product development and the appropriate material selection, the manufacturing process of high-quality and innovative implants comes increasingly into focus. Efficient and secure processes are essential.
High-precision machining centres
Chiron offers high-precision machining centres for medical technology. That alone, however, does not guarantee process reliability in production. CHIRON engineers and technicians with medical-technical backgrounds develop top products and processes in the in-house Medical Technology Center in cooperation with the customers. Test processing, tests of clamping means and tools are daily routine, just as the tests of material behavior. In this way, the quality of processes and products is already verified in advance. This adds security and saves costs. With Chiron, you are in good hands.
Medical & Precision Technology Center
Chiron engineers and technicians with medical-technical backgrounds develop top products and processes in the in-house Medical Technology Center in cooperation with the customers. Test processing, tests of clamping means and tools are daily routine, just as the tests of material behavior. In this way, the quality of processes and products can already be verified in advance. In addition, the best solution for the customer can be developed with the users at an early stage.