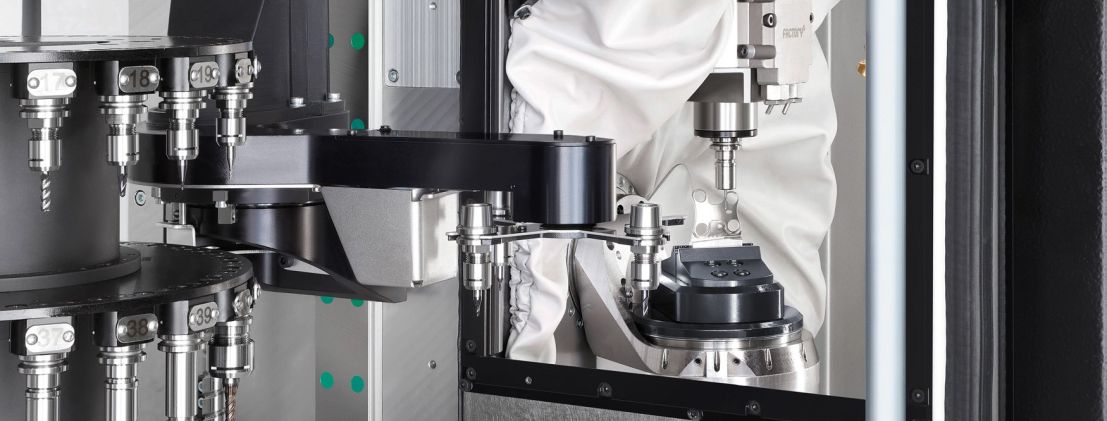
Chiron Group Highlights Future-Ready Manufacturing at AMB
In manufacturing's dynamic landscape, adaptability is key, particularly in machining where innovation is crucial. This September, the Chiron Group will spotlight this need for forward-thinking strategies during the AMB in Stuttgart. Here Chiron will debut the FZ19 S five-axis machine, the hallmark of its new 19 series, emphasizing their commitment to advanced manufacturing technologies.
Which strategies and technologies are successful today and in the future for optimally manufacturing a workpiece in terms of quality, productivity and unit costs? What process solutions does medical technology need? What is the future for the automotive industry? Bernd Hilgarth, CSO of the Chiron Group, draws this conclusion from the developments of the last five years: "Our industry has always been able to cope with unstable economic and political conditions and has emerged from them stronger than before. That is why it is particularly important now to revive strong and recognized values such as product quality, cost-effectiveness and innovative strength. Our customers - and we as manufacturers too, of course - need solutions that will enable us to hold our own in global competition and stand out positively. We can only achieve this together. AMB, with its concentrated knowledge in one place, is the opportunity to talk to each other and find solutions."
Automation is still rising
Five years ago, one in three turnkey machines came with automation as standard; today it is seven out of ten. For Thomas Marquardt, Head of Automation at the Chiron Group, there are two reasons for the high demand: "On the one hand, there is the concern about finding the 'simple' operator, someone who also works in the 2nd and 3rd shift, and on the other hand, the fact that customers see the greatest potential in process automation to improve quality and productivity and thus keep unit costs under control. It is crucial to know what the solution should be able to do to achieve the goal. How much standard is possible and how much individuality is needed on top." The Automation and Application team, which has grown to over 30 employees, has a wide range of products at its disposal: integrated automation on MT centers, extensive standard automation from the Variocell range, highly autonomous stand-alone solutions and interlinked system solutions. Automation solutions for micro-machining and series production on twin-spindle centers will be on display live at AMB.
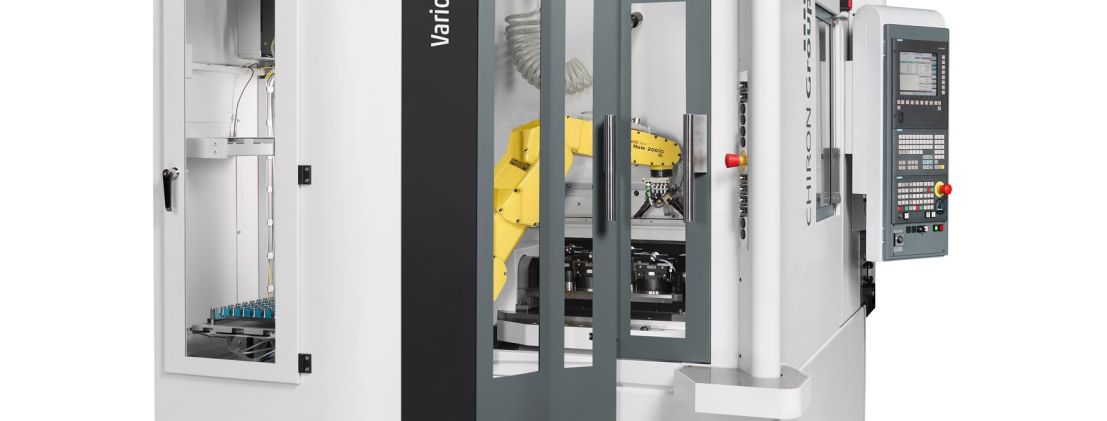
Resource-efficient micromachining
Micro-machining is not a new technology, but one that has really taken off. Why should components just a few centimetres in size be produced on machines that are basically oversized in terms of footprint, mass and energy requirements? Bone plates for hand surgery, dental technology, instruments, special complex custom parts and prototypes and, of course, parts from the watch and jewellery industry are among the target workpieces of resource-efficient and ultra-precise micromachining. A micromachine such as the Micro5 is adapted to these "small and fine" products and, with just 0.5 kW on just 1 m2, has clear advantages in terms of energy efficiency and footprint. In combination with Feed5 automation and an AGV, the Micro5 can be experienced live in Stuttgart and is worth seeing for all those who "micro-machine" their parts and are thinking about the future, keyword reporting obligation in accordance with the Corporate Sustainability Reporting Directive (CSRD), which comes into force in 2026.
World premiere of the 19 series
The FZ19 S five-axis celebrates its world premiere at AMB and is the highlight of the machining show. "We are in pole position with the new 19 series," says Markus Vollmer, Senior Product Manager, full of conviction. He bases this on results from user experience during the test phase, namely the series production of forged steel parts: "The 19 series is a good 25% faster from solid material and when machining complex workpieces." According to Vollmer, arguments for the versatility of the new series are the optimal design of the work area in relation to the workpiece dimension and the Chiron Group's spindles for high-precision and dynamic machining in aluminum, steel and cast iron. At the AMB, components from the energy and aerospace sectors will be machined and a "heavy duty" performance part will be machined to show how stable and dynamic the FZ 19 S five-axis mills are - which of course also applies to turning operations. For Markus Vollmer: "the complete "Series 19" package opens up new perspectives for users to design their manufacturing solutions precisely, productively and reliably."
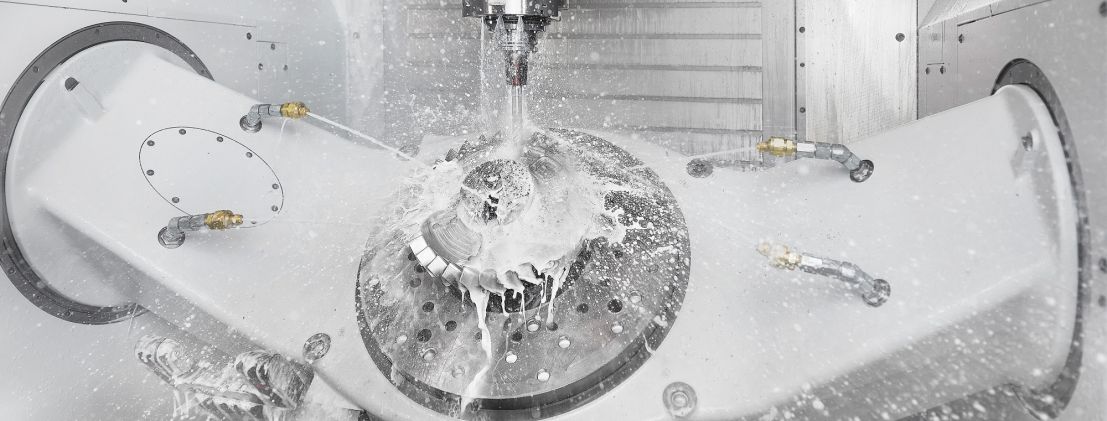
All-round machining centers
This is true for machines, but also for the many manufacturing companies that specialize in contract manufacturing and face a wide variety of challenges. The machines in the 15 series are among the most versatile in the product range in terms of parts spectrum and sectors; since 2000, a 15 has been put into operation on average every second day. The next generation of the 15 series is controlled by the new Sinumerik One and all digital systems from the SmartLine program can be used to their full extent. The RTA200 rotary table for "light" 4-axis machining of aluminum, for example, is also new. It is wear-free and requires only 0.4 s instead of the previous 0.9 s for 0°/180° positioning. At the trade fair, a DZ 15 with Fanuc 31 iB5 control will be used for 4- and 5-axis machining, double-spindle and with Variocell automation.
Integrated gear-cutting technologies
Another new feature is the integration of all gearing technologies into the MT 715 series in collaboration with Paul Horn and Saacke. Every year, 1 billion gears are manufactured worldwide. For prototypes and series production, the MT 715 with gear-cutting technology is a reliable alternative to specialized gear-cutting machines for the complete machining of parts. Users receive a complete package comprising machine, tool and technology cycles with input screens.
"During the five days of AMB in Stuttgart, the Chiron Group, with its machines, technologies, solutions and a trade fair team of over 60 people, will be meeting the challenges of interested parties and our customers in the production of the future and, Bernd Hilgarth is certain, "together we will also find the right future-oriented solutions."
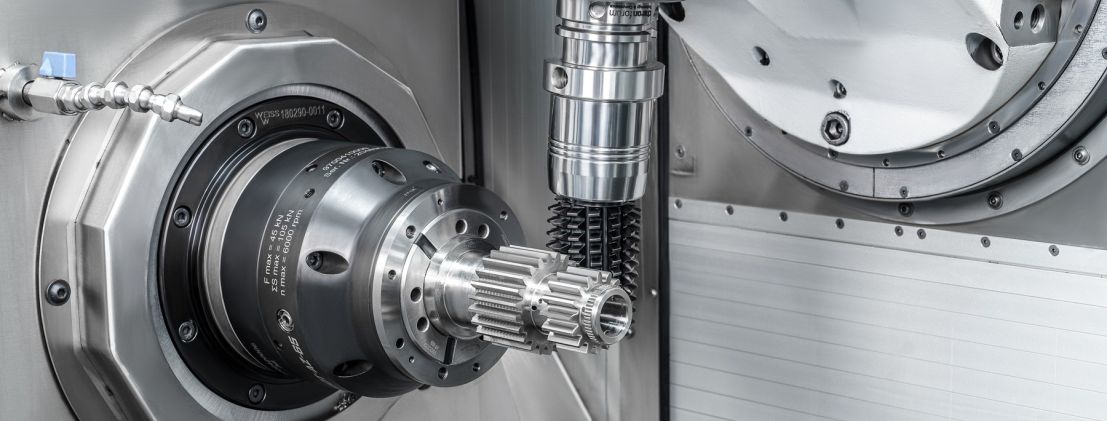