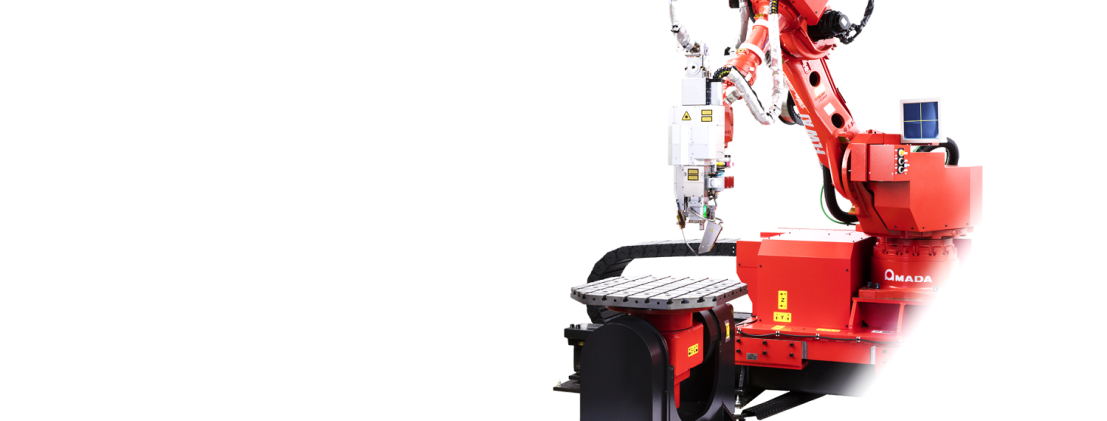
Amada fiber laser welding technology for precise, high-speed welding applications
Amada Miyachi Europe announces that it will highlight its highly precise fiber laser welding technology at EuroBLECH 2016. Experts will be present on the stand to discuss the benefits of fiber laser welding for applications in the Automotive, Electronics & Solar Cells, IT & Multimedia, Medical, Aerospace and Defence industries. In addition, the Miyachi EAPRO Jupiter Fibre Laser Welding System and the AWS3 Active Welding System 3, an integrated resistance welding solution, will be on display in the stand.
Continuous-wave CO2 welding lasers have limited accuracy and undesired high heat input into the weld, while pulsed Nd:YAG laser welders are limited in terms of maximum welding speed, minimal spot size, and electrical to optical energy conversion efficiency. For the growing number of applications that demand higher precision control, lower heat input, and lower electrical energy consumption than are possible with these traditional laser welding technologies, Continuous Wave Fibre Laser Welding is a superior solution.
In a fiber laser welding system, the laser light is generated in an active fiber and guided to the workpiece by a flexible delivery fiber. The flexibility of the delivery of this laser beam ensures maximum quality in end products and highly efficient production. Fibre laser welding enables a number of materials processing applications such as welding of very small parts and fine structures, medium power fine metal welding at high speed or with single-mode lasers, and high power laser welding of metals.
The AMADA MIYACHI EAPRO Jupiter Fibre Laser Welding System, to be on display at the show, is designed for fast, accurate and reliable welding. The fiber laser’s power level and high beam quality allows power up to 700 W to be fired into very precise weld spots.
The AWS3 Active Welding System 3 is an integrated resistance welding solution that provides process control, monitoring, and quality analysis. Available in either servo-motorized or pneumatic versions, the AWS3 can be used alone as a benchtop system or easily integrated into a production line. The AWS3 features modular components that offer maximum flexibility and is ideal for use in resistance welding of connectors, switches, cables, engine components, dashboard electronics and lighting components, as well as batteries, solar cells, and medical components.