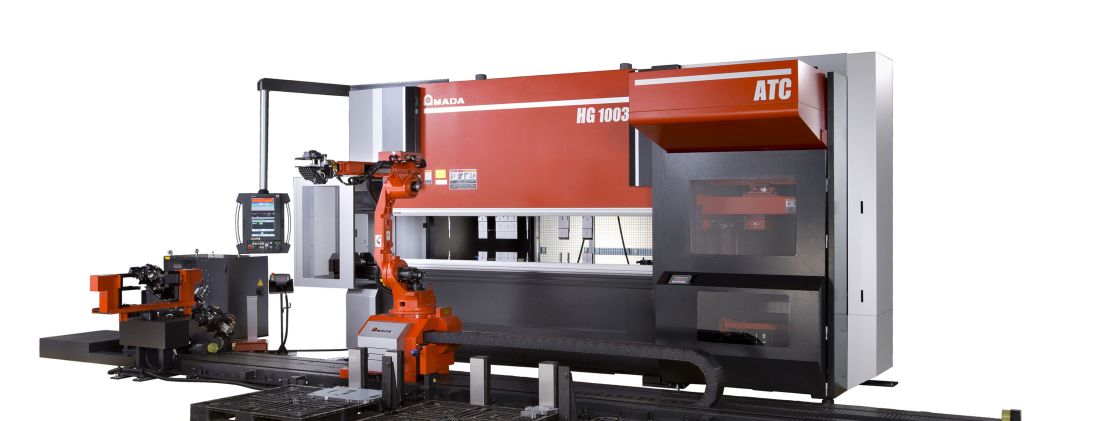
AMADA presents new bending features for higher productivity
Forming and, more particularly, bending metals is an essential step in the production of mechanical assemblies made from sheet metal. As well as the demand for increased precision, bending accuracy and the integrity of the metal surfaces, this procedure requires plenty of physical effort and, until now, frequent manual intervention. These various tasks have an extensive impact on operator safety and speed of execution and they end up impacting the productivity and profitability of a business. Amada incorporates these process-based factors into its research and development. At EuroBlech 2016, you can see how Amada focuses on all these ‘dimensions’ in its bending solutions.
European legislation imposes safety conditions on the operation of machines, which stipulates a reduction in the speed of moving parts that put the operator at risk. Amada has tackled this point to develop a solution to remove the risk factors linked to these moving parts while retaining maximum productivity rates that exploit top machine speeds. The solution drastically cuts down the loss of time between bends, when the operator has to wait for the positioning stops to move into place. We have recorded time savings of around 12% on a ‘fast’ machine, based on the production of one piece with seven-folds. There is even an impressive 36% time-saving to be had compared to another commercially available model processing a comparable part.
The “trick” that makes this happen has a name: FAST (Finger with Active Security Technology). These new stop fingers that can be fitted onto Amada bending machines have an active safety device built in that limit risk to operators if they come into contact with moving parts, even at full speed. This safety feature and “productivity provider” will be introduced and explained at EuroBlech 2016 on the HFE 3i 1003 machine exhibited on the stand. This machine will be equipped with the new generation of AFH tools and of course, will be connected to the relevant software VPSS3i BEND, which both contribute to the productivity of this solution pack.
Higher productivity is also a question of ergonomics
Some essential tasks on bending machines can be dangerous, like feeding in large sheets of metal. Similarly, loading and working with bending tools also poses a risk; it also takes up a significant amount of time, which affects the productivity of the equipment. Amada’s HG-ATC machine offers unrivaled results. We have recorded time savings of more than 50% when automatically loading tools, compared to other commercially available machines, sometimes even soaring to nearly 80%. In light of these results, it is easy to see why the HG-ATC has won over so many users who have, in turn, increased their customer base. This machine will be presented at EuroBLECH 2016 in its latest version, HG 2204 ATC, which can now be equipped with SF75 sheet followers. These make it easier for the operator to handle larger parts. As well as reducing the time it takes to change tools thanks to the ATC (Automatic Tool Changer), the safety and comfort of operators using this highly productive machine are now significantly standalone machines.
Higher productivity goes through logistics as well
Automation and robotisation lighten the load for operators, enhance productivity and increase production rates. Again, in the interests of productivity, Amada designs add-ons to improve workstations. At EuroBLECH 2016, Amada has chosen to introduce one of its latest-generation robotic solutions: the HG-1003ARs, equipped with the new AC300 unloading module. This automated bending process perfectly illustrates all the productivity and safety enhancements you can achieve with a press brake, while boosting and improving operator safety. This leaves more time for other tasks like preparing for the next component.
3i for Industry 4.0
It goes without saying that all of these bending solutions incorporate all the latest digital technology developed by Amada over a number of years, in line with industry innovations gearing up towards the factory of the future, “Smart Factory” or “Industry 4.0" All the latest evolutions of the Amada bending solutions that will support sheet metal working business are waiting for your attention at EuroBLECH 2016.